In the complex and demanding field of industrial piping systems, the 36 blind flange emerges as an essential component celebrated for its reliability and efficiency. These robust flanges are integral to numerous industries including oil and gas, petrochemicals, and water treatment, owing to their unmatched capacity to provide a secure seal even under high-pressure environments.
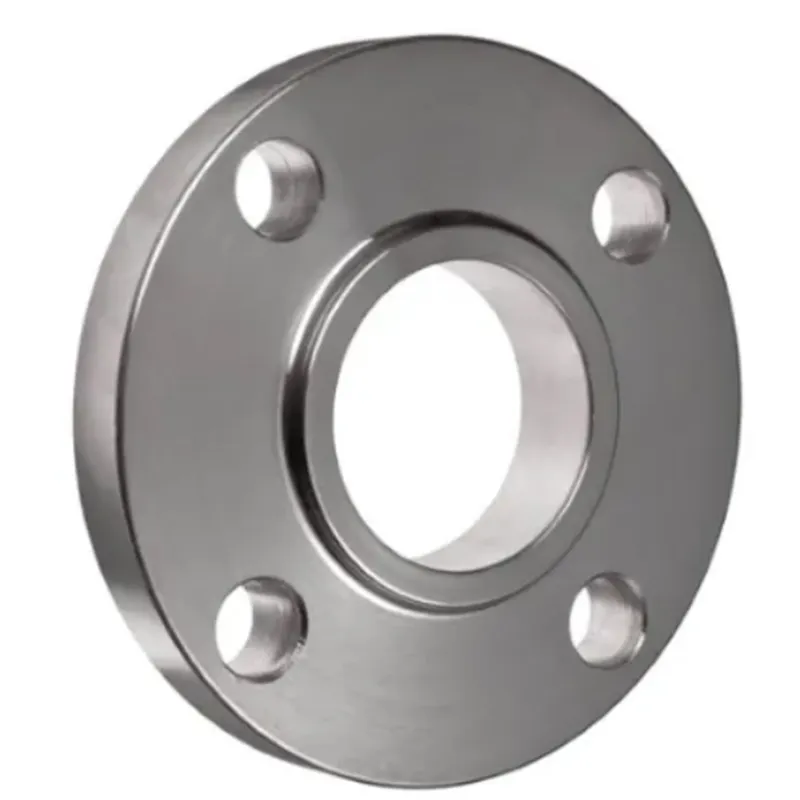
A 36 inch blind flange, with its sizable diameter and flat, solid surface, is specifically designed to terminate or close off piping systems, serving as a cap that prevents the flow of liquid or gas. This functionality is crucial during maintenance, repair, or shutdowns, as it allows for isolation without disrupting the whole system. It is these moments where the reliability and functionality of a blind flange are put to the test, and those with authentic experience handling such components can attest to the blind flange's unmatched efficiency in maintaining system integrity.
From a professional standpoint, the design and manufacturing of a 36 blind flange adhere to stringent industry standards such as the ASME B16.5 or B16.47. These specifications ensure that each flange not only meets but often exceeds performance requirements under a variety of challenging conditions. Experts universally acknowledge the importance of compliance with these standards, as non-compliance can lead to catastrophic failures.
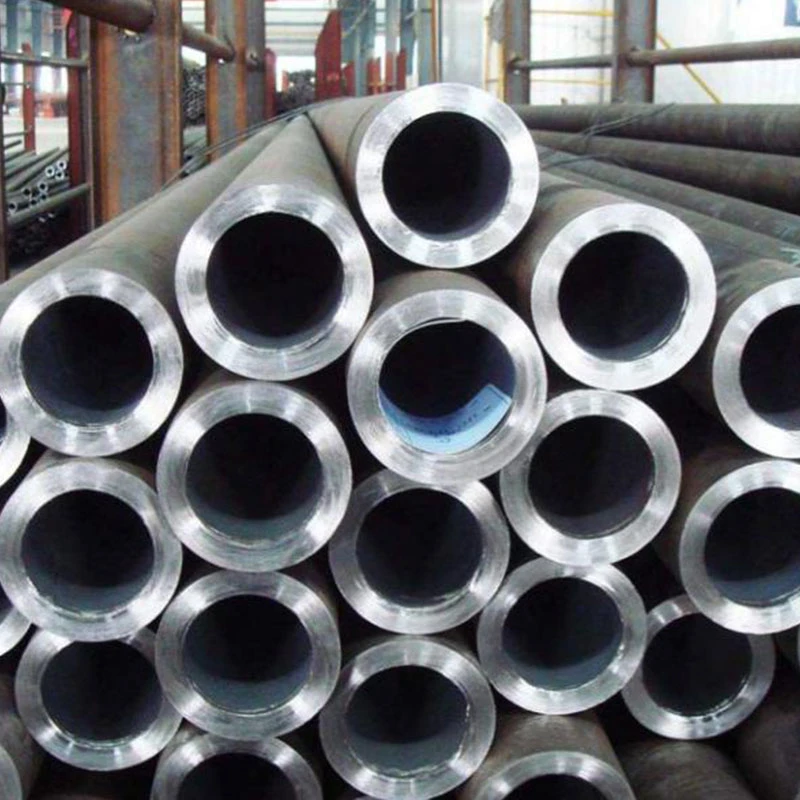
The material used in constructing a 36 inch blind flange is another fundamental aspect ensuring the flange performs optimally. Typically, these flanges are crafted from stainless steel, carbon steel, or alloy steel, chosen based on the specific requirements of the industry in which they’re employed. For instance, stainless steel is often favored in environments where corrosion resistance is paramount. Acknowledging the impact of material science in flange manufacturing is an area where professionals display their expertise, providing insight and recommendations tailored to specific industrial needs.
Within the context of industrial best practices, the importance of flange testing cannot be overstated. Pressure testing, typically performed during the manufacturing process, ensures that each 36 blind flange can withstand the pressures it will encounter once installed. This step is critical in affirming the flange's durability and efficacy, providing stakeholders with the confidence that their systems are safeguarded against leaks and potential failures.
36 blind flange
Trustworthiness in the realm of piping and flanges is heavily reliant on both the manufacturer’s track record and the certifications they hold. Companies producing 36 blind flanges that are ISO certified exemplify a commitment to quality assurance processes. These certifications provide an elevated level of confidence for purchasing managers and engineers who depend on the flange's performance in their projects.
The authority of any provider of 36 inch blind flanges is often measured by customer testimonials and case studies. A history of successful implementations across high-profile projects can turn a manufacturer into a trusted industry leader. This aspect of authority also speaks to the collaborative ethos between flange providers and their clients, ensuring that each application is addressed with precision and expertise.
In an industry where each component must operate flawlessly under extreme conditions, the 36 blind flange stands out for its simplicity, efficiency, and robust design. It embodies a solution that offers peace of mind and trusted performance, hallmarked by years of expert evolution in design and engineering.
For those who work with or are considering using 36 inch blind flanges, understanding these facets—from design specifications and material choices to testing standards and manufacturer certifications—is not merely advantageous; it is imperative. It is this comprehensive knowledge and dedication to quality and standards that underscore the critical role these flanges play across industries worldwide, affirming their place as a trusted component in the integrity of piping systems.