Blind flanges play a crucial role in a variety of industrial applications, serving as a vital component in piping systems, pressure vessels, and more. Their primary function is to seal off or block the end of a pipe or vessel, ensuring the containment of gases or liquids and maintaining system integrity. Understanding the different types of blind flanges can greatly impact the efficiency and safety of industrial processes. This article delves into the various blind flange types, their applications, and why selecting the correct one is essential for operational success.
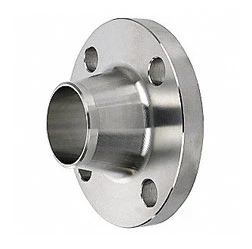
Blind flanges are traditionally circular plates with mounting holes but without a central bore, designed to prevent the flow of substances by sealing the openings of pipelines. They come in various materials, sizes, and pressure ratings, each suited for specific applications. The effectiveness of a blind flange lies not only in its ability to block the flow but also in its adaptability to high-pressure environments and different types of media.
Standard blind flanges are often constructed according to specifications such as ASME/ANSI, DIN, and JIS, which ensure compatibility and safety in their application. The choice of material—be it carbon steel, stainless steel, or alloy steel—depends significantly on the operational conditions, including temperature, pressure, and the type of fluid or gas in the system. Stainless steel blind flanges, for example, are favored for their corrosion-resistant properties, making them ideal for chemical processing applications.
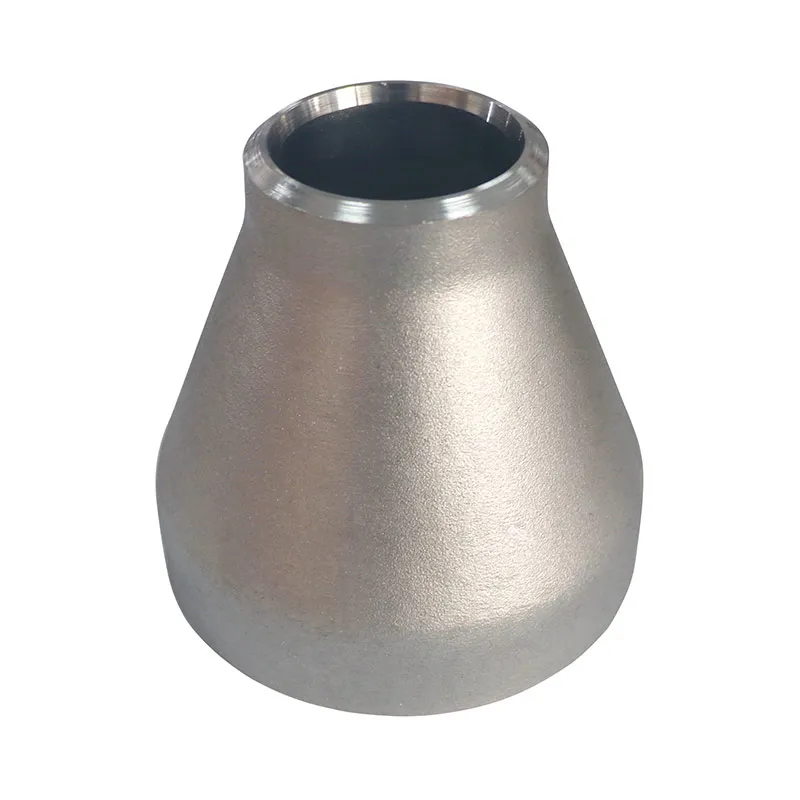
Several variations of blind flanges are available, each designed to cater to specific needs within industrial setups.
The raised face (RF) blind flange is one such type, renowned for its enhanced sealing capabilities. The raised face feature provides a better grip and efficiency when used with gaskets, making it a popular choice in situations requiring high leak prevention, such as in oil refineries or petrochemical industries.
Another well-regarded type is the ring-type joint (RTJ) blind flange. This design includes a groove cut into its face, accommodating a metal ring that deforms to create a strong seal. RTJ blind flanges are particularly suited for high-pressure environments, where leak prevention is paramount. They are commonly used in oil and gas applications, providing a reliable seal under extreme pressures and temperatures, thus ensuring the safety and efficiency of operations.
blind flange types
For environments that demand both a quick installation and removal process, flat face (FF) blind flanges are optimal. Their simple structure allows for ease of handling and installation, often in lower pressure applications where mechanical robustness is not as critical. These flanges are typically found in water treatment plants and HVAC systems, where ease of maintenance and cost-effectiveness are priorities.
In the realm of high-efficiency and precision-demanding scenarios, the customization of blind flanges plays a significant role. Custom designs can accommodate unique requirements, such as non-standard dimensions, bespoke pressure ratings, or specialized coatings. This capability allows industries to tailor their flanges to specific operational conditions, enhancing performance and prolonging the lifespan of the flange.
It is important to consider that the success of a blind flange not only lies in the choice of type and material but also in its adherence to maintenance and inspection protocols. Regular checks for wear and corrosion, proper installation practices, and compatibility verification with the existing system are essential to ensure long-term efficacy and safety. Neglecting these aspects can lead to failures, operational downtimes, and costly repairs.
Blind flanges, in essence, are more than just end caps for pipelines; they are integral to the safety and flow efficiency of an entire system. By choosing the appropriate type, ensuring high-quality materials, and adhering to stringent maintenance practices, industries can achieve better safety standards and operational reliability. As industrial needs evolve, so too will the technology and designs of blind flanges, continuing to safeguard and optimize industrial processes across the globe.