Navigating the intricate world of industrial components, EN 1092-1 flanges stand out as a vital element in the convergence of piping systems across various sectors. These circular devices, adherent to European standards, are engineered with precision to facilitate the seamless connection, termination, and control of pipelines, ensuring efficiency and safety. Understanding the complexities of EN 1092-1 flange specifications can significantly impact operational success, given their pivotal role in maintaining system integrity under varying pressures and temperatures.
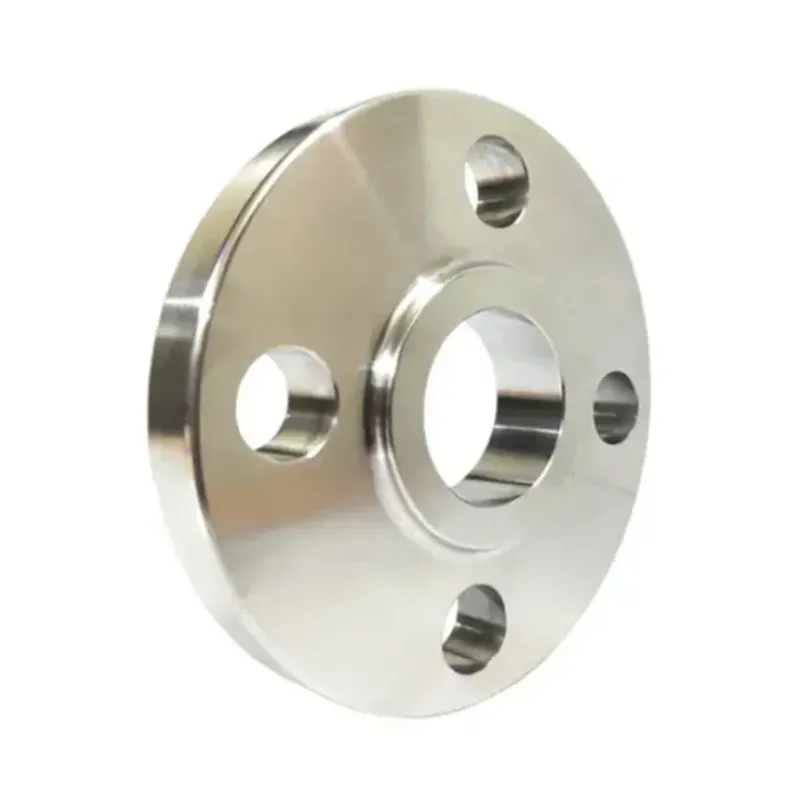
EN 1092-1 flanges are prevalent across industries such as oil & gas, petrochemicals, power generation, and water treatment, where reliability and performance are paramount. The standard outlines numerous aspects of flange construction, including types, materials, dimensions, and pressure ratings, providing a comprehensive framework that addresses the diverse needs of industrial applications.
When delving into EN 1092-1 specifications, the flange types are a key consideration. They encompass the likes of welding neck flanges, slip-on flanges, blind flanges, socket weld flanges, threaded flanges, and lap joint flanges. Each design serves a specific function and is chosen based on criteria such as ease of installation, pressure handling capabilities, and alignment requirements.
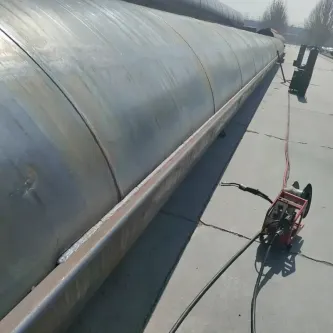
Welding neck flanges are frequently employed in high-pressure environments due to their robustness and ability to withstand extreme temperatures. Their tapered hub and butt-welded connection ensure optimal strength, making them suitable for critical pipeline applications. Slip-on flanges, though easier to install due to their simplistic design, work best in low-pressure settings where precise alignment isn’t a chief requirement.
Blind flanges, utilized to cap the ends of pipelines, prove indispensable during maintenance and system shutdowns. Their convenience is unparalleled when it becomes necessary to halt flow or isolate a section of the pipeline for inspection or cleaning purposes. Threaded flanges are ideal when welding is not feasible, providing a strong and reliable connection through their internal and external thread conformations.
The material composition of EN 1092-1 flanges further defines their suitability for specific applications. Materials range from carbon steel, alloy steel, and stainless steel, to non-ferrous metals such as aluminum and copper alloys. Each material grade brings distinct attributes, contributing to the flange’s resistance to corrosion, heat, fatigue, and wear.
en 1092 1 flange specifications
Understanding the pressure ratings, denoted through PN numbers like PN6, PN10, PN16, PN25, and so forth, is crucial for ensuring that the selected flange matches the operational demands of the piping system. These ratings correlate to the flange’s ability to withstand pressure in bar units at an ambient temperature, guiding engineers and purchasers in aligning their choices with the system’s specifications.
Authenticity in sourcing EN 1092-1 flanges can mean the difference between operational success and costly downtime. Manufacturers with ISO certifications and a track record of compliance with international quality standards are often preferred, providing assurance of longevity and performance. Through rigorous material testing and adherence to precise production protocols, these manufacturers ensure that each flange meets the high expectations set by EN standards.
Moreover, the adaptability of EN 1092-1 flanges enhances their appeal. Alongside standard specifications, custom manufacturing is a pathway many companies explore to cater to unique operational needs. This flexibility, combined with an unwavering commitment to quality, positions EN 1092-1 flanges as a cornerstone in industrial piping systems the world over.
For those navigating the procurement process of EN 1092-1 flanges, expert consultation remains invaluable. Engaging with specialists who offer insights into flange selection, material compatibility, and regulatory compliance can greatly enhance the strategic implementation of these components. These interactions not only foster a deeper understanding but also steer organizations towards making informed decisions that align with their engineering objectives and budgetary constraints.
In today's competitive industrial landscape, where the margin for error is ever-narrowing, the importance of implementing the right flange type with precise specifications cannot be overstated. As industries continue to evolve, embracing technological advancements while adhering to stringent safety standards, EN 1092-1 flanges will undoubtedly remain pivotal in the orchestration of efficient and sustainable pipeline systems.