Alloy 625 fittings are a cornerstone in industries characterized by their demanding operational environments, such as oil & gas, aerospace, and chemical processing. Renowned for their exceptional resistance to harsh conditions, these fittings have carved out a significant niche, promising durability and reliability where it matters most.
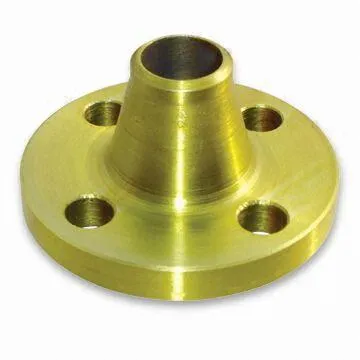
Experience speaks volumes,
especially when considering the numerous applications of Alloy 625 fittings. In the oil and gas industry, for example, these fittings must withstand the corrosive effects of both seawater and the various chemical substances involved in extraction and processing. Installation and maintenance teams have noted the stark contrast between Alloy 625 components and those made from less resilient materials. Downtime and maintenance costs are reduced, directly impacting profitability and operational efficiency. Companies that have relied on traditional materials have often found themselves revisiting installations to replace corroded components, a problem significantly mitigated with the use of Alloy 625.
From a technical expertise standpoint, the composition of Alloy 625 plays a pivotal role in its desirability. The alloy is primarily composed of nickel and chromium but also includes molybdenum and niobium, which enhance its mechanical properties. It is this unique composition that affords Alloy 625 its remarkable resistance to oxidation and corrosion, even at elevated temperatures. Engineers and metallurgists alike praise its versatility, highlighting its suitability not just for fittings, but also for various types of welding applications. This compatibility makes it a preferred choice for complex systems where seamless integration and durability are paramount.
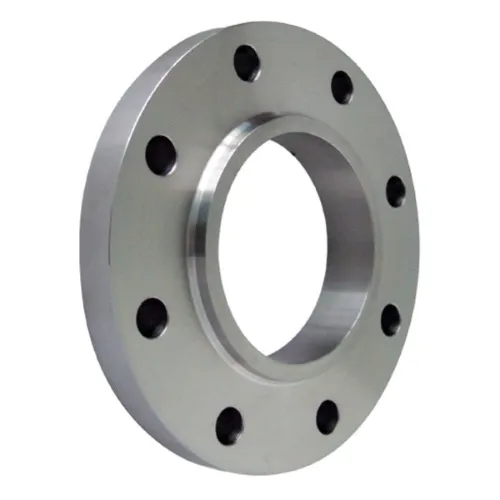
Understanding the authoritative nature of Alloy 625 fittings requires a look at the historical context and the rigorous standards set by regulatory bodies. The alloy was first developed in the context of the aerospace industry, where performance standards are notoriously stringent. Its adoption into other sectors is a testament to its performance and reliability. Today, Alloy 625 conforms to multiple international standards, including those set by ASTM and ASME, providing assurance to stakeholders regarding quality and safety. Such endorsements from standardizing organizations serve as a seal of approval, reassuring engineers, procurement specialists, and end-users of the product's credibility.
alloy 625 fittings
Trustworthiness, in this context, is derived from both the technical superiority and the extensive field testing that Alloy 625 fittings have undergone. Testimonials from industry experts often cite their superior performance in high-stakes scenarios—like deep-sea exploration or jet engine components—where failure is not an option. In environments where conditions are unpredictable and can change rapidly, having fittings that are resistant to cracking, pitting, and stress-corrosion failures is vital.
Furthermore, certifications and third-party testing offer additional layers of verification. Manufacturers often engage in rigorous independent testing to substantiate claims about the performance and lifespan of Alloy 625 fittings. These tests typically assess parameters such as tensile strength, ductility, and resistance to various forms of corrosion. The results consistently confirm the superior nature of Alloy 625, thus fostering trust with end-users.
In conclusion, Alloy 625 fittings represent not only the pinnacle of corrosion-resistant materials but also embody the values of experience, expertise, authority, and trustworthiness. Their continued use across a range of demanding industries is a testament to their unparalleled performance and reliability. For buyers, engineers, and stakeholders seeking solutions that offer both longevity and peace of mind, Alloy 625 stands out as a quintessential choice.