Round pipe welding is an essential process in numerous industrial applications, playing a crucial role in sectors such as construction, automotive, aerospace, and pipeline engineering. A comprehensive understanding of this technique is invaluable for ensuring structural integrity, longevity, and safety of welded structures. This article delves into the various aspects of round pipe welding, examining its principles, benefits, challenges, and the advancements in technology that are transforming the field.
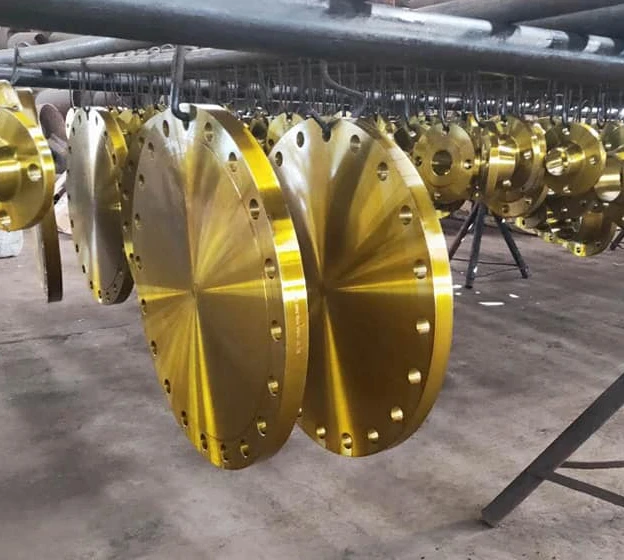
Round pipe welding is characterized by its application on cylindrical surfaces, requiring precision and skill. The welding process must accommodate unique challenges associated with the geometry of round pipes, such as maintaining weld continuity and controlling heat distribution. Several welding techniques are utilized for round pipes, including TIG (Tungsten Inert Gas), MIG (Metal Inert Gas), and stick welding, each offering distinct advantages depending on the material and application.
TIG welding is often preferred for round pipes requiring high precision and a clean finish. This technique allows for control over the heat input and weld pool, making it ideal for thin-walled pipes and delicate materials such as stainless steel and aluminum. MIG welding, on the other hand, is favored for its speed and efficiency, particularly in applications involving thicker materials or large-scale projects. Stick welding remains a versatile choice for outdoor worksites or situations where equipment portability is a factor.
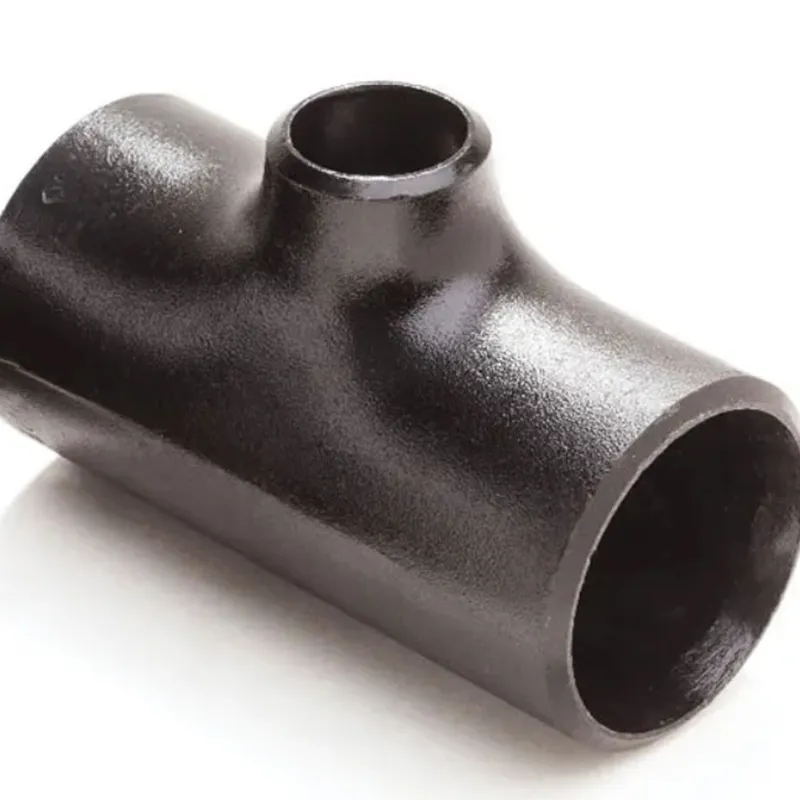
The benefits of effective round pipe welding are numerous. Properly executed welds provide optimal strength and durability, essential for high-pressure environments like water or gas pipelines. A well-crafted weld ensures a seamless joint, minimizing the risk of leaks or structural failure. Moreover, round pipe welding allows for design flexibility, enabling the construction of complex systems with varying pipe diameters and configurations.
Despite its benefits, round pipe welding presents several challenges. One of the primary concerns is achieving consistent weld quality around the pipe circumference. Welders must compensate for gravitational effects on the molten weld pool and maintain a steady hand to avoid defects. Additionally, ensuring adequate penetration without causing excessive distortion or burn-through requires meticulous control of welding parameters.
Advancements in technology are addressing many of these challenges, revolutionizing the practice of round pipe welding. Automated welding systems and robotic arms are increasingly employed to deliver precision and repeatability, reducing human error and labor costs. These systems are equipped with sensors and feedback mechanisms that adjust parameters in real-time, ensuring optimal weld quality.
round pipe welding
Welding simulation software is another technological advancement providing significant advantages. These programs allow welders to visualize the welding process, predict potential issues, and refine techniques before actual production. Simulation technology enhances training and skill development, equipping welders with the expertise needed to navigate the complexities of round pipe welding.
Material innovation is also playing a pivotal role in round pipe welding. The development of advanced alloys and composite materials is driving changes in welding practices, necessitating new techniques and parameters. Constant research and testing are vital to understand the interactions between these materials and various welding processes, ensuring safe and effective applications.
In order to maintain high standards in round pipe welding, adherence to industry regulations and standards is crucial. Organizations like the American Welding Society (AWS) and the American Society of Mechanical Engineers (ASME) provide guidelines and certifications that define best practices and ensure weld quality. Compliance with these standards is a testament to a company's commitment to safety and excellence.
The importance of skilled welders cannot be overstated. Proper training and certification are essential for producing reliable welds and preventing accidents. Continuous professional development helps welders stay abreast of technological advancements and industry trends, further enhancing their expertise and trustworthiness.
In conclusion, round pipe welding is a specialized field that demands a blend of technical skill, precision, and innovation. The integration of technology and adherence to rigorous standards are essential for overcoming challenges and leveraging the benefits of this critical process. As industries evolve and new materials emerge, the future of round pipe welding promises continued advancement, driven by expertise, authority, and an unwavering commitment to quality and safety.