Selecting the correct flange and its types is critical to ensuring the durability and efficiency of piping systems. Among the many options available, slip-on flanges and weld neck flanges are two of the most commonly used types. While both serve the purpose of connecting pipes, valves, and other equipment, they differ significantly in design, strength, installation process, and ideal applications. This article explores the key differences between slip-on flanges and weld neck flanges to help you make an informed choice.
What is a Slip-On Flange?
A slip-on flange (SOP flange) is designed to fit over the pipe, with the pipe extending slightly beyond the flange. It is welded on both the inner and outer surfaces to secure the connection.
Advantages of Slip-On Flanges:
Ease of Installation: Slip-on flanges are straightforward to install, as they do not require precise pipe cutting or beveling.
Cost-Effectiveness: Their simple design and minimal material usage make them more affordable compared to other flange types.
Flexibility: Suitable for pipes of slightly varying dimensions, they offer flexibility during installation.
What is a Weld Neck Flange?
A weld neck flange (WN flange) features a long, tapered neck that transitions gradually into the pipe. This design provides additional strength by distributing stress evenly between the flange and the pipe. The neck is butt-welded to the pipe, creating a seamless connection.
Advantages of Weld Neck Flanges:
High Strength and Durability: The tapered neck and butt-welded connection make it ideal for high-pressure and high-temperature systems.
Reduced Stress Concentration: The gradual transition minimizes the risk of stress-related failures, making it suitable for critical applications.
Long-Term Reliability: Weld neck flanges are highly resistant to fatigue and corrosion due to their robust design.
Slip-On Flange vs. Weld Neck Flange: Key Differences
1. Design and Structure
Slip-On Flange: Features a flat or slightly raised surface that the pipe slides into before welding.
Weld Neck Flange: Includes a tapered neck that ensures a gradual transition between the flange and the pipe, enhancing mechanical strength.
2. Welding Requirements
Slip-On Flange: Requires fillet welds on both sides, which are less complex and faster to execute.
Weld Neck Flange: Requires a butt weld, which is more labor-intensive and demands greater precision.
3. Strength and Durability
Slip-On Flange: Suitable for low-pressure and low-temperature systems but lacks the strength for high-stress applications.
Weld Neck Flange: Designed to handle high-pressure and high-temperature environments due to its robust construction.
4. Applications
Slip-On Flange: Ideal for general-purpose applications such as water pipelines and HVAC systems.
Weld Neck Flange: Preferred in critical industries like oil and gas, where system integrity is essential.
5. Cost Considerations
Slip-On Flange: More affordable due to less material usage and simpler installation.
Weld Neck Flange: Higher cost but offers unmatched durability and long-term performance.
Choosing the Right Flange for Your System
Factors to Consider:
Operating Pressure and Temperature:
Use slip-on flanges for systems with lower pressures and temperatures.
Opt for weld neck flanges for high-pressure, high-temperature environments.
Criticality of the System:
For non-critical systems, slip-on flanges offer an economical solution.
For critical systems where failure is not an option, weld neck flanges are the safest choice.
Installation and Maintenance Costs:
Slip-on flanges are cost-effective and easier to install, saving on labor costs.
Weld neck flanges require skilled labor but provide long-term cost savings due to their durability.
Material Compatibility:
Both flanges are available in various materials such as stainless steel, carbon steel, and alloys to suit different environments.
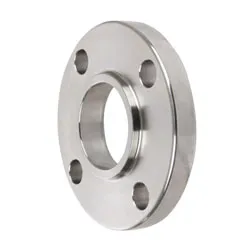