In the world of industrial manufacturing and construction, stainless steel welded pipes are frequently a topic of paramount importance. They embody the perfect blend of durability, versatility, and efficiency that industries require for a wide array of applications. While many consider them a fundamental component, exploring the specifics behind their utility and the advantages they offer reveals the depth and breadth of their significance in both current and future contexts.
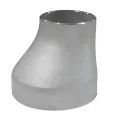
Stainless steel welded pipes, often heralded for their excellent resistance to corrosion, provide an invaluable resource in settings exposed to moisture and various environmental factors. This resistance not only extends the lifespan of projects but also ensures minimal maintenance, contributing to both safety and economic efficiency. The importance of corrosion resistance is highlighted in sectors like chemical processing, oil and gas, and marine environments where failure due to corrosion can have catastrophic consequences.
From a manufacturing perspective, these pipes are notable for their malleability and ease of production. The welding process, which typically involves techniques such as TIG (Tungsten Inert Gas) and MIG (Metal Inert Gas) welding, allows for precision in creating strong, seamless welds that maintain the integrity of the material. This capability is crucial when pipes need to meet stringent regulatory requirements, particularly in industries that transport hazardous materials.
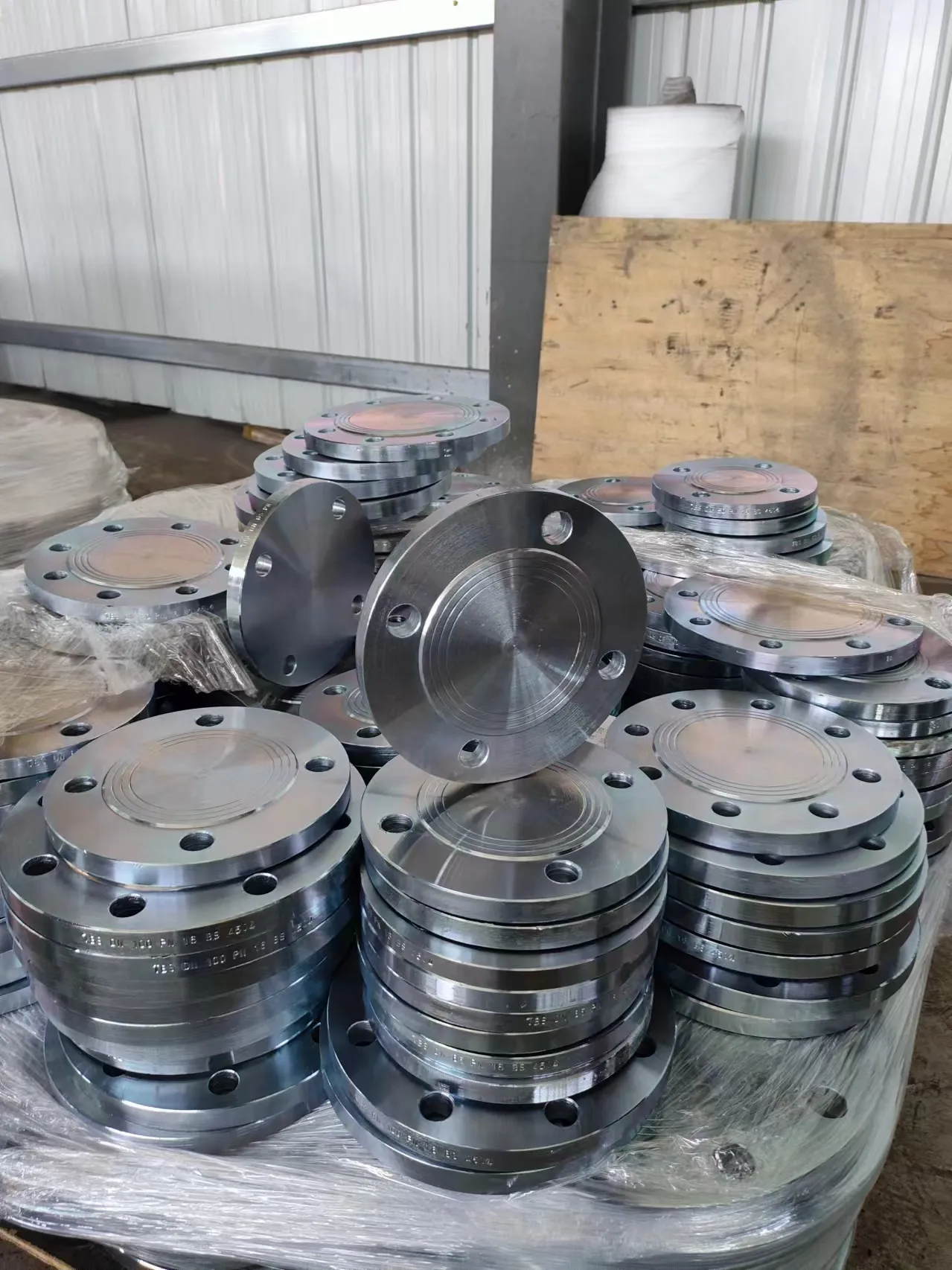
Incorporating stainless steel welded pipes into infrastructure projects is a decision often informed by both their mechanical properties and their aesthetic appeal. Architects frequently choose stainless steel for visible installations because its sleek, modern appearance aligns with contemporary design paradigms. Beyond aesthetics, these pipes bring a high tensile strength, which makes them suitable for high-pressure applications. They are also highly resistant to high temperatures, broadening their applicability from industrial to domestic heating systems.
On the frontlines of innovation, manufacturers are continuously striving to enhance the efficiency and quality of stainless steel welded pipes. Advances in technology have introduced 3D modeling and computerized simulations into the welding process, allowing for unprecedented precision and customization. This innovation reduces error rates and production time, fostering a more sustainable production environment.
ss welded pipe
The expertise in producing these vital components is not just limited to advanced technology but is also deeply rooted in the know-how of skilled professionals. Certified engineers and technicians employ a comprehensive understanding of metallurgy and engineering principles to ensure that each pipe meets necessary quality standards. Their expertise is vital in testing and verifying that each product can withstand specific physical and environmental stresses, thus maintaining a high standard of trustworthiness in various applications.
The authoritativeness of stainless steel welded pipes in industrial use stems not only from their material properties but also from their adherence to international standards. Conformity to standards such as ASTM, ASME, and ISO ensures a level of reliability that is respected across the globe. Regulatory bodies oversee these standards to ensure products are consistently safe and effective for use. Trust in these standards ensures that whether the pipes are used in harsh geographical locations or under intensive industrial processes, they will deliver on performance expectations.
Real-world experience showcases that transitioning from traditional materials like galvanized steel to stainless steel welded pipes has delivered measurable improvements in projects ranging from urban infrastructure to expansive agriculture systems. Feedback from operators and engineers highlights an overall decrease in long-term operational costs and a marked improvement in system integrity and safety.
In conclusion,
stainless steel welded pipes stand as a testament to the fusion of material science and practical application. Their unique combination of performance, durability, and adaptability positions them as a pillar in modern industrial and construction efforts. Forward-thinking companies that invest in these pipes not only benefit from improved efficiency and safety but also position themselves advantageously in markets that increasingly prioritize quality and reliability. The continued evolution of these products, driven by expert knowledge and compliance with stringent standards, ensures their relevance and essentiality in the modern world.