Flanges are essential components in many industrial applications, providing a reliable connection between pipes, valves, pumps, and other equipment. Understanding the various types of flanges is crucial for selecting the right components for your projects and ensuring system integrity and reliability. This guide delves into some of the most common flange types, accompanied by vivid descriptions to help distinguish their unique features.
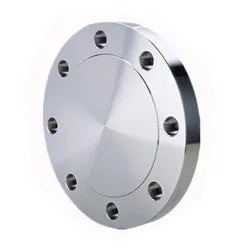
Slip-On Flanges are widely favored due to their simplicity and ease of installation. They slide over the pipe and are typically welded both inside and outside to ensure a secure connection. Ideal for lower pressure applications, these flanges can be found in various industries that prioritize cost-effectiveness and straightforward assembly. Their design allows for easy alignment and fitting, although they might not be suitable for high-pressure systems due to potential leaks from weld imperfections.
Weld Neck Flanges stand out for their long, tapered hub that gradually merges with the pipe, distributing stress evenly between the flange and the pipe. They are preferred in high-pressure and high-temperature environments, such as in petrochemical and power generation industries. The unique design of weld neck flanges ensures minimal turbulence at the joint and offers excellent mechanical stresses resistance, making them a long-lasting and reliable choice in demanding applications.
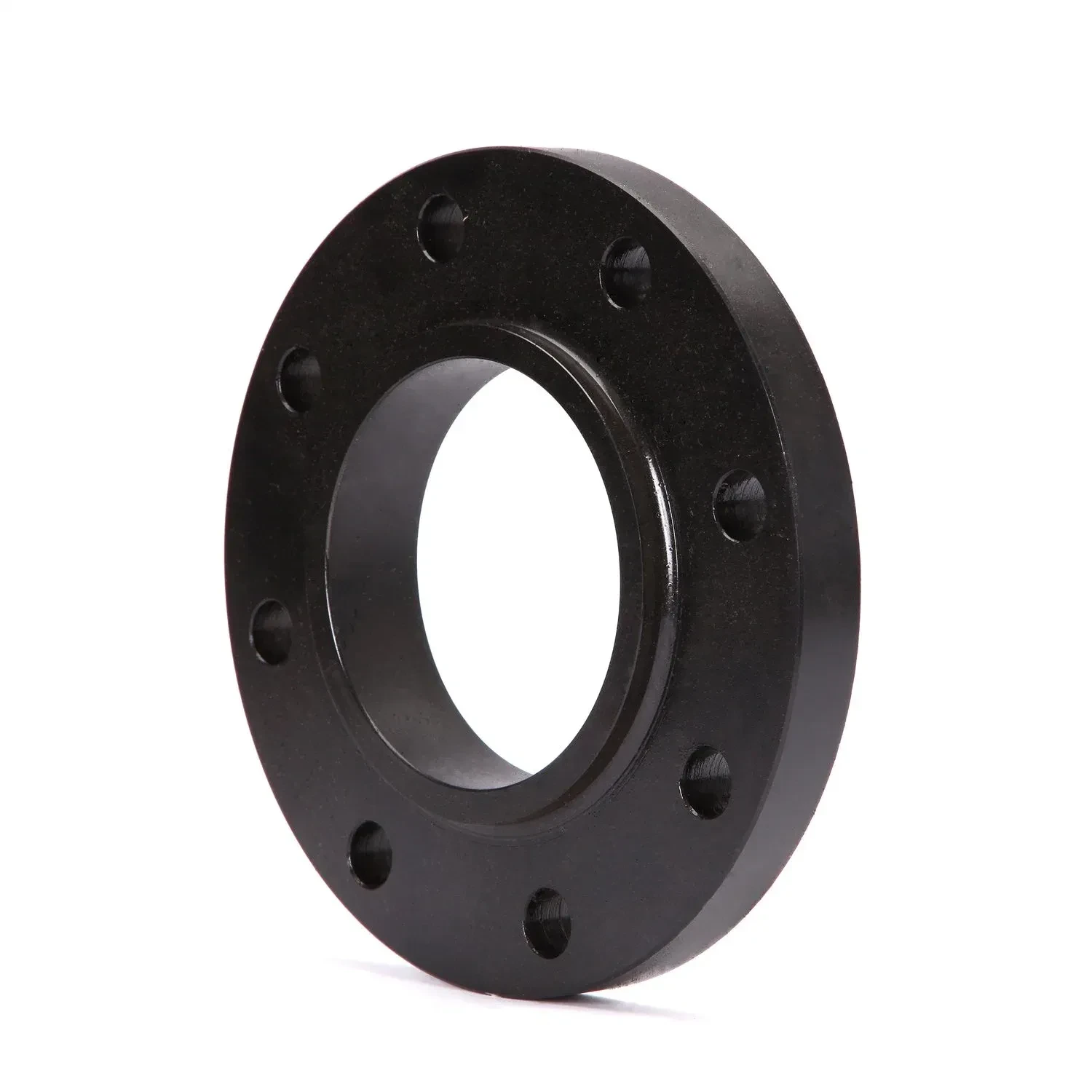
Blind Flanges are used to close the end of a piping system or a vessel opening, providing an easy way to access the line when maintenance is required. Without a center opening, blind flanges are perfect for systems that need frequent isolation or where future expansions are planned. Their solid construction makes them suitable for high-pressure applications, and they can be drilled to accommodate pressure testing.
types of flanges with pictures
Socket Weld Flanges are designed for smaller pipe sizes and are ideal for high-pressure systems. The pipe is inserted into the flange before being fillet welded around the top. This design ensures a smooth bore and improved flow characteristics within the pipeline. Industries such as chemical processing often rely on socket weld flanges for their dependability and ease of assembly without requiring precise alignment or machining.
Lap Joint Flanges are used in conjunction with a corresponding stub end. These flanges are not directly welded to the pipe, which allows them to swivel around the pipe for easy alignment. This feature is particularly useful in systems where frequent disassembly is required for maintenance or inspection. While their initial installation involves a higher cost due to the need for an additional component (the stub end), lap joint flanges can reduce overall project costs and complexity in systems that require adaptable connections.
Threaded Flanges cater to systems in which welding is not feasible. They fit on pipes with matching external threads, providing a reversible connection that's easy to assemble and disassemble. Though they boast convenience, threaded flanges are typically applied in low-pressure systems due to the risk of leakage at the threaded joint. Their most recognizable applications can be found in plumbing and low-stress environments.
Each flange type brings its own set of advantages suited to specific environments and operational demands. By analyzing the needs of your system and understanding the strengths of each flange type, you can ensure optimal functionality, safety, and longevity in industrial applications. Manufacturers and engineers should prioritize selecting flanges based on pressure ratings, material compatibility, and industry standards to enhance system performance and integrity. Trusted sourcing from reputable suppliers further ensures the quality and credibility of flanges used in any critical infrastructure.