Weldable pipes are an integral component in various industrial applications and constructions where reliable joint performance and durability are essential. Selecting the right weldable pipe for any project requires an understanding not just of the material properties, but also insights into their practical applications in the field. This article delves into these aspects, guided by industry expertise and experience.
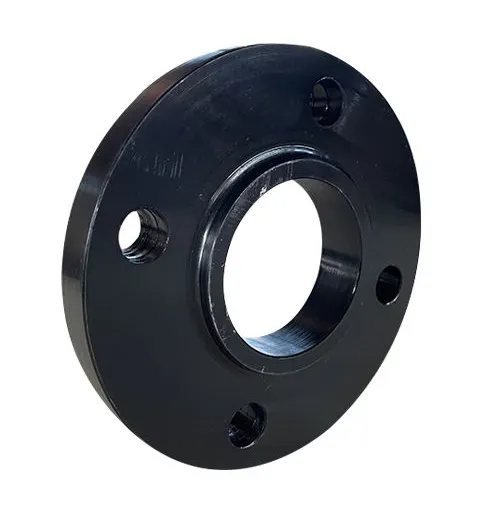
Weldable pipes come in a variety of materials, including steel, aluminum, and titanium. Each material offers unique advantages depending on the application. Steel weldable pipes, for instance, are renowned for their strength and durability, making them a preferred choice in construction and infrastructure projects. Aluminum pipes, on the other hand, are lightweight and resistant to corrosion, often used in applications where weight is a consideration, such as in aerospace or automotive industries.
One critical factor for weldable pipes is the ease and effectiveness of the welding process. With the utilization of advanced techniques such as TIG (Tungsten Inert Gas) and MIG (Metal Inert Gas) welding, achieving a strong, precise joint is feasible. These methods ensure that the material properties of the pipe are maintained, reducing the risk of defects and increasing overall joint integrity.
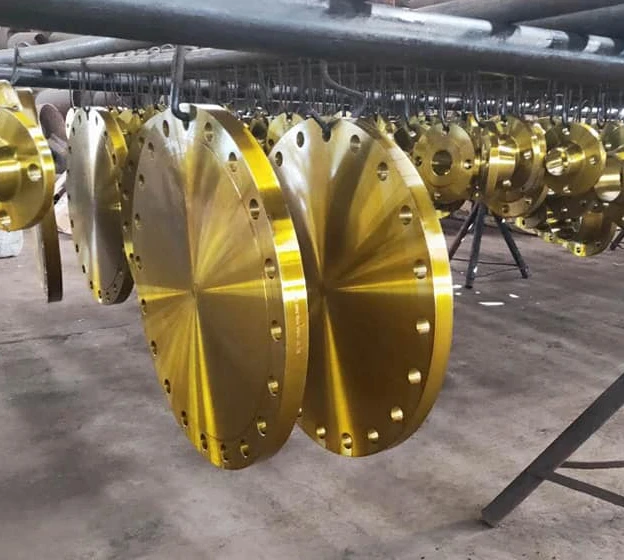
Welding expertise is essential for ensuring optimal performance of weldable pipes. Skilled welders understand the nuances of different welding techniques and can adjust parameters like temperature, speed, and gas flow to accommodate the specific properties of the pipes being used. This adaptability ensures that welders can handle a variety of situations, from repairing pipelines to constructing complex frameworks.
The role of quality assurance cannot be overstated when it comes to weldable pipes. To guarantee the safety and reliability of these components, companies often employ rigorous testing standards. Non-destructive testing methods such as ultrasound or radiography are employed to detect any inconsistencies or weaknesses in the welds, which further assures the integrity of the welded joints. Regular inspections and certifications by authoritative bodies add another layer of trustworthiness, ensuring that these pipes meet stringent industry standards.
weldable pipe
In the market, the manufacturer's reputation plays a pivotal role in the perceived quality and reliability of weldable pipes. Trusted brands tend to have rigorous production processes, robust quality assurance protocols, and a track record of reliability, providing peace of mind to contractors and engineers who depend on these products for safe and effective constructions.
Furthermore, environmental and economic considerations are influencing the evolution of weldable pipe technology. Sustainable production methods and recyclable materials are increasingly being integrated into manufacturing processes. This not only reduces environmental impact but also offers cost benefits in the form of reduced waste and recycled materials.
End users of weldable pipes benefit from a wealth of resources and support provided by leading manufacturers and suppliers. Many companies offer detailed manuals, on-site training, and 24/7 customer support to ensure that their products are used safely and effectively. Such comprehensive support structures amplify the expertise available to contractors and technicians and enhance the overall project success rate.
As innovations in materials science and welding technology advance, the future of weldable pipes appears promising. Continued research and development efforts are expected to result in pipes that offer even greater durability, ease of use, and sustainability, further solidifying their status as a cornerstone of construction and industrial applications.
In conclusion, weldable pipes are indispensable in numerous industries due to their versatility, strength, and adaptability. A robust understanding of the materials and welding processes, combined with an emphasis on quality assurance and manufacturer reliability, ensures that projects utilizing these pipes are executed with the highest standards of safety and efficiency. Whether in large infrastructure projects or specialized applications, weldable pipes remain an essential tool in achieving structural integrity and durability.