Welding pipes to flat plates is a crucial task in various industries, including oil and gas, shipbuilding, construction, and manufacturing. Mastering this skill requires understanding both the intricacies of welding techniques and the unique materials handling required for a seamless bond. As someone with extensive experience in welding, I aim to convey vital insights to help you achieve superior results.
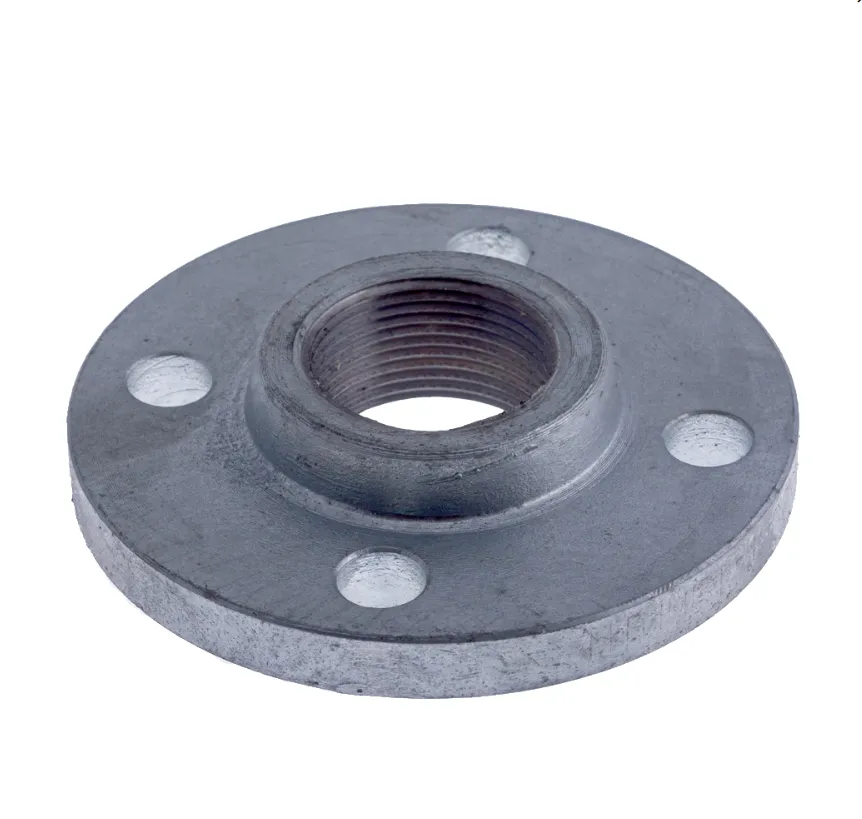
Successfully welding a pipe to a flat plate begins with choosing the right welding technique. Methods such as TIG (Tungsten Inert Gas) welding, MIG (Metal Inert Gas) welding, and SMAW (Shielded Metal Arc Welding) each have distinct advantages depending on the materials and applications involved. For thin-walled pipes, TIG welding is praised for its precision and clean results, while MIG welding can offer speed and efficiency suitable for thicker materials.
Proper material preparation cannot be overstated. The surfaces of both the pipe and the flat plate must be thoroughly cleaned to remove any rust, oil, or paint. This ensures a strong bond and minimizes the risk of defects. Additionally, aligning the pipe and plate correctly is paramount. Utilizing fixtures and clamps can help maintain precise alignment and prevent warping during the welding process.
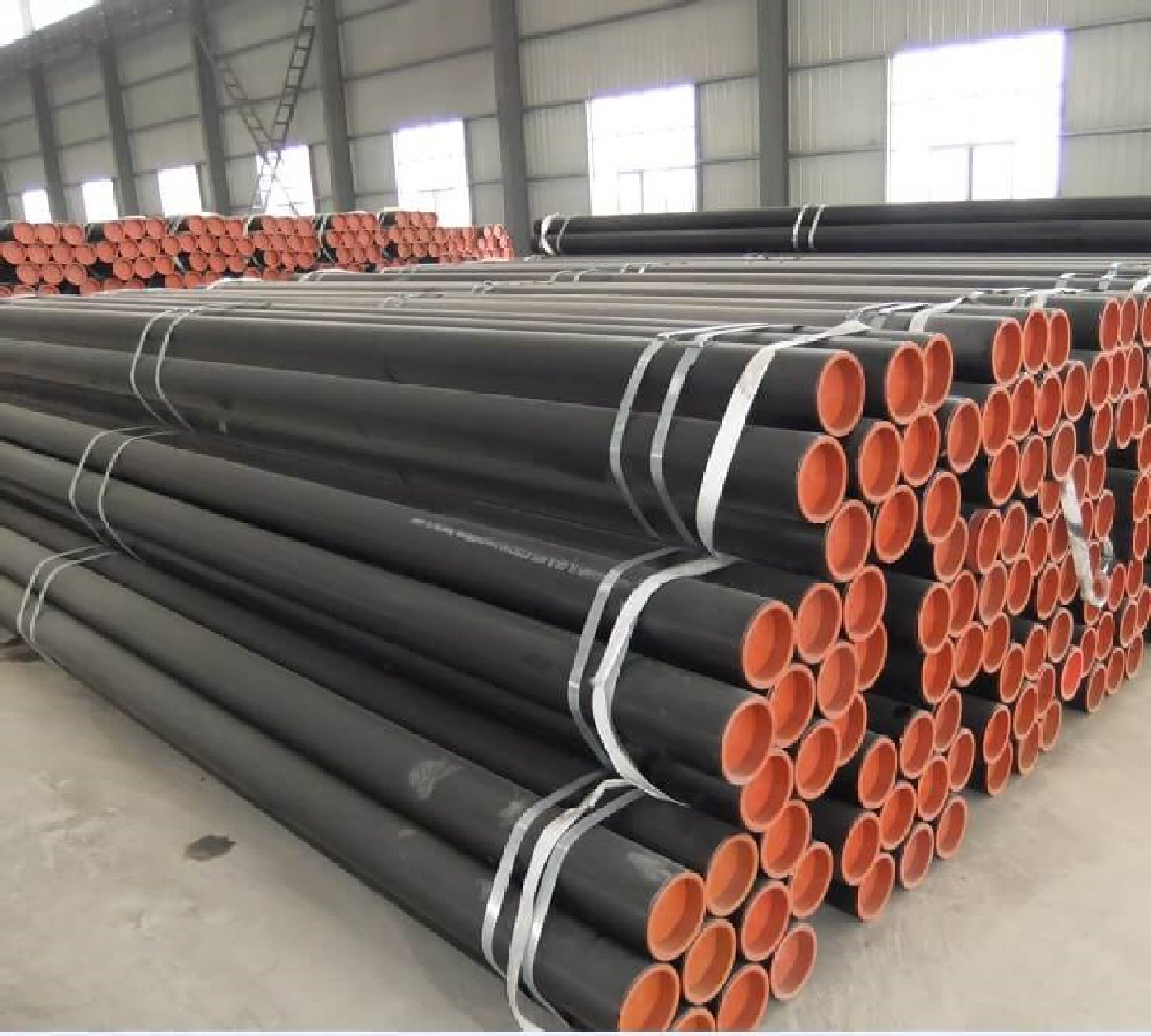
For achieving optimal welds, control over heat input is critical. The heat must be sufficient to create a strong bond but not excessive to avoid warping or compromising the integrity of the materials. Pre-heating the materials can sometimes be beneficial, especially when working with thicker pipes or plates, as it reduces thermal gradient and minimizes stress concentrations at the weld joint.
An authoritative approach to welding involves regularly assessing weld quality. Non-destructive testing methods, such as ultrasonic testing or radiographic inspection, can be employed to ensure the weld integrity is uncompromised. These techniques can detect internal defects that might not be visible to the naked eye, thereby increasing the reliability of the weld.
welding pipe to flat plate
Trust is paramount in this field, and building reliability through consistency and quality control is key. Welding professionals understand that safety is non-negotiable. Therefore, adhering to industry standards and guidelines is essential. Certifications like those from the American Welding Society (AWS) can provide additional credibility and showcase a commitment to quality and safety.
Documentation of the welding process adds to its trustworthiness. Maintaining detailed records of materials used, techniques applied, and inspection results can be invaluable for future reference and for assuring clients of the quality. This transparency not only builds trust but also helps in troubleshooting any potential issues down the line.
Furthermore, innovation in welding technology is allowing us to push the boundaries of what is possible. Automation and robotic welding technologies are increasingly employed to enhance precision and repeatability. While technology offers incredible benefits, there is no substitute for the trained eye and skillful hand of a seasoned welding professional who can adjust to the nuances of each unique task.
In conclusion,
welding a pipe to a flat plate is as much an art as it is a science. By integrating expertise, maintaining high standards, and embracing technological advancements, welding professionals can ensure strong, high-integrity joints that stand the test of time. The principles outlined here form a robust framework for mastering this essential task through a blend of traditional practices and modern innovations.