When selecting components for industrial piping systems, the importance of a reliable and high-quality blind flange cannot be overstated, especially one as specific as a 10-inch blind flange. Often used to terminate the end of a piping run or to seal off a pipe section for maintenance or testing, a blind flange is a critical piece that guarantees the system's integrity and performance.
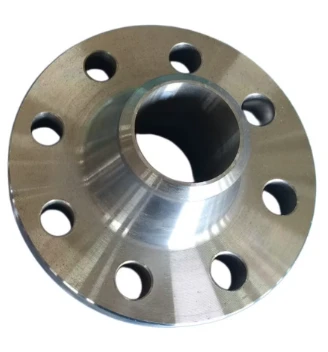
The 10-inch blind flange is especially relevant in industries such as waterworks, petrochemical, oil and gas, and even power generation sectors. Known for their robustness and reliability, blind flanges are indispensable in environments where precision and safety are non-negotiable.
One of the most significant factors contributing to the expertise associated with a 10-inch blind flange is its construction material. Typically made from carbon steel, stainless steel, or alloy steel, these materials are chosen based on their ability to withstand high pressure and temperature variations. Carbon steel flanges are renowned for their affordability and toughness, making them suitable for systems transporting water or other non-corrosive substances. Conversely, stainless steel is appreciated for its corrosion resistance, ideal for more aggressive chemical environments.
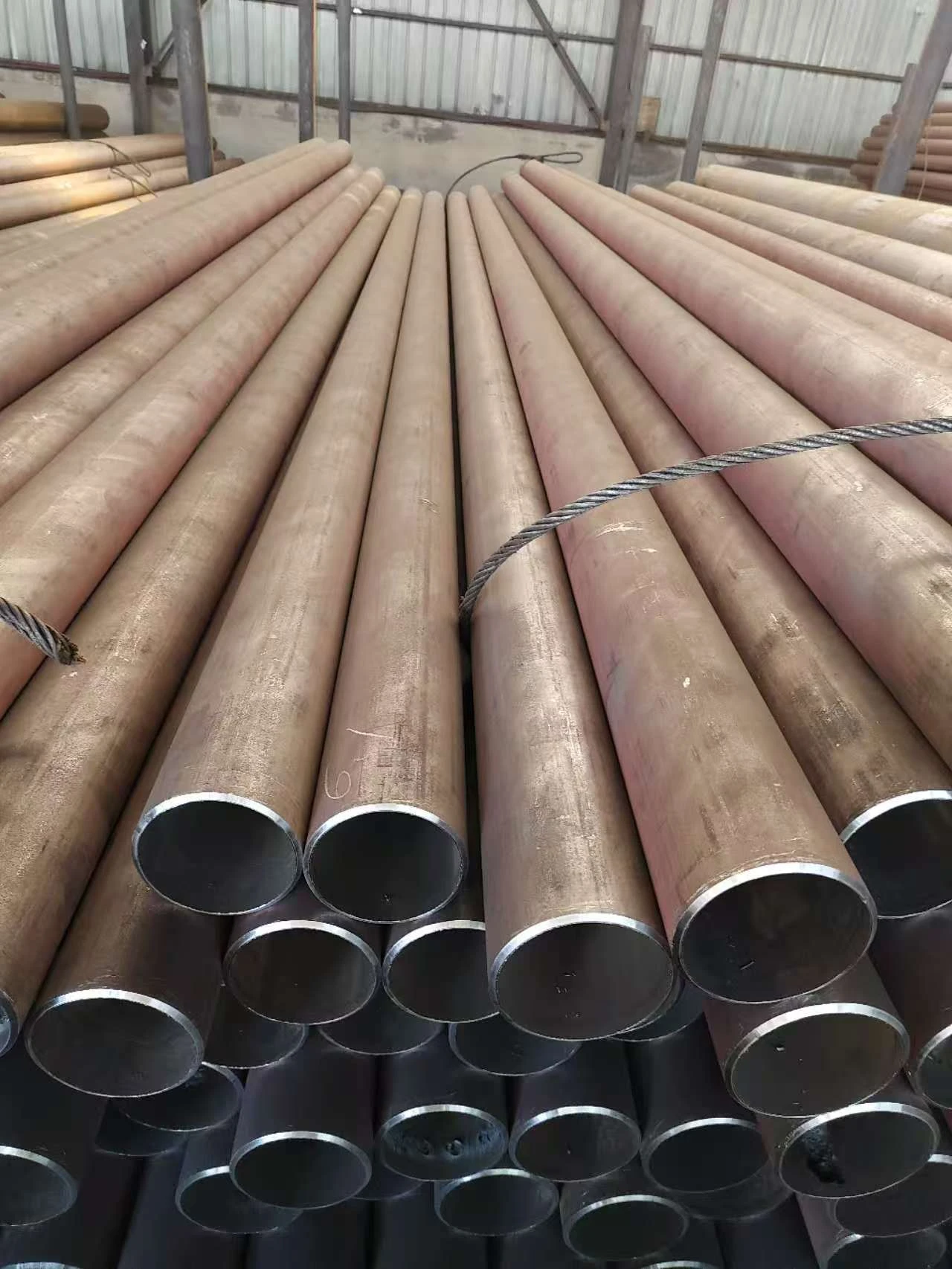
Understanding the various pressure ratings associated with 10-inch blind flanges is crucial. With pressure ratings ranging from Class 150 to Class 2500, each class corresponds to the maximum pressure the flange can handle at a specified temperature. This expertise ensures that professionals can select the right class of blind flange to match the application's needs, enhancing both safety and system efficiency.
From an authoritative viewpoint, the standards governing the manufacture of 10-inch blind flanges are stringent. Organizations like the American National Standards Institute (ANSI) and the American Society of Mechanical Engineers (ASME) set forth specifications that guarantee each flange can endure mechanical stressors specific to its environment. When aligning to standards such as ASME B16.5 for pipe flanges and flanged fittings, the blind flange’s dimensions, materials, and pressure ratings are meticulously regulated. Consumers can trust these flanges to perform dependably across diverse applications by adhering to these standards.
10 inch blind flange
Another aspect contributing to the trustworthiness of 10-inch blind flanges is the manufacturing process. Quality assurance protocols, including non-destructive testing (NDT), are almost invariably implemented to detect surface and subsurface defects. Techniques such as ultrasonic testing, magnetic particle testing, and radiography validate the structural integrity of the flange, ensuring it is primed for safe deployment in high-stakes environments.
Real world experience showcases that while installation may seem straightforward, the inherent skill of proper flange alignment and bolt tightening cannot be underestimated. Even a small misalignment or improper torque can lead to future system failures or leaks, thus emphasizing the need for experienced personnel. Comprehensive experience with blind flanges aids in reducing install-time errors while significantly lowering maintenance costs over the lifecycle of the piping system.
The application versatility of a 10-inch blind flange is also noteworthy. They are not just terminal fittings; with minor modifications, blind flanges can accommodate various needs. For instance, some systems require tapping a blind flange to include drain connections or instrumentation ports. This customization capability underscores the adaptability of the blind flange in solving complex industrial challenges.
Ultimately, investing in a high-quality 10-inch blind flange is not merely about safeguarding immediate project outcomes; it’s about securing the long-term reliability and safety of a crucial industrial infrastructure component. With unmatched expertise and authoritative backing, these small yet significant fittings play a massive part in various global sectors, frequently becoming a defining element of a project's success. When sourced from reputable manufacturers, these flanges indeed epitomize the perfect blend of durability, efficiency, and economy, making them an indispensable asset to any piping system.