Navigating the intricacies of the industrial materials market can be a challenging endeavor, especially when it comes to components as specific as the blind flange. A “blind flange” refers to a solid disk used to block off a pipeline or fitting. This component plays a crucial role in pipeline systems, primarily seen in factories, refineries, and processing plants. Here, we explore the importance, application, and long-term benefits of selecting the right blind flange for industrial projects, rooted in years of experience and expertise.
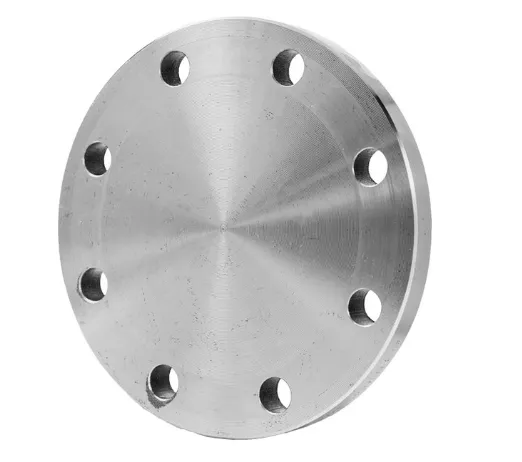
Blind flanges, often unsung heroes in the industrial sector, possess a unique blend of features that elevate their importance beyond mere pipeline accessories. It starts with their primary function—sealing the ends of pipes. This is essential in scenarios where an expansion is anticipated, or an inspection is mandatory. Blind flanges offer the versatility of creating a seal that can be dismantled without the need of cutting operations, ensuring that the integrity of the system remains uncompromised while allowing rapid resumes of operation when needed.
From an expertise standpoint, the versatility of blind flanges is enhanced by the variety of materials they can be manufactured from, including stainless steel, carbon steel, and alloy steel. Each type has its specific advantages stainless steel offers excellent resistance to corrosion, carbon steel delivers formidable strength, and alloy steels provide hardness and durability, depending on the composite materials used. These materials are chosen based on the conditions of their use—whether exposed to harsh chemicals, high pressures, or extreme temperatures—thereby reinforcing their reliability.
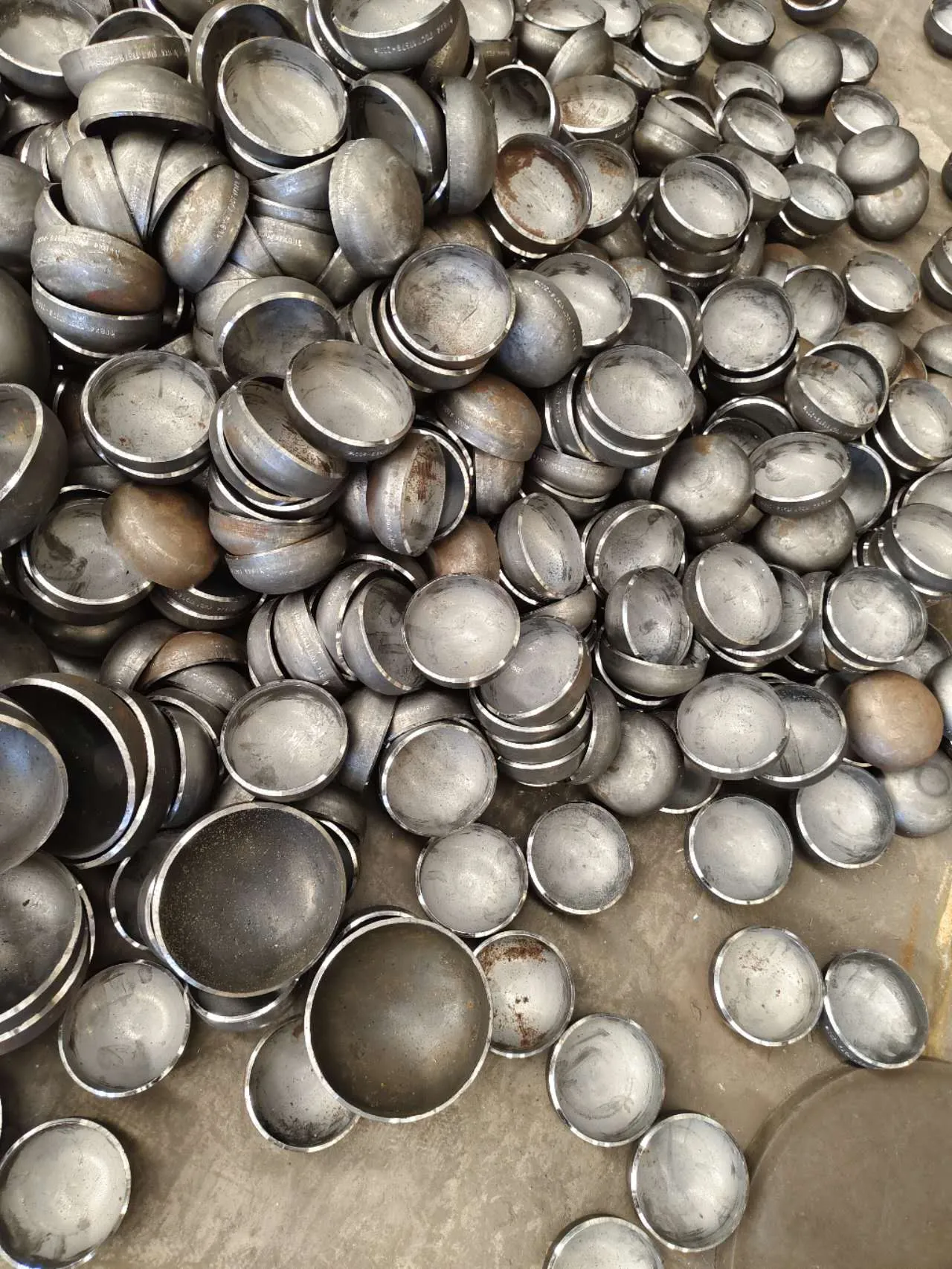
The authoritative nature of blind flange implementation in infrastructure cannot be overstated. In fact, the American National Standards Institute (ANSI) has set rigorous guidelines to ensure that blind flanges meet exact specifications for safety and performance. These standards encompass dimensions, pressure ratings, and material requirements. A misaligned or improperly rated flange could result in dangerous leaks or system failures, emphasizing the critical need for adherence to these standards. Manufacturers committed to these guidelines ensure that each blind flange delivers exceptional performance tailored to specific industrial needs.
5 blind flange
Trustworthiness becomes a key factor when considering suppliers for blind flanges. It is imperative that suppliers are not only ISO certified but also have a verifiable record of quality assurance and customer satisfaction. Long-term partnerships with trusted suppliers can mean the difference between consistent operational success and costly system failures. Reviews and testimonials from industry leaders who have utilized specific blind flange products further cement a supplier’s reputation, while detailed case studies provide insight into real-world applications and challenges resolved through superior product performance.
By selecting the right blind flange, companies maximize efficiency and cut down unforeseen maintenance costs. Properly chosen blind flanges facilitate routine inspections, adapt to modifications in pipeline configurations, and withstand fluctuating operational pressures. Emerging technologies in production are continuously driving improvements in flange materials and designs, ensuring that the components keep up with evolving industry requirements and environmental standards.
Embracing these blind flange solutions goes beyond mere adoption of a product; it involves a strategic approach to integrating these components into existing systems to yield maximum benefits. Continuous educational efforts, led by industry associations and leading manufacturers, aim to guide stakeholders in understanding the critical impact of their choice and application of blind flanges. Such educational initiatives play a vital role in enhancing industry-wide knowledge, thereby elevating the collective expertise on the matter.
In sum, blind flanges are indispensable to the stability and functionality of pipeline systems within industrial operations. Through careful selection, adherence to authoritative standards, and fostering trustworthy supplier relationships, businesses can ensure robust system performance. This strategic focus not only underscores operational dependability but also encapsulates a broader commitment to safe and sustainable industrial practices.