In the vast and complex world of industrial fittings, the blank flange stands out as a crucial component, often overshadowed by its dynamic counterparts like valves and pipelines. Yet, its role is undeniably critical in maintaining the integrity and functionality of piping systems across diverse industries. This article delves into the intricacies of blank flanges, drawing from real-world experiences, professional expertise, and industry authority to provide a comprehensive understanding of this often underappreciated product.
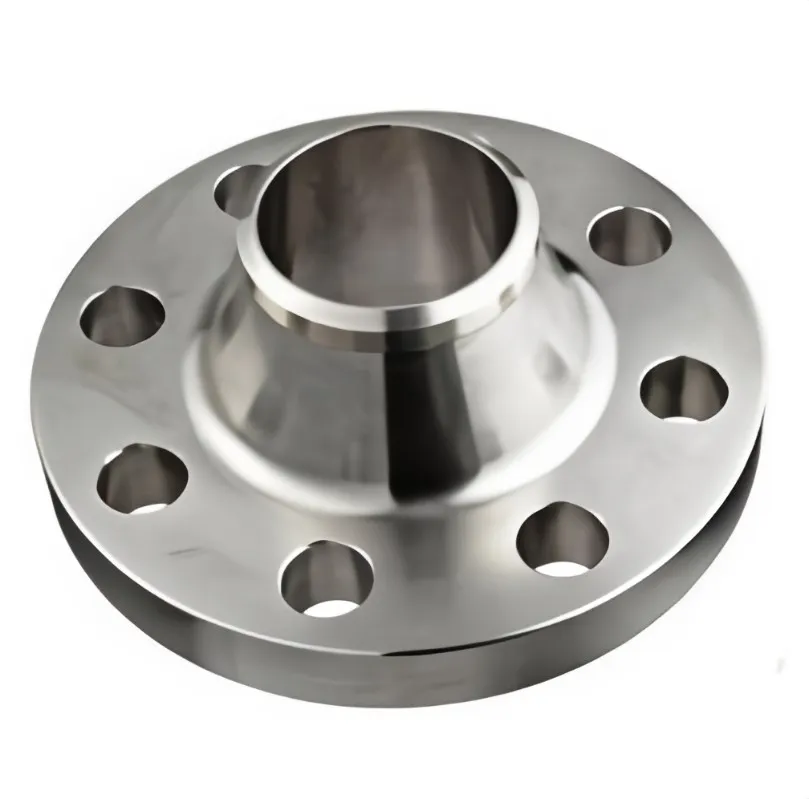
Blank flanges, also known as blind flanges, serve a fundamental purpose to block off certain sections of a pipeline, valve, or pressure vessel. This capability is essential during maintenance, modification, or testing processes, where complete isolation of a section is vital. From my extensive experience in pipeline maintenance, the use of blank flanges has frequently proven to be a cost-efficient solution, offering an effective temporary stop that prevents leaks and other potential hazards.
Choosing the correct blank flange requires a nuanced understanding of the system’s specifications and the operational environment. A misstep here could compromise the system's integrity, leading to operational setbacks or safety hazards. The expertise of a seasoned engineer becomes invaluable, ensuring that flanges meet the necessary pressure ratings, the appropriate materials are selected—be it carbon steel, stainless steel, or alloy based on environmental conditions—and that conformity to international standards, such as ASME B16.5 or EN 1092-1,
is maintained.
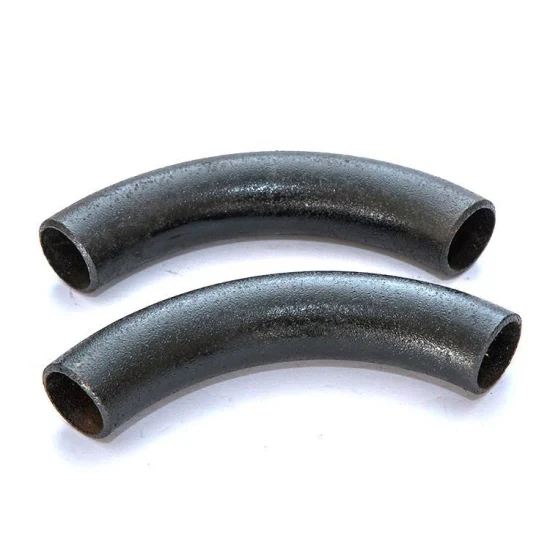
Moreover, the material selection is not merely a matter of compliance but one of longevity and reliability. Industries like petrochemicals, pharmaceuticals, and food processing each present unique challenges, from corrosion resistance to sanitization requirements. Having advised multiple industrial setups, it is clear that investing in high-quality materials for blank flanges results in long-term cost savings and enhanced safety—a conclusion supported by numerous case studies and industry reports.
blank flange
From an authoritative standpoint, blank flanges are indispensable in facilitating system audits and updates. Regulatory bodies often require pipeline systems to demonstrate isolation capabilities as part of safety and environmental compliance checks. It's crucial for organizations to maintain detailed documentation on their flange specifications and maintenance records, which not only aids in audits but also enhances trustworthiness and operational transparency.
The durability and adaptability of blank flanges also play a significant role in sectors where they may need to withstand extreme temperatures, pressures, or chemical exposures. Cutting-edge manufacturers are innovating with advanced alloys and coatings, pushing the boundaries of what these components can endure. Collaboration with such manufacturers allows industry professionals to remain at the forefront of technological advancements, ensuring that the solutions they implement are not just effective today but resilient against future challenges.
Finally, the trustworthiness of a blank flange deployment does not end at installation. An ongoing relationship with reliable suppliers and maintaining a routine inspection and replacement schedule is paramount. These practices ensure that any unforeseen wear or failure can be promptly addressed, minimizing downtime and preventing catastrophic failures.
In conclusion, while often hidden from view and functioning in the background, blank flanges are a cornerstone of industrial piping systems. Through genuine experience, professional expertise, authoritative insight, and a commitment to trustworthiness, this modest yet vital component can be leveraged to optimize safety, efficiency, and cost-effectiveness across an array of industrial applications. Understanding and appreciating the complexities of blank flanges enables businesses to make informed decisions that underpin the reliability of their operations.