The world of industrial piping solutions offers a wealth of options to ensure efficiency, safety, and system integrity. Among these essential components, the blind pipe flange stands out, often being overlooked despite its critical functionality in various applications. This component not only enhances the resilience of piping systems but also provides unparalleled solutions in terms of performance and security.
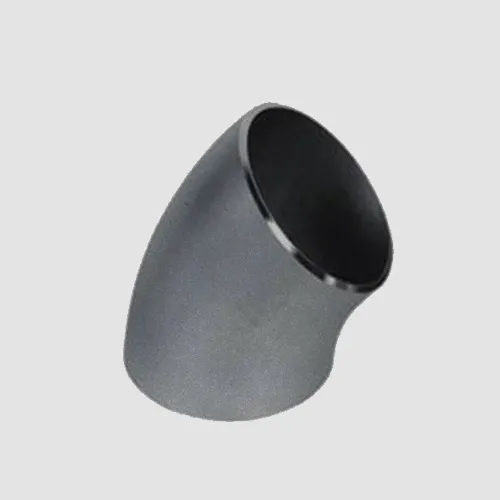
Blind pipe flanges are indispensable for their ability to close off the ends of piping systems securely. Unlike open-ended pipes, a blind flange ensures that no unwanted elements enter or exit a piping system, maintaining the purity and quality of the materials being transported. The design of a blind flange includes no opening for fluids or gases to pass through, creating a secure block. This is particularly beneficial in industries where contamination can incur significant costs or safety hazards, such as food processing, pharmaceutical production, and chemical engineering.
In addition to sealing pipelines, blind pipe flanges play a decisive role in system testing. By terminating one end of a pipe run, these flanges allow systems to be pressurized and checked for leaks without the expense of waste or product loss. This aspect proves crucial for industries that depend on precise pressure systems, including oil and gas, where operational security depends heavily on reliable testing procedures.
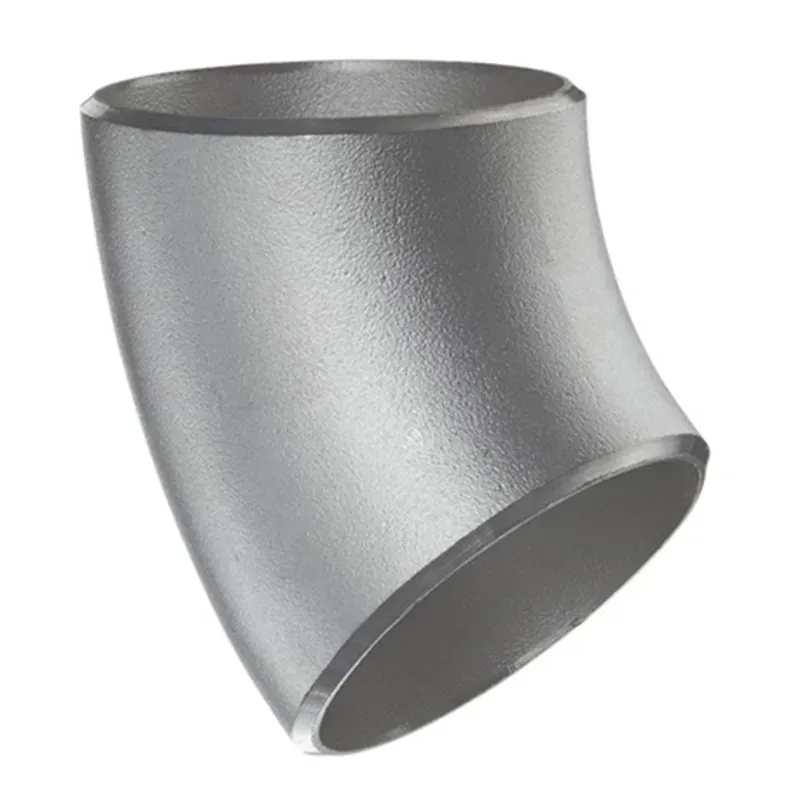
The use of blind flanges also extends to the modification and expansion of existing piping systems. When there's a need to halt the flow temporarily or change the configuration of a system, blind flanges act as placeholders that can be easily removed without disrupting the entire pipeline infrastructure. This facilitates flexibility in the design and maintenance of complex piping networks, saving both time and money.
Expertly crafted blind pipe flanges must adhere to stringent standards to ensure compatibility and safety. Materials selection is of paramount importance, with options ranging from stainless steel and carbon steel to specialty alloys, each chosen for their ability to withstand specific temperature and pressure conditions. Adherence to standards such as ASME B16.5 or B16.47 ensures the flange will perform reliably under designated conditions, signifying manufacturing excellence and providing peace of mind to engineers and operators alike.
blind pipe flange
Beyond their functional attributes, blind pipe flanges are also pivotal in addressing environmental and sustainability concerns. They can prevent leaks that not only waste valuable resources but could also cause environmental harm. In an era where sustainability is as critical as operational efficiency, integrating components that align with eco-friendly practices is not merely an option but a necessity.
Trust in blind pipe flanges extends from their proven reliability under duress in some of the most demanding environments. Testimonials from engineers and operators consistently underscore the importance of choosing high-quality flanges to avoid unforeseen failures and associated costs. Industry leaders know that investing in robust flanges equates to fewer pipeline interruptions and greater long-term savings.
As the world continues to demand more sustainable, efficient, and secure industrial practices, blind pipe flanges remain a key component of the broader system solutions, ensuring safe and efficient operations across diverse applications. Their importance cannot be overstated and is continually reinforced by ongoing innovation in flange technology, designed to meet the ever-evolving demands of global industries.
In conclusion, while often unseen once installed, blind pipe flanges embody Experience through their historical effectiveness, Expertise via engineering precision, Authoritativeness through adherence to international standards, and Trustworthiness by delivering on their promise of security and performance. They are an essential piece of the puzzle in maintaining the integrity and performance of critical pipeline systems.