In the vast realm of industrial applications, the slip blind flange emerges as a pivotal component for ensuring seamless operations and safety. This crucial apparatus not only reflects engineering prowess but also embodies the epitome of reliability and efficiency in various sectors, including oil and gas, petrochemical, and water treatment facilities. To truly appreciate the value this component brings, we delve into its sophisticated design, practical applications, and the undeniable security it offers.
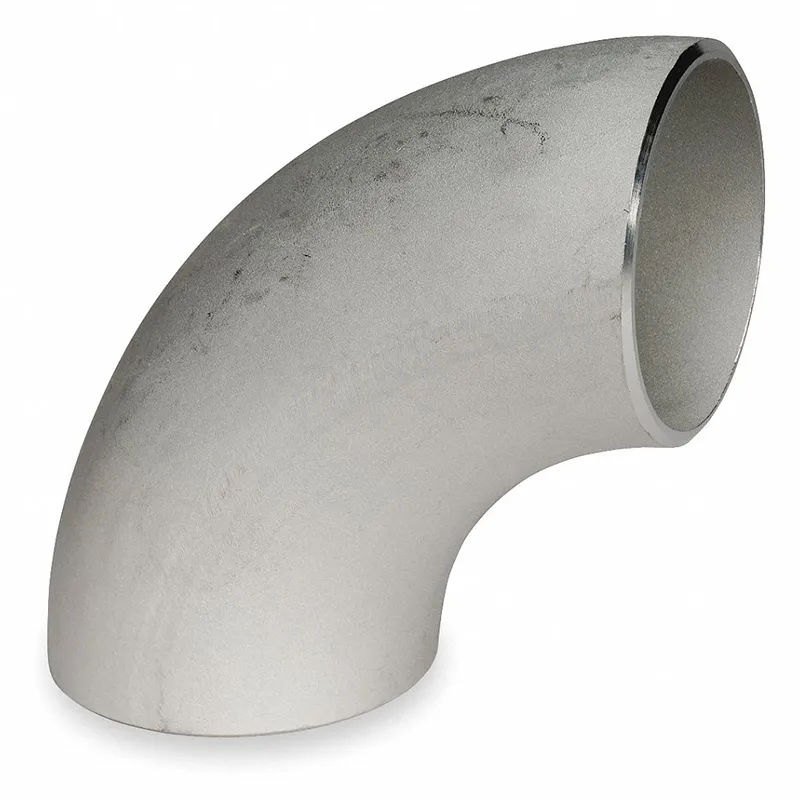
Slip blind flanges are engineered to temporarily close off a pipeline or vessel. What sets them apart from other flange types, like threaded or lap joint flanges, is their unique ability to be slid over the pipe and fixed in place without requiring a completely dismantled line. This feature plays an indispensable role in maintenance and inspection operations, as it ensures that work can be conducted without prolonged downtime, ultimately safeguarding operational continuity.
Expertise in the field of industrial maintenance underscores the critical nature of these components. The design fundamentally incorporates a circular disc, akin to a blind flange, but with an essential modification a hole at the center that allows it to slip over a pipe. Here's where true engineering inventiveness becomes apparent—no two systems are identical, and slip blind flanges are fabricated in various materials, ranging from stainless steel and carbon steel to more specialized alloys. This variety ensures compatibility with different pressure ratings and chemical exposure, thus enhancing their versatility.
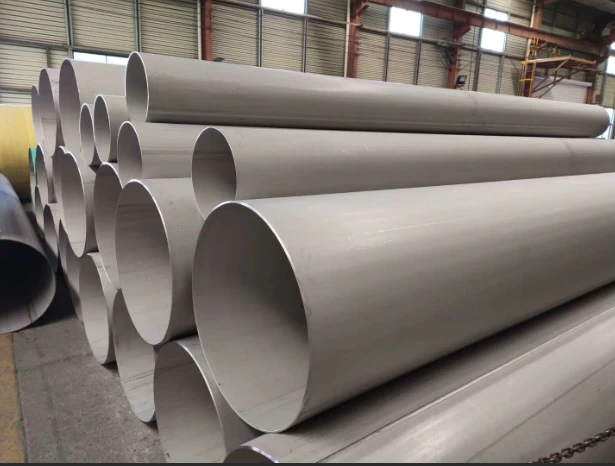
For professionals engaged in system integrity assessments, employing a slip blind flange is a testament to their expertise. They can expertly determine the appropriate moments to isolate a section of piping to perform repair jobs or periodic checks. Such strategic isolation prevents spillage, contamination, or, in severe cases, catastrophic failures that may lead to operational hazards and financial losses. Their adeptness guarantees that the correct specifications of each slip blind flange match the standards and requirements of the pressure system they are safeguarding.
slip blind flange
Within the industry ecosystem, the authoritative voice on slip blind flanges often emanates from seasoned engineers and technicians whose extensive field experience informs the ongoing improvements in flange design. Their insights have driven enhancements like reduced weight for easier handling and the introduction of innovative gaskets and sealing technologies that minimize the risk of leaks, ensuring secure closures and tight fits.
From a trustworthiness standpoint, slip blind flanges stand as a synonym for reliability. The rigorous manufacturing and testing protocols, adhering to international standards such as ANSI and ASME, further affirm their dependability. These standards ensure that each flange can withstand the nuanced demands of high-pressure environments while maintaining an unimpeachable seal. Users can trust that a correctly installed slip blind flange will perform its intended function without compromise.
To paint a broader picture, the demand for slip blind flanges is a reflection of modern industrial operation's gravitation towards systems that balance performance with safety. Industries around the globe recognize the significant safety margins these flanges introduce, aligning with stringent safety regulations. Facilities that prioritize this balance often report not only a reduction in maintenance costs but also enhancements in employee safety and overall workplace morale.
In conclusion, the slip blind flange represents more than a mere component—it's a blend of innovative engineering, expert application, and steadfast reliability. For those seeking superior operational efficiency and safety, its role cannot be overstated. As industries continue to evolve, so too will the technologies around slip blind flanges, ensuring that they meet the future's challenges with the same commendable efficacy they display today.