The threaded blind flange serves as a critical component in various piping systems, primarily used to seal the ends of pipes or openings in pressure vessels. With its unique design and functionality, it caters to industries requiring robust sealing solutions such as the oil and gas, chemical, and petrochemical sectors. Diving into its specificities not only highlights its pivotal role but also underscores the expertise and excellence in manufacturing and material selection essential for its optimal performance.
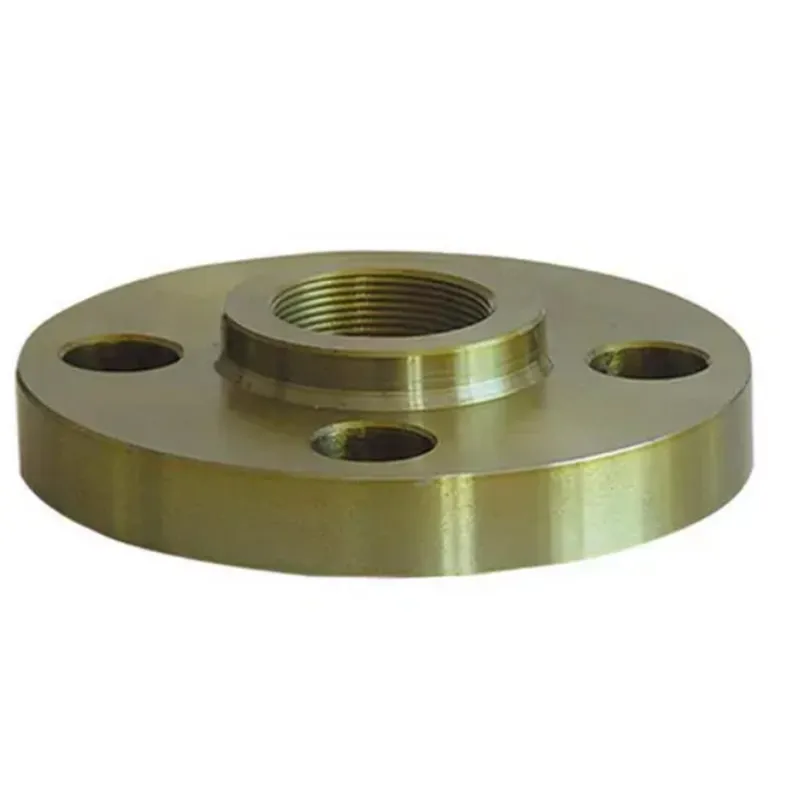
Threaded blind flanges, unlike their slip-on or weld neck counterparts, do not require welding to attach to the system. This inherent feature confers versatility, enabling quick installation and disassembly, which is particularly advantageous in settings where maintenance and inspections are frequent. Experience from field applications reveals that the ability to rapidly replace or assess these components significantly reduces downtime, leading to increased operational efficiency.
An understanding of material selection is pivotal when discussing threaded blind flanges. Typically constructed from materials such as stainless steel, carbon steel, or alloy steel, the choice depends heavily on the service environment. For example, stainless steel is preferred in corrosive environments due to its resistance to rust and chemical degradation. On the other hand, carbon steel offers cost-effectiveness and is suitable for less corrosive applications. Expert insight suggests that careful consideration of the material in relation to the media transported can significantly extend the lifespan of the flange and minimize unforeseen failures.
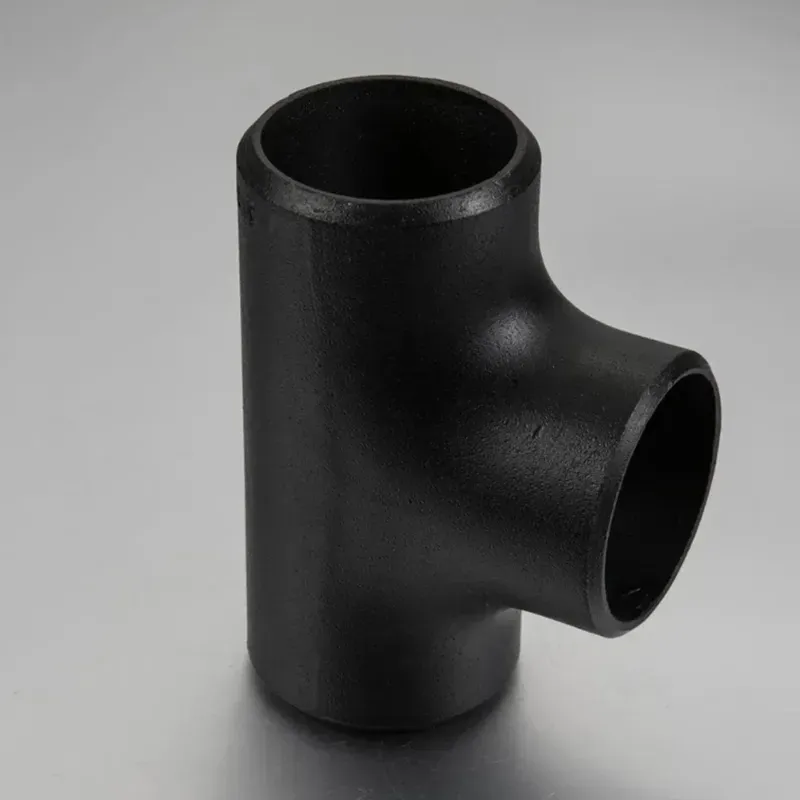
Moreover, industry standards and certifications, such as ASME (American Society of Mechanical Engineers) specifications, guide the manufacturing of these flanges. Adhering to these standards ensures that the flanges can withstand the pressures and temperatures they are exposed to, thus affirming their reliability. Professionals in the field trust these standards as a benchmark of quality, providing assurance that the products they are using are both safe and effective.
threaded blind flange
In terms of design, the threaded blind flange features precision-engineered grooves that allow it to thread directly onto the pipe, providing a tight seal without the need for additional sealing materials. This design minimizes the risk of leakage, a critical factor in high-pressure applications. Expertise in design and engineering plays a crucial role in this aspect, where precision machining and quality control are indispensable in achieving the necessary tolerances that prevent leakages.
The application of threaded blind flanges is extensive, spanning various industries. However, feedback from users highlights their particular effectiveness in the oil and gas sector, where they are used to terminate pressure vessel openings and provide access for cleaning and maintenance. Such feedback not only illuminates their practical applications but also builds trust, as real-world testimonials serve as a powerful indicator of product reliability and performance.
In addition to practical applications, ongoing innovations in manufacturing processes, such as advanced CNC machining and automated quality inspections, further enhance the product’s credibility. These cutting-edge technologies ensure that each flange meets stringent quality standards, providing peace of mind to end-users who rely on these components in critical infrastructure.
In conclusion, the threaded blind flange epitomizes a blend of engineering excellence, material expertise, and practical application. Its design and functionality highlight its indispensability in various industrial environments, while adherence to standards underscores its reliability and trustworthiness. For those in the field, understanding the nuances of threaded blind flanges not only aids in optimal selection and application but also in leveraging their full potential across demanding operational landscapes. Such comprehensive knowledge ensures that the right decisions are made, fostering not only enhanced performance but also safety and longevity in piping systems.