Understanding the Essential Role of Hydraulic Flanges in Modern Machinery
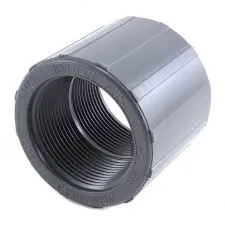
Hydraulic flanges are unsung heroes in the world of industrial machinery. Their robust design and critical function in hydraulic systems ensure their necessity in providing fluid connectivity and high-pressure containment. This article not only delves into the anatomy and functionality of hydraulic flanges but also underscores their indispensable role in myriad applications, focusing on key factors that define their performance and selection criteria.
A hydraulic flange is a critical component in hydraulic systems, positioned at the intersection of piping, tubing, or hydraulic hoses. It serves as an intersection point, channeling hydraulic fluid under pressure with precision and reliability. Understanding the components is essential for choosing a suitable hydraulic flange—tasks that only experts and experienced personnel are adept at accomplishing.
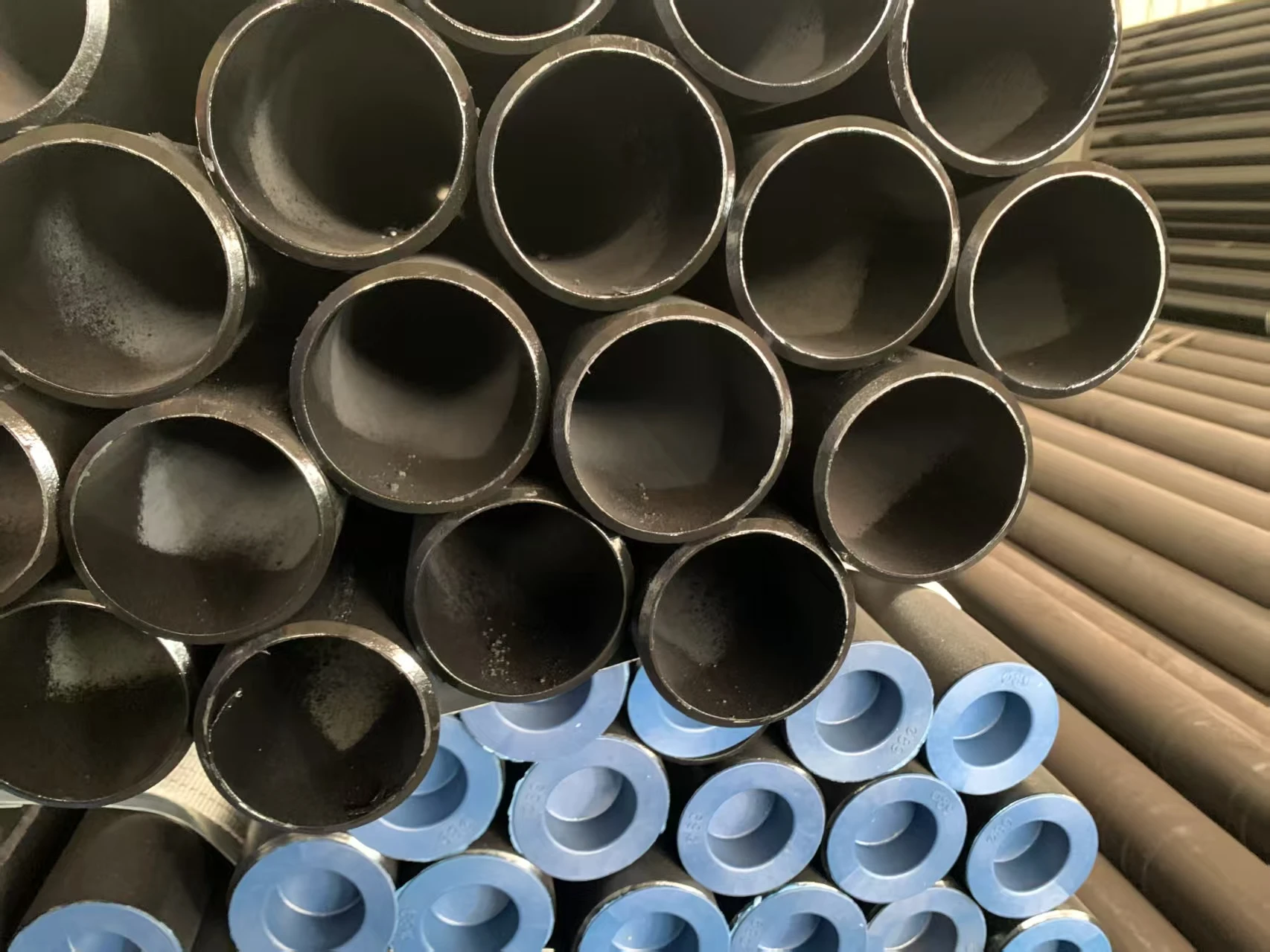
The genealogy of hydraulic flanges spans various shapes and sizes. The most common types include SAE Code 61 and Code 62 flanges, which differ primarily in pressure capacities. Code 61 supports pressures up to 3,000 psi, while Code 62 can withstand up to 6,000 psi. These flanges are designed with four bolt holes, bearing resemblance aesthetically but differing structurally to cater specific pressure conditions.
Selecting the right material for hydraulic flanges is paramount, as it influences longevity and reliability under stress. Carbon steel remains a popular choice due to its affordability and strength, making it suitable for general purposes. However, stainless steel and alloys provide enhanced corrosion resistance and are preferred in sectors like maritime and chemical processing where environmental conditions are harsher.
The design and sealing efficiency of the flange also harbor critical importance. A secure seal is vital to prevent leaks, which can lead to performance drop-offs or outright system failures. O-rings, commonly made from nitrile, fluoroelastomer, or silicone, mate with the grooves on the flange surface to create a formidable barrier against fluid escape, thus maintaining system integrity.
hydraulic flange
Installation methodology further influences the efficiency of a hydraulic flange. Flanges are mounted using bolts and nuts, requiring precise torqueing to ensure the seal is uniformly compressed. Over-tightening can damage the O-ring or even warp the flange, leading to leaks. Conversely, insufficient torque may result in fluid seepage from inadequately compressed seals.
Hydraulic flanges boast versatility across industries, underscoring their application in manufacturing, agriculture, construction, and even aerospace. In manufacturing, precise fluid delivery is imperative for hydraulic presses and automation systems. In agriculture, the hydraulic flanges facilitate the movement of heavy machinery with precision. Moreover, flanges enhance excavators and forklifts' operability by ensuring optimal hydraulic power delivery in construction sectors.
Trust becomes paramount when enterprises select suppliers for hydraulic flanges. Ensuring the authenticity and quality of the flanges is a task best left to reputable manufacturers with a history of compliance with global standards such as ISO 6162 or SAE J518. A credible supplier will provide technical expertise, aiding in the selection and maintenance of components that fit clients’ specific operational demands.
Despite their crucial role, hydraulic flanges require regular inspections and maintenance. Over time, factors like temperature fluctuations and fluid contamination may degrade seals or even warp flanges. Routine checks and part replacements help mitigate these risks, ensuring prolonged equipment life and sustained performance. Enterprises must instill a proactive maintenance regime backed by documentation to keep detailed records of component performance and service histories.
In conclusion, hydraulic flanges serve as vital components ensuring the smooth operation of modern machinery. Their selection, installation, and maintenance should be approached with attention to detail and expert guidance. By understanding the nuances of materials, design, and application, businesses can ensure efficiency, safety, and sustainability in their hydraulic systems. Embracing this knowledge not only fosters trust and reliability but also solidifies a company’s position as a beacon of authority in its respective industry.