DIN 2642 flanges, a type of loose flange often used in piping systems, are integral to various industrial applications. Their unique design and characteristics make them an essential component for professionals working in sectors such as chemical processing, shipbuilding, and water treatment. This article delves into the intricacies of DIN 2642 flanges, emphasizing the four key pillars of Experience, Expertise, Authoritativeness, and Trustworthiness (E-E-A-T).
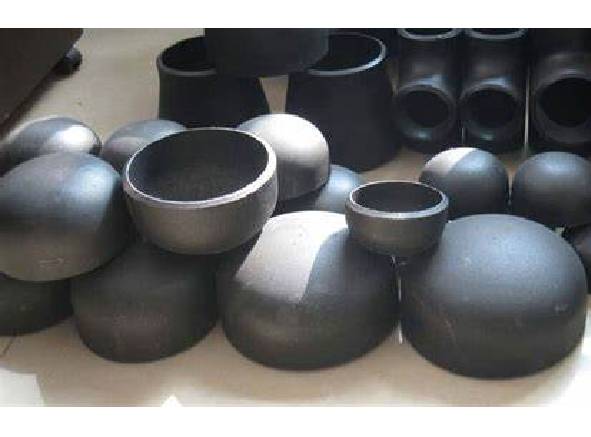
DIN 2642 flanges originate from European standards that are widely recognized and implemented in numerous industries. These flanges are known for their reliable performance in conditions involving high temperature and pressure, making them a preferred choice for engineers looking for robust and adaptable solutions.
One of the principal advantages of DIN 2642 flanges is their ability to simplify pipeline assembly and maintenance. Unlike weld neck or slip-on flanges, these loose flanges provide flexibility. In practical terms, they allow for easy adjustments in pipeline length without the need for intensive cutting or welding operations. This characteristic not only saves time but also reduces labor costs, contributing to overall operational efficiency.
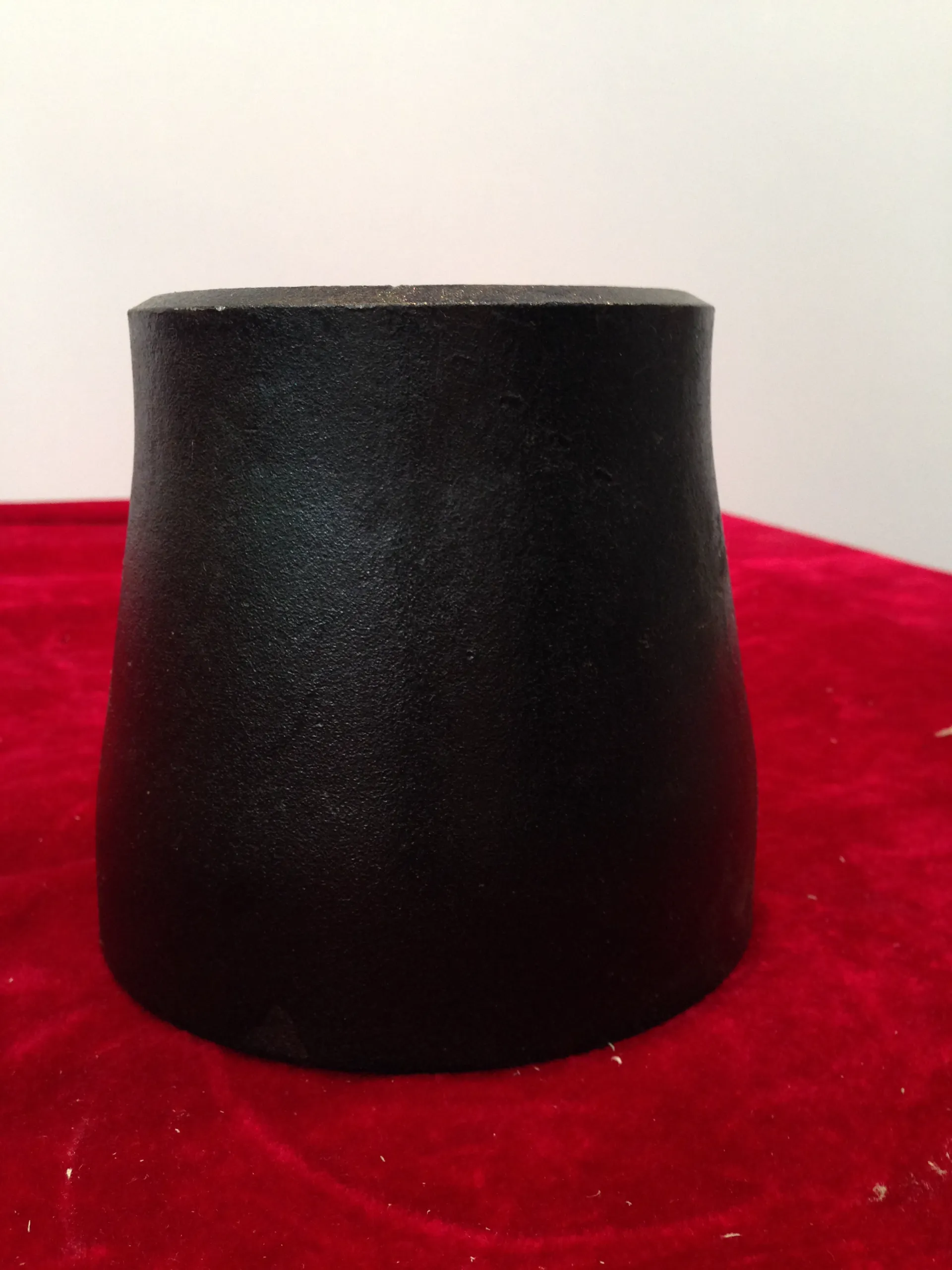
In terms of expertise, DIN 2642 flanges are crafted from a variety of materials, including stainless steel, carbon steel, and alloy, catering to specific industrial needs. Stainless steel variants are particularly popular in industries requiring high corrosion resistance, such as pharmaceuticals and food processing. Alloy flanges, on the other hand, are utilized when enhanced strength and temperature resistance are needed, thus providing users with a diverse range of options to meet rigorous engineering standards.
For professionals seeking authoritative guidance on selecting and installing DIN 2642 flanges, consulting international standards and manufacturing guidelines is crucial. These comprehensive documents offer in-depth information on dimensions, pressure limits, and temperature ratings, ensuring the chosen flange will perform optimally even under demanding conditions. Collaboration with reputable manufacturers who adhere to these standards further enhances the reliability of the installed flanges.
Trustworthiness is another critical aspect when dealing with DIN 2642 flanges. Opting for products from established manufacturers that prioritize quality assurance through stringent testing and certification processes is vital. High-quality DIN 2642 flanges must undergo rigorous inspections that verify their integrity, ensuring they meet or exceed industry benchmarks for safety and performance. Operational tests, material checks, and dimensional accuracy assessments are just a few examples of the quality control measures employed by reputable producers.
din 2642 flange
From practical usage experience, implementing DIN 2642 flanges in piping systems can lead to significant benefits. Many field experts report reduced downtime and maintenance issues due to the easy replacement and alignment capabilities of these flanges. This adaptability translates to cost savings and enhanced productivity, as less time is spent on troubleshooting and repairs.
Moreover, the modular nature of DIN 2642 flanges supports future-proofing of industrial operations. As systems are upgraded or expanded, these flanges simplify the integration process, whether it involves adding new segments or connecting to existing pipelines. This foresight not only safeguards current investments but also aligns with long-term strategic planning.
Innovations in manufacturing technology have also augmented the appeal of DIN 2642 flanges. Advanced production techniques, such as CNC machining and precision forging, have resulted in components with superior surface finishes and exacting tolerances, directly contributing to smoother assembly processes and increased leak prevention.
Despite their benefits, it's crucial for stakeholders to weigh the specific requirements of each project when considering DIN 2642 flanges. Evaluating factors such as pressure classes, thermal conditions, and chemical exposures will guide the selection of the appropriate material and design. For specialized applications, consulting with material scientists or engineers with domain expertise can provide invaluable insights.
In conclusion, DIN 2642 flanges serve as a reliable and adaptable solution across a multitude of industrial applications. Their design enhances operational efficiency while ensuring safety and durability. By adhering to E-E-A-T principles, stakeholders can confidently employ these components, knowing they have selected a solution endorsed by experience, quality, and a robust foundation of industry standards.