DIN 50 flanges, a crucial component in the world of piping and mechanical installations, have seen their significance grow in various industrial applications due to their standardized design and robust construction. For those unfamiliar, the term DIN refers to the Deutsches Institut für Normung, Germany’s national organization for standardization, ensuring that these flanges adhere to stringent technical specifications and quality measures.
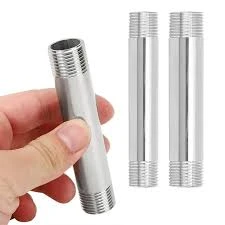
One of the most compelling aspects of DIN 50 flanges is their versatility and adaptability across different industries— ranging from petrochemicals to pharmaceuticals. Their standardized dimensions provide a seamless integration into existing piping systems, making these flanges a go-to choice for engineers and technicians aiming to maintain operational efficiency. The common use of quality materials, such as stainless steel, carbon steel, and alloyed variants, enhances their corrosion resistance and mechanical strength, ensuring longevity even under the harshest conditions.
Professionals working with DIN 50 flanges often emphasize the ease with which they can be installed and maintained. Thanks to the comprehensive dimensions provided by the DIN standards, engineers can ensure a proper fit with other piping components, reducing the risk of leaks—an essential factor for maintaining safety and reducing downtime in industrial environments. This standardization minimizes the need for custom manufacturing, which can be both time-consuming and costly, making DIN 50 flanges both a time- and cost-efficient solution.
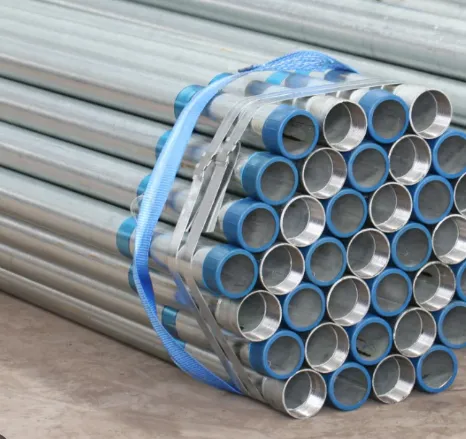
From a technical standpoint, the pressure ratings of DIN 50 flanges are crucial for determining their suitability for various applications. These pressure thresholds dictate where these components can be safely used, with high-pressure models particularly favored in high-stress environments such as chemical plants where the transfer of hazardous materials is a daily occurrence. It is essential for technical professionals to thoroughly understand these specifications to ensure both safety and compliance with industry regulations.
din 50 flange
Another factor enhancing the expertise of DIN 50 flanges is their ability to undergo rigorous testing processes. Quality assurance is paramount in the field of industrial installations, where components like flanges play a pivotal role in maintaining the structural integrity of entire systems. Reputable manufacturers of DIN 50 flanges undertake extensive testing procedures, including hydrostatic and pressure performance tests, to verify that each flange can withstand the operational demands placed upon it. These tests are a testament to their commitment to producing components that can be trusted in critical applications across various sectors.
For industry professionals seeking to deepen their understanding or enhance their inventory with high-quality components, acquiring knowledge from established experts in the field is indispensable. Attending industry conferences, engaging with professional networks, and reviewing data sheets and manufacturer guidelines can provide valuable insights into the latest advancements and best practices associated with DIN 50 flanges.
In summary, DIN 50 flanges represent a harmonization of reliability, functionality, and accessibility in flange technology. Their widespread use across diverse industries underscores their recognized authority as essential components in ensuring the smooth operation of complex fluid transport systems. Emphasizing expertise in selecting the right flange involves understanding the specific requirements of your application and consulting with experts to make informed, trustworthy decisions that align with both performance needs and regulatory standards. By doing so, organizations can ensure operational excellence, safety, and cost-effectiveness, leveraging the proven dependability of DIN 50 flanges in their infrastructure.