The 2 inch blind flange is a critical component in numerous industrial applications, renowned for its role in providing a secure seal that halts fluid flow. Most commonly used in pipeline systems, blind flanges are fundamental in ensuring operational safety and efficacy. With this distinctive capability, understanding their specifications, installation processes, and materials can vastly enhance the operational efficiency and safety compliance of industrial setups.
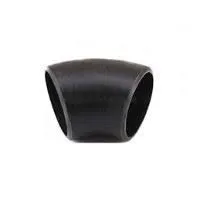
Constructed from a variety of materials, including stainless steel, carbon steel, and alloy steel, the choice of material for a 2 inch blind flange depends significantly on the operating environment. Stainless steel flanges are often selected for applications involving high temperatures or corrosive substances due to their resistance to rust and physical integrity under extreme conditions. Conversely, carbon steel is favored for its robustness in applications where the operational temperatures are not excessively high, offering a cost-effective yet durable solution.
An oft-overlooked aspect of the 2 inch blind flange is its impact on maintenance routines and shutdown procedures. Its utilization allows for easy access to pipeline systems during maintenance without the need to completely dismantle the system, saving both time and resources. This utility is particularly vital during unplanned maintenance scenarios where the swift restoration of operations is critical. The ability to provide a firm seal ensures that the rest of the pipeline system remains intact, preventing potential contamination or leaks.
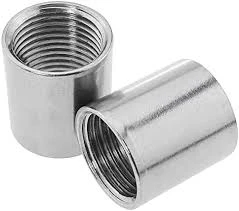
Installation of a 2 inch blind flange demands precision and understanding of its mechanics. It is typically affixed using bolts that align with the pipeline's flange pattern. Ensuring the bolts are evenly tightened is crucial to preventing pressure imbalances that may cause leaks or lead to flange failure. Utilizing a torque wrench to achieve the appropriate tension is advisable for maintaining the structural integrity of the connection. Regular checking and retorquing can avert issues associated with thermal expansion or contraction in high-temperature applications.
2 inch blind flange
Technical expertise is critical when selecting the correct specifications for a 2 inch blind flange. This includes understanding the pressure class, which signifies the maximum pressure the flange can sustain, and the face type, such as flat face or raised face, which determines the surface design where the seal occurs. In environments where the system undergoes variable pressures, opting for a flange with a higher pressure class can prevent structural failures and ensure reliability. Consultation with a flange specialist can provide insight into selecting the optimal design tailored to specific operational demands.
In terms of authority within the field, manufacturers of 2 inch blind flanges adhere to strict industry standards such as ASME B16.5,
which governs the dimensions and tolerances for pipe flanges and flanged fittings. The rigors of compliance certify that purchased flanges meet established quality and safety benchmarks, thus enhancing their reliability in critical applications. Documentation verifying compliance is often supplied by manufacturers, providing additional assurance of performance.
Trust in the application of 2 inch blind flanges can be fostered through routine plant audits and rigorous testing of flange connections. Conducting hydrostatic tests can verify the integrity of the seal, providing empirical evidence of a flange’s capability to withstand operational pressures. Furthermore, implementing a robust inspection protocol can detect early signs of wear or damage, allowing for preemptive measures to be taken before failure occurs.
In conclusion, the 2 inch blind flange serves as an indispensable element in industrial settings, thanks to its function in separating sections of pipeline systems safely and efficiently. Its role in facilitating maintenance, ensuring safety, and maintaining system integrity cannot be overstated. Through careful material selection, precision in installation, and adherence to industry standards, businesses can improve their operational reliability and prevent costly downtimes. Emphasizing expertise in product selection and maintenance ensures that potential risks are managed and trust is built within operational protocols. By strategically incorporating these practices, businesses can secure a competitive edge in their respective industries, showcasing their commitment to quality and safety.