Threaded Fittings A Comprehensive Guide
Threaded fittings are an essential part of the mechanical engineering world. They are used to connect pipes, valves, and other components in various systems, such as water, gas, and oil. In this comprehensive guide, we will explore the different types of threaded fittings, their uses, and the importance of proper selection and installation.
Introduction to Threaded Fittings
Threaded fittings are components that have threads on their ends, allowing them to be connected to other threaded components. These threads can be male (external) or female (internal). Male threads are used on the end of a pipe or other component that will be inserted into a female thread, while female threads are used on the end of a fitting that will receive a male thread.
There are several types of threaded fittings, each with its own purpose and characteristics. Some common types include
1. **Straight Threaded Fittings** These fittings have straight threads and are used for simple connections between pipes or other components.
2. **Tapered Threaded Fittings** Tapered fittings have threads that gradually decrease in diameter from the base to the tip. They are used for connecting components with different diameters or for creating a seal between the fitting and the pipe.
3. **Socket Wrench Fittings** These fittings have a socket wrench thread, which is designed to be tightened using a socket wrench. They are commonly used in industrial settings for connecting heavy-duty components.
4. **Slip-on Fittings** Slip-on fittings have threads that are designed to be slipped over the end of a pipe or other component without the need for a tool. They are commonly used in plumbing applications.
Importance of Proper Selection
The proper selection of threaded fittings is crucial for the successful operation of a system. Factors to consider when selecting threaded fittings include
1. **Thread Size** The size of the threads should match the size of the components being connected. Incorrect thread sizes can result in leaks or other problems.
2. **Thread Type** The type of threads should match the type of components being connected. For example, male threads should be used on the end of a pipe that will be inserted into a female thread, and vice versa.
3. **Material** The material of the threaded fitting should be compatible with the material of the components being connected. Incompatible materials can result in corrosion or other problems Incompatible materials can result in corrosion or other problems
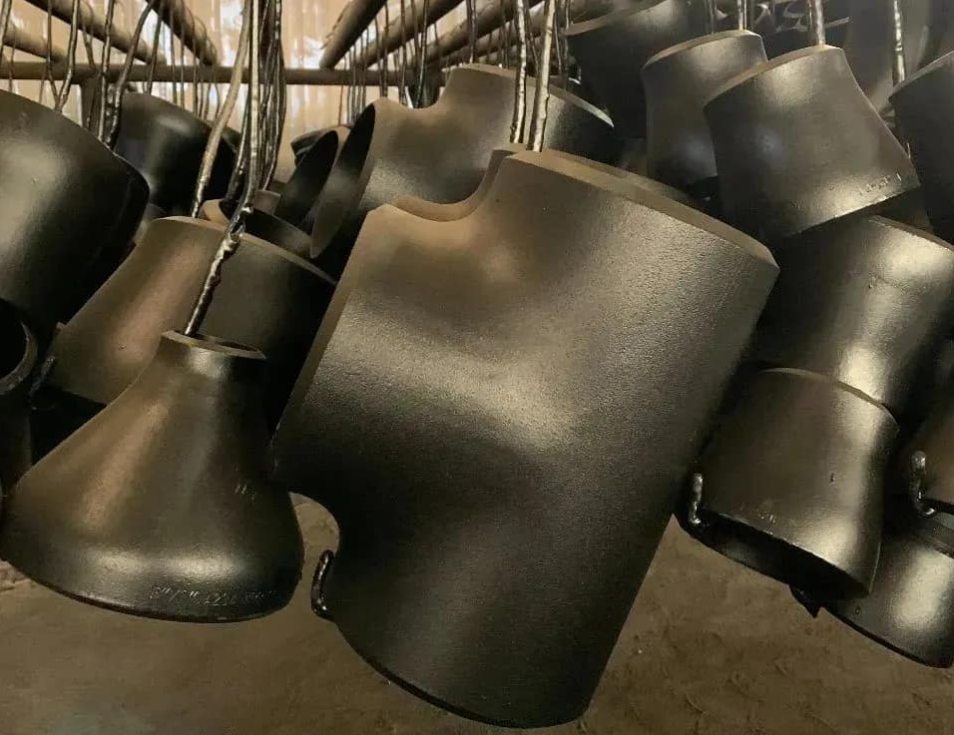
Incompatible materials can result in corrosion or other problems Incompatible materials can result in corrosion or other problems
1 2 threaded fittings.
4. **Load Rating** The load rating of the threaded fitting should be sufficient to handle the expected load. Under-rated fittings can fail under load, causing damage to the system.
Installation Techniques
Proper installation of threaded fittings is essential for their proper function and the longevity of the system. Some common installation techniques include
1. **Tightening with a Wrench** Threaded fittings can be tightened using a wrench or other suitable tool. The proper torque should be applied to ensure a good connection.
2. **Using a Pipe Wrench** Pipe wrenches are designed to tighten pipe threads and can be used to install threaded fittings.
3. **Using a Socket Wrench** Socket wrenches are designed for tightening socket wrench threads and can be used to install socket wrench fittings.
4. **Slip-on Installation** Slip-on fittings can be installed by simply sliding them over the end of a pipe or other component.
Maintenance and Inspection
Threaded fittings require regular maintenance and inspection to ensure their proper function and the longevity of the system. Some common maintenance tasks include
1. **Visual Inspection** Regular visual inspection can help identify any signs of wear, corrosion, or other problems.
2. **Thread Inspection** Threads should be inspected for signs of damage or wear. Worn or damaged threads can cause leaks or other problems.
3. **Tightening** Threaded fittings should be tightened periodically to ensure a good connection and prevent loosening over time.
4. **Replacement** Worn or damaged threaded fittings should be replaced with new ones to maintain the system's functionality and longevity.
In conclusion, threaded fittings play a crucial role in the mechanical engineering world. Proper selection, installation, and maintenance are essential for the successful operation of a system. By understanding the different types of threaded fittings and their uses, engineers and technicians can ensure the efficient and reliable operation of their systems.