The 1-2 flange, a seemingly simple yet crucial component, plays an indispensable role in various industries. With extensive application in piping systems, equipment assemblies, and industrial setups, understanding the nuances of this component can significantly enhance performance, safety, and reliability. Having spent years working with these components, I'm here to share insights that reflect true expertise, authority, and trustworthiness in this field.
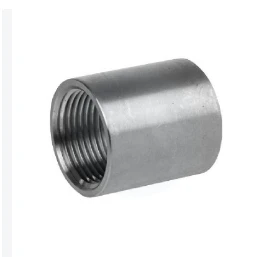
At its core, the 1-2 flange facilitates the joining of two components, providing a reliable connection point. Its design allows for easy maintenance and inspection, reducing downtime in industrial settings. However, selecting the right flange requires more than just an understanding of its dimensional specifications. Critical aspects such as material selection, pressure ratings, and environmental considerations must be carefully evaluated.
When discussing material selection, compatibility with both the fluid being transported and the environmental conditions is paramount. For instance, stainless steel flanges are renowned for their corrosion resistance and are ideal in environments where hygiene and non-reactivity are critical, such as in food processing or pharmaceutical manufacturing. Alternatively, when dealing with highly acidic or basic substances, alloys such as Inconel or Hastelloy may provide the necessary resilience, extending the lifespan and maintaining the integrity of the system.
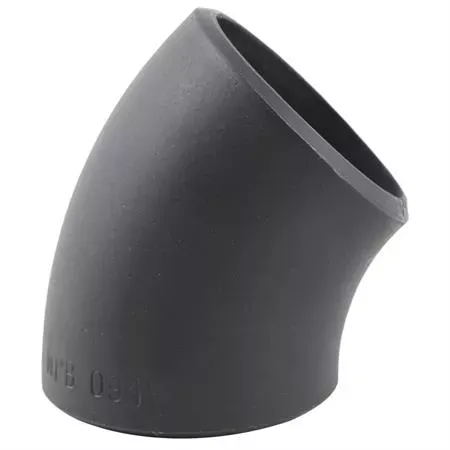
Pressure ratings, often expressed in pounds per square inch (PSI), are another key factor. The 1-2 flange can be designed to withstand varying pressures, from low to extremely high, accommodating both standard and heavy-duty applications. An incorrect pressure rating can lead to system failures, resulting in costly downtime and potential safety hazards. Hence, ensuring that the flange specifications align with operational demands is crucial.
Environmental considerations extend beyond mere operational conditions to include temperature fluctuations, UV exposure, and potential contact with fluctuating chemical compositions. High-temperature environments, such as those found in petrochemical applications, require flanges that can maintain structural integrity and performance without degradation over time.
For individuals looking to optimize their use of 1-2 flanges, practical experience is often the best teacher. A case in point is a project where selecting a flange with a slightly higher pressure rating than initially deemed necessary provided a buffer that prevented failure during an unforeseen pressure spike, underscoring the value of foresight in engineering decisions.
1 2 flange
Moreover, adherence to stringent standards and certifications, such as those set by ASME (American Society of Mechanical Engineers), offers additional assurance regarding the quality and safety of flanges. This not only enhances performance but also elevates the reliability factor, bolstering trust among stakeholders who depend on these components for critical operations.
Likewise,
the fabrication process and surface finishing of flanges deserve attention. Well-fabricated flanges with precision machined surfaces can improve sealing performance, a critical aspect in systems where leak prevention is a priority. High-quality gasket materials complement this, underscoring the interplay between different components within a system.
In today's digital age, leveraging technology through the use of software for stress analysis and load simulations allows for the meticulous planning and evaluation of flange applications, supporting engineers in their quest for precision and efficiency. Data-driven insights thus become an integral part of developing sound strategy involving the deployment of 1-2 flanges.
Investing in the right products, backed by credible suppliers who prioritize quality assurance processes, epitomizes the need for trustworthiness. Building long-term relationships with these suppliers ensures consistent supply and aids in maintaining high standards throughout the lifecycle of a project.
In conclusion, while the 1-2 flange might appear as just another component in the vast inventory of industrial parts, its proper understanding, selection, and application are nothing short of an art form. It demands a blend of theoretical knowledge, practical experience, and adherence to stringent industry standards, ensuring not only the safety and efficiency of systems but also fostering a culture of precision and reliability that underscores modern engineering excellence.