In the world of high-performance materials, 17-4 seamless tubing stands out as an exceptional choice for industries requiring robustness and precision. As a versatile alloy, 17-4 stainless steel, also known as UNS S17400, is specifically noted for its excellent strength and outstanding resistance to corrosion. This makes it an ideal candidate for applications extending from aerospace engineering to medical devices, and even oil and gas exploration.
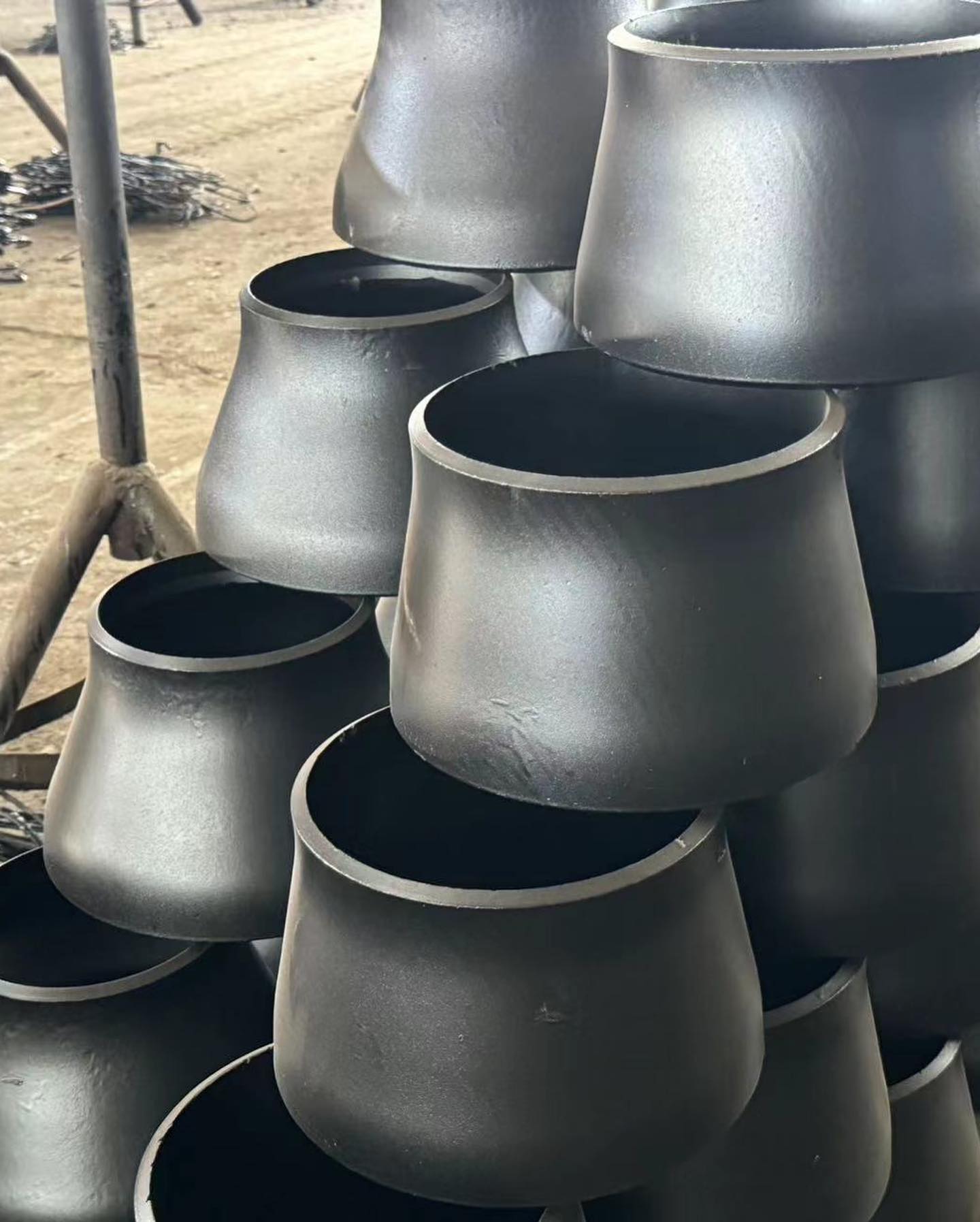
My own experience with 17-4 seamless tubing came about during a project in the aerospace sector. We were tasked with selecting a material that not only met the rigorous demands for mechanical strength and thermal stability but also adhered to stringent safety standards.
The seamless construction of 17-4 tubing was a critical factor in our decision-making process. Unlike welded tubes, seamless tubing presents minimized risk of imperfections and potential points of failure, ensuring reliability even under extreme pressure.
From a technical perspective, the remarkable properties of 17-4 stainless steel arise from its unique composition. The alloy contains a blend of iron, chromium, nickel, and copper, which are further enhanced by heat treatment processes to achieve different hardness levels. This process, known as precipitation hardening, allows manufacturers to tailor the mechanical properties of the tubing to meet specific requirements. It is this adaptability that has cemented 17-4 stainless steel as a go-to option for highly specialized industrial applications.
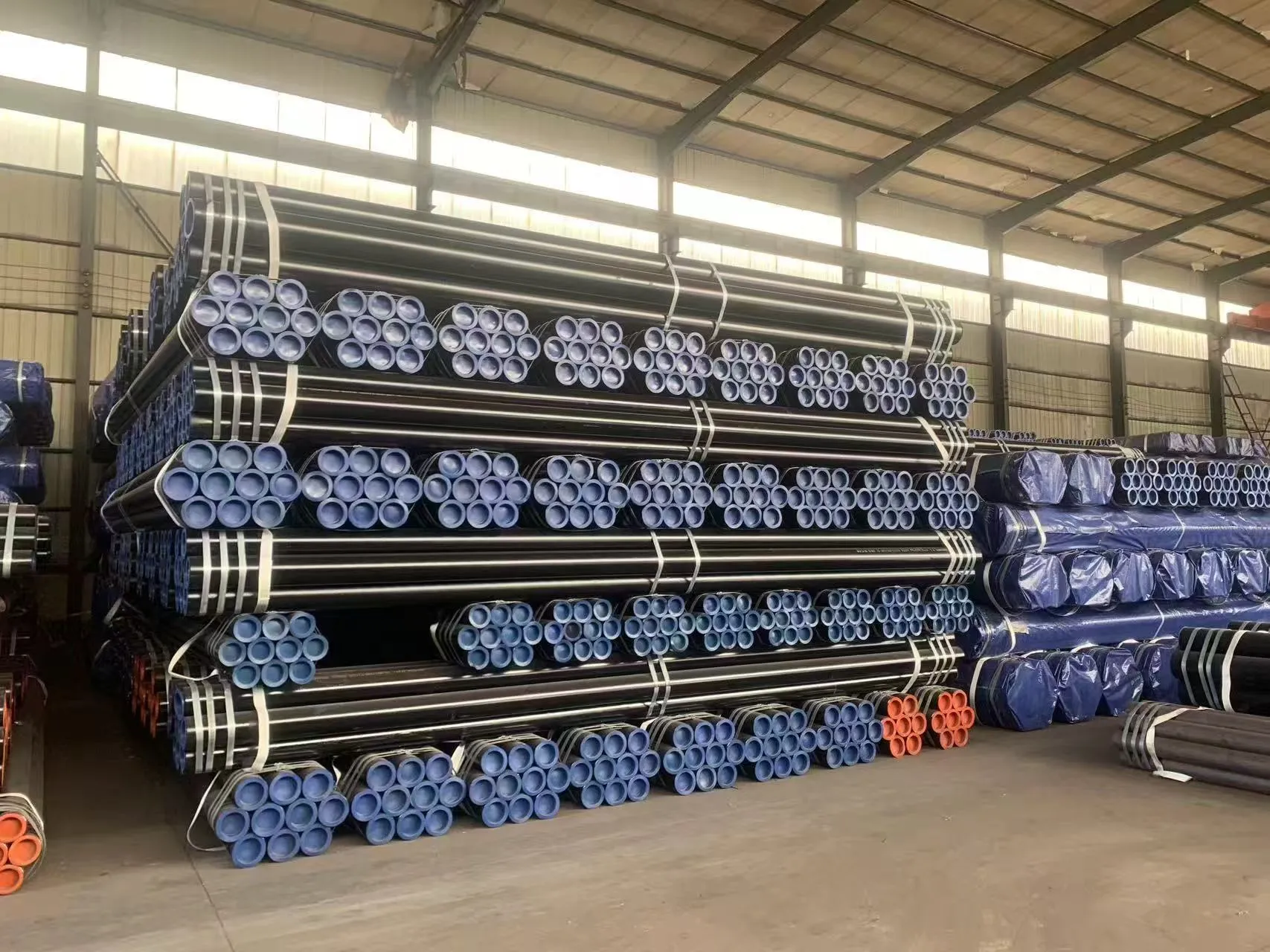
Our team collaborated closely with several experts during the selection process, seeking insight from metallurgists who emphasized the exceptional toughness of 17-4 seamless tubing. They pointed out that the alloy maintains its integrity and performance even in environments characterized by rapid temperature changes. This thermal resilience is particularly vital in spacecraft components exposed to the harsh conditions of outer space.
17 4 seamless tubing for sale
Furthermore, extensive data supports the authoritative use of 17-4 seamless tubing in medical devices. The biocompatibility of the material ensures it meets the rigorous health and safety standards demanded by the medical field. Devices such as surgical instruments and orthopedic implants often incorporate 17-4 tubing precisely because it offers reliability without compromising on hygiene due to its corrosion-resistant nature.
Trust in 17-4 seamless tubing is built not only on its inherent material properties but also on the reputation of manufacturers who provide rigorous testing and certification. Partnering with reputable suppliers who adhere to industry standards such as ASTM A564 ensures that the tubing delivered is of the highest quality. These certifications are a testament to the commitment manufacturers make to reliability, which in turn fosters trust among engineers and designers relying on these materials for critical applications.
Moreover, the seamless aspect of the tubing is crucial where joint integrity is of paramount importance. The absence of welds reduces the risks associated with corrosive attack and localized stress concentrations that can lead to premature failure. This quality is invaluable in sectors such as oil and gas, where the operational conditions are harsh, and failure is not an option.
In conclusion, the characteristics of 17-4 seamless tubing position it as a premier choice for industries that can afford no compromises when it comes to material performance. The combination of strength, corrosion resistance, and adaptability through heat treatment makes it a versatile asset in a wide range of applications. As the demand for high-performing materials continues to rise, the authoritative role of 17-4 seamless tubing is solidified by both practical experience and technical validation, making it a trusted component in the toolkit of engineers across the globe.