Pipe flanges are an essential component in various industries, including oil and gas, petrochemicals, water supply systems, and many more. Their primary function is to connect pipes, valves, pumps, and other equipment to form a piping system. Selecting the right flange is crucial for ensuring the system's efficiency, safety, and longevity.
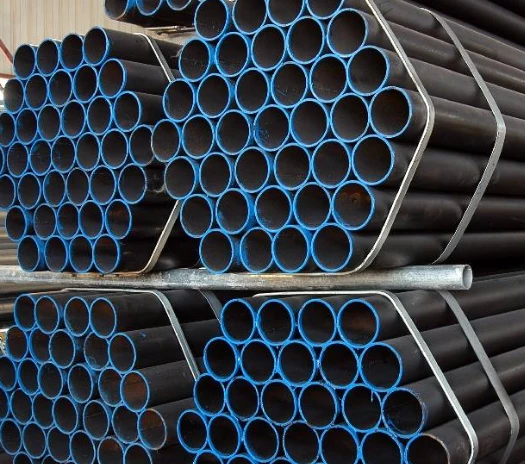
One of the most practical experiences with pipe flanges involves their reliability in high-pressure environments. For instance, in a large-scale petrochemical plant, pipe flanges need to withstand extreme pressures and temperatures. A flange failure could lead to catastrophic consequences, underscoring the importance of quality and precision in their manufacturing. Experience with leading brands that adhere to international standards like ASME, ANSI, or DIN is invaluable. Manufacturers that go through rigorous testing and quality checks provide products that professionals in the field have trusted for decades.
From an expertise standpoint, understanding the different types of pipe flanges enhances selection accuracy. For those unfamiliar, the landscape of pipe flanges includes welding neck, slip-on, socket weld, lap joint, threaded, and blind flanges, each serving specific functions. For example, a welding neck flange is ideal for high-pressure applications due to its capacity to maintain alignment under various loads. These nuances demonstrate why professionals should continually expand their expertise in identifying the ideal flange type for each scenario.
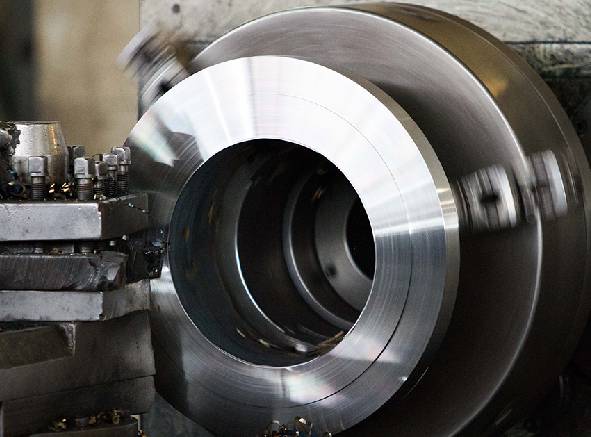
Authoritativeness in the field of pipe flanges can often be measured by a company's history and the certifications of its products. An authoritative flange manufacturer will offer detailed documentation and certification for each piece, often supported by case studies or testimonials from significant industry players. This transparency not only establishes authority but also provides assurance to customers about the product's capabilities and compliance with industry standards.
1 pipe flange
Trustworthiness in pipe flange selection often hinges on the materials used and the compatibility with the intended application. Innovation in material science has led to the development of flanges made from stainless steel, carbon steel, alloy, and various composites, each offering distinct benefits. For instance, industries dealing with corrosive substances might opt for stainless steel due to its superior corrosion resistance. Trustworthy manufacturers openly share information regarding material grades and their suitability for different environments, providing peace of mind that the chosen flange will perform as expected under specific conditions.
In addition to material and type, dimensions and pressure ratings are crucial factors in flange selection. Flanges are manufactured to fit pipes of various sizes, and each comes with a pressure rating, denoting the maximum pressure it can handle. Selecting a flange that matches the system's pressure requirements prevents leaks and system failures. This aspect emphasizes why expert consultation is beneficial; seasoned professionals can provide insights into choosing not only the most suitable flange but also ensuring it enhances the system’s overall integrity.
Finally, recent advancements have led to the introduction of custom-designed flanges to accommodate unique applications. These bespoke solutions demonstrate a blend of engineering prowess and innovative material use, reflecting the evolution of the industry to meet specific client needs more efficiently. Customization comes with its own set of challenges and benefits, but it allows systems to operate more cohesively, often leading to cost savings in the long run due to increased efficiency and reduced maintenance.
In summary, the selection of a pipe flange is not merely about connecting components but about ensuring the continuous and safe operation of critical systems. The right balance of experience, expertise, authority, and trust is crucial. For engineers and purchasing managers, understanding these facets can lead to informed decisions that optimize performance and uphold safety standards in demanding industrial environments.