The mastery of 2G pipe welding is critical for industries demanding high-quality pipe joints, such as oil and gas, chemical manufacturing, and shipbuilding. This process involves welding pipes in the horizontal position, creating a strong circumferential joint. Unlike other welding positions, 2G allows for a more uniform application of filler material, resulting in durable seams that are crucial in industries where leaks or joint failures are not an option. Using cutting-edge techniques and equipment can greatly improve the quality of a 2G weld, and understanding the intricacies of this process is essential for success.
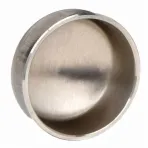
To achieve the perfect 2G weld, it's important to start with the right equipment and materials. High-quality welding machines that offer precise control over amperage and voltage are essential. These machines ensure that the weld pool is adequately managed, preventing potential defects such as porosity or slag inclusion. When selecting filler materials, compatibility with the base metal is paramount, as mismatches can cause weak joints that compromise pipeline integrity. Metals like carbon steel, stainless steel, and various alloys demand specific fillers to ensure joint strength and longevity.
The technique used by the welder plays an equally crucial role in the welding process. A steady hand, good eye coordination, and an in-depth understanding of how heat affects different metal types are critical skills. Welders must carefully maintain the torch angle and travel speed to ensure a consistent weld bead. Any fluctuations can lead to imperfections that, in some industries, can result in catastrophic failures. For example, in the oil and gas sector, a flawed weld can lead to costly and dangerous leaks, emphasizing the importance of masterful technique.
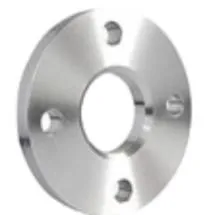
Real-world applications often dictate variations on standard 2G practices. For instance, in environments with restricted access or challenging positions, welders might adopt specialized techniques to handle the operational constraints. Moreover, certain industries impose rigorous inspection standards using non-destructive testing (NDT) methods like X-ray or ultrasonic testing, which demand that each weld meets the highest quality benchmarks to pass these stringent evaluations.
2g pipe weld
Experienced welders also understand the importance of pre-weld and post-weld care. Cleaning the pipe surfaces before welding removes impurities that can cause defects, and post-weld heat treatment is often necessary to relieve stress in the joint, minimizing the potential for cracking or warping over time. Adequate preparation and follow-up ensure that even once the most skilled weld is made, its integrity is preserved through the pipeline's operational life.
The authority of 2G pipe welding also expands into the realm of automation. As industries modernize, the integration of robotic welding arms becomes more common. These machines provide unmatched precision and repeatability, ideal for projects demanding high output with minimal errors. Nevertheless, even with automation, expert oversight ensures that robotic systems are properly calibrated, and any anomalies are quickly addressed. Automation complements skilled workmanship, allowing companies to scale operations without sacrificing quality.
Trust in the 2G pipe welding process is often established through certifications and training programs. Certified welders bring a reassuring level of expertise, having demonstrated their abilities to produce high-quality welds under various conditions. This formal recognition serves as a testament to their skills and a promise of reliability to employers and clients alike. Encouraging ongoing education and certification helps keep welders abreast of new techniques and technologies, ensuring the workforce remains competent and competitive.
The world of 2G pipe welding is continuously evolving with advancements in technology and materials, yet the cornerstone remains the expertise of the welder. Mastering the skill involves not merely the ability to produce a strong weld but also a commitment to ongoing learning and adherence to industry standards. By integrating traditional craftsmanship with modern technology and maintaining rigorous inspection protocols, industries can achieve the highest levels of product quality and safety. As industries push boundaries in conjunction with demanding environments, the importance of experienced and authoritative 2G welders remains at the forefront of operational success.