Die Casting A Comprehensive Guide
Die casting is a manufacturing process that involves pouring molten metal into a steel mold cavity to create a desired shape. This versatile technique has been used for centuries, with its origins dating back to the ancient Egyptians who used it to cast gold and silver jewelry. Today, die casting is widely used in various industries, including automotive, aerospace, electronics, and consumer goods.
The die casting process begins with the creation of two or more steel molds, known as dies. These dies are carefully designed and machined to create the exact shape and size of the part to be produced. The dies are then assembled and clamped together, creating a sealed cavity where the molten metal will be poured.
Once the dies are ready, the molten metal is heated to a high temperature and then poured into the mold cavity through a sprue and runner system. As the metal cools and solidifies, it takes the shape of the mold cavity, creating a finished part. The excess metal is then drained from the mold through channels called risers, which provide a source of metal for filling any voids that may form during the cooling process.
One of the key advantages of die casting is its ability to produce parts with complex shapes and tight tolerances. The high pressure used during the pouring process ensures that the metal flows evenly into all areas of the mold, resulting in parts with smooth surfaces and accurate dimensions. Additionally, die casting can produce parts at a faster rate than other manufacturing processes, making it an attractive option for high-volume production runs Additionally, die casting can produce parts at a faster rate than other manufacturing processes, making it an attractive option for high-volume production runs
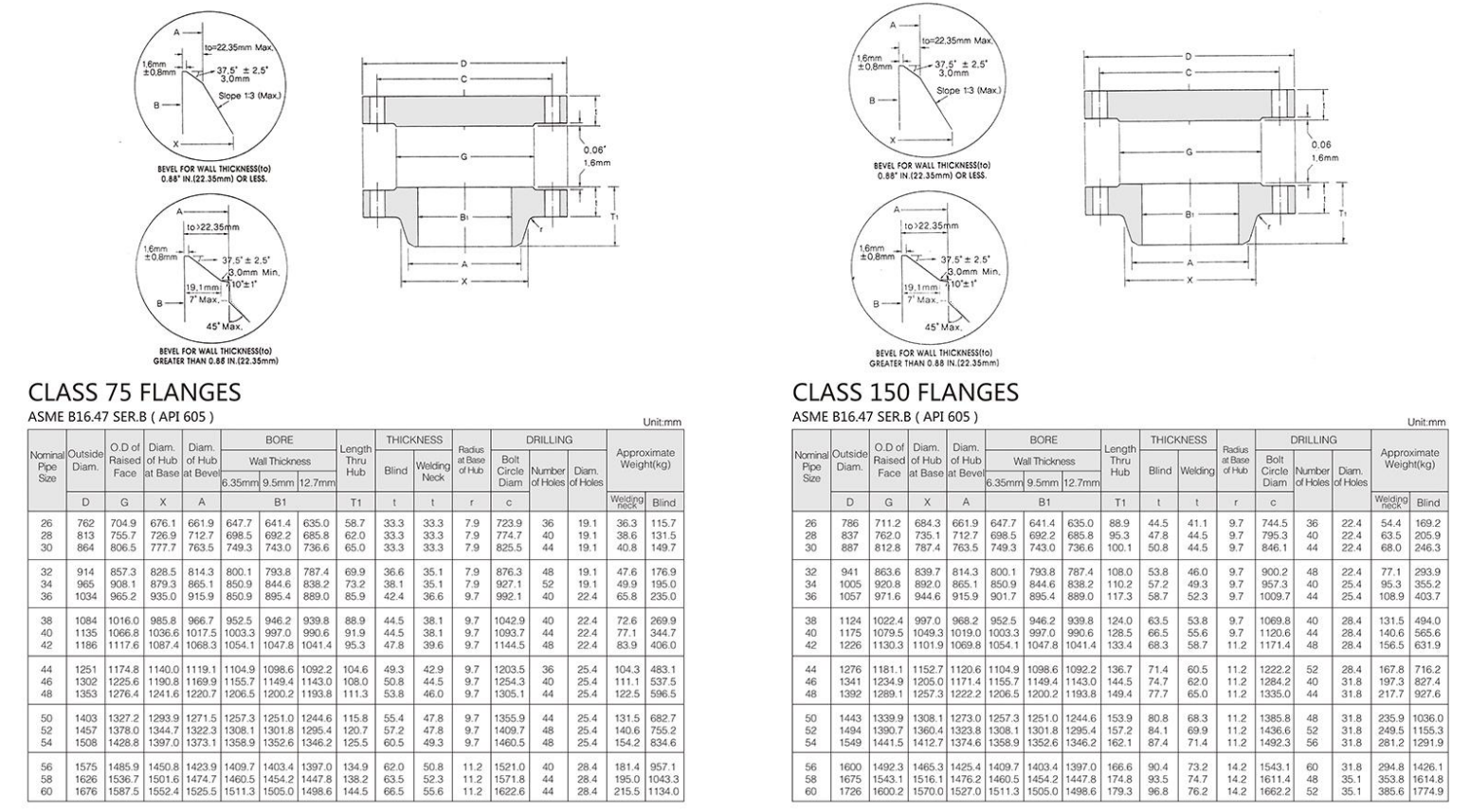
Additionally, die casting can produce parts at a faster rate than other manufacturing processes, making it an attractive option for high-volume production runs Additionally, die casting can produce parts at a faster rate than other manufacturing processes, making it an attractive option for high-volume production runs
die casting.
However, die casting also has some limitations. One of the main challenges is dealing with the high temperatures involved in the process, which can cause thermal stresses and warping in the molds. To mitigate these issues, die casters often use advanced materials and cooling techniques to maintain the stability of the molds throughout the production process.
Another challenge is the cost associated with die casting. The initial investment in tooling and equipment can be significant, and the process itself can be energy-intensive. However, when compared to other manufacturing methods, die casting can offer a lower overall cost per part for high-volume productions.
In conclusion, die casting is a versatile and efficient manufacturing process that has been used for centuries to produce a wide range of products. Its ability to produce parts with complex shapes and tight tolerances, combined with its fast production rates, makes it an attractive option for many industries. While there are some challenges associated with die casting, such as thermal stresses and high costs, these can be mitigated through proper design and process optimization.