Flanges play a pivotal role in the construction and machinery sectors, offering essential connections for pipelines, pumps, and other infrastructural components. Among the myriad of flange types, the 3 8 flange stands out as a versatile and highly valuable option for professionals across various industries. When considering the adoption or specification of a 3 8 flange, it's crucial to understand its application, benefits, and selection criteria to ensure optimal performance and longevity.
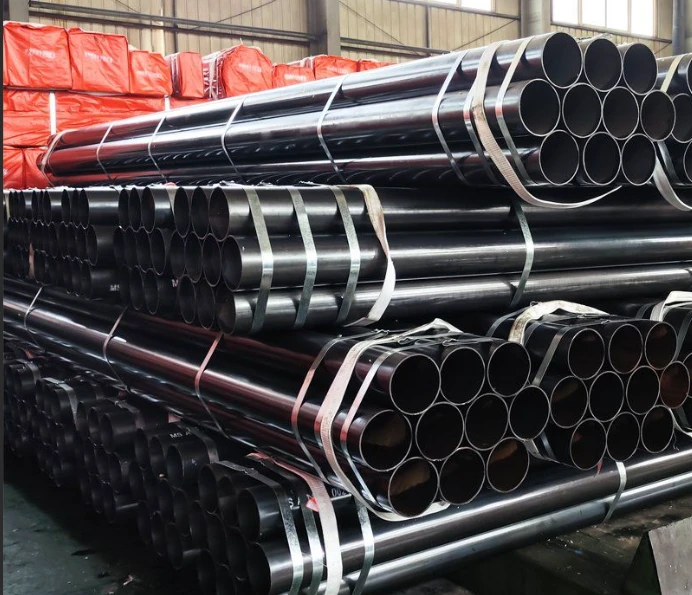
At the core of its functionality, a 3 8 flange provides a robust connection point with an internal bore size that allows for easier installation and alignment of connecting pipes or equipment. This specific flange is designed for systems requiring exceptionally precise engineering, often utilized in oil and gas, chemical production, and marine industries. Its unique design contributes to maintaining high-pressure integrity and leak prevention, which is paramount for industries dealing with volatile or hazardous materials.
The material composition of a 3 8 flange significantly impacts its application suitability. Typically constructed from stainless steel, carbon steel, or alloys like Inconel, the choice of material directly influences the flange's resistance to corrosion, temperature durability, and structural integrity. For instance, stainless steel flanges are preferred for environments exposed to moisture and corrosive substances due to their rust-resistant properties, ensuring extended lifespan and reduced maintenance costs. On the other hand, carbon steel flanges are favored in scenarios where strength and cost-efficiency are prioritized over corrosion resistance.
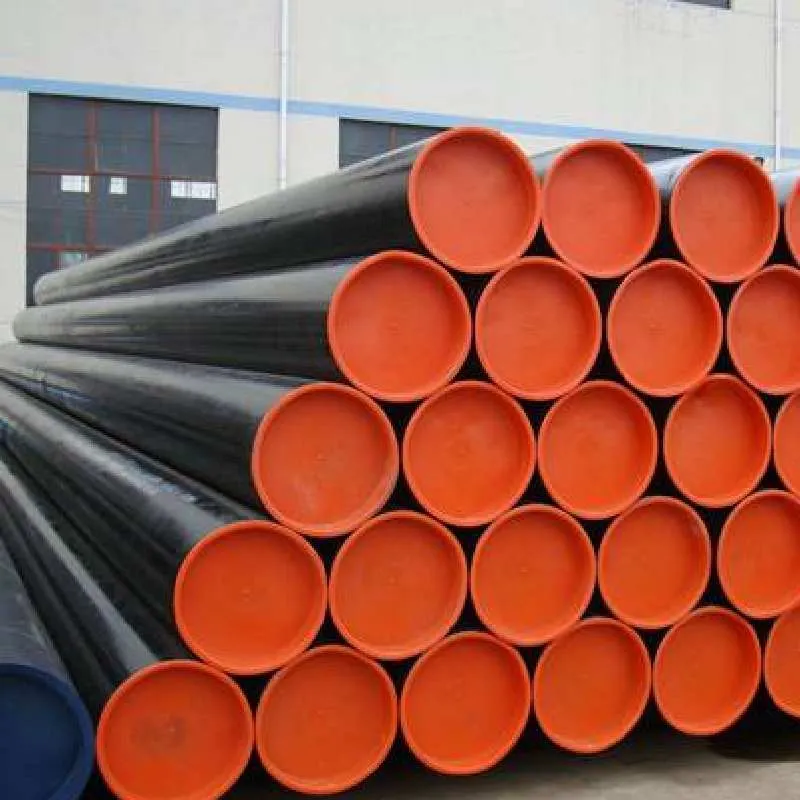
To select the right 3 8 flange, several factors must be meticulously evaluated. The pressure rating (indicated by its class or schedule) is paramount, as it determines the maximum pressure the flange can safely withstand. Furthermore, the temperature rating must align with the operating conditions of the system to avoid potential failures. Compatibility is another critical consideration; the flange must perfectly align with the size, material, and design specifications of the pipe or equipment it joins to prevent leaks or structural discrepancies.
Beyond material and compatibility, adherence to industry standards is necessary for ensuring the flange's reliability and safety.
Standards such as the ASME B16.5, EN 1092-1, and DIN 2633 provide comprehensive guidelines on dimensions, materials, and testing procedures, ensuring flanges meet global benchmarks for quality and performance. Utilizing flanges compliant with such standards not only boosts system efficiency and safety but also facilitates international operations, where adherence to universally recognized specifications might be legally mandated.
3 8 flange
The installation process is another vital aspect of leveraging the benefits of a 3 8 flange. Proper alignment is crucial, as misalignment can lead to gasket failures and connection breakdowns. Using appropriate gaskets and ensuring even torque distribution across flange bolts enhance the connection's stability and durability. Routine inspections and maintenance, such as checking for signs of wear, corrosion, or deformation, allow for early detection of potential issues, thereby preventing system downtimes and extending the operational life of the flange.
Furthermore, the adaptability of the 3 8 flange design enhances its usability across diverse projects. Customization options, such as surface treatments, hole patterns, and sealing methods, allow engineers to tailor the flange to specific application requirements, ensuring optimal performance and efficiency.
The environmental and economic implications of choosing the right 3 8 flange cannot be overstated. Selecting a high-quality, appropriately rated flange minimizes leaks and emissions, contributing to environmental protection and sustainability. From an economic perspective, investing in durable and reliable flanges reduces long-term repair and replacement costs, providing a favorable return on investment.
In conclusion, the 3 8 flange is a cornerstone component in many industrial applications, offering unparalleled reliability and functionality when selected and applied correctly. By understanding the specific needs of the system, adhering to industry standards, and following best practices in installation and maintenance, businesses can harness the full potential of this essential piece of engineering equipment. With careful consideration and strategic implementation, the 3 8 flange not only ensures operational success but also upholds safety, efficiency, and environmental responsibility in every application.