In the world of industrial fabrication and piping systems, 7018 pipe welding has built a reputation as the go-to method due to its reliability and efficiency. Rooted in decades of professional use, 7018 electrodes are prized for their low hydrogen deposit and excellent mechanical properties, offering superior weld quality in diverse conditions.
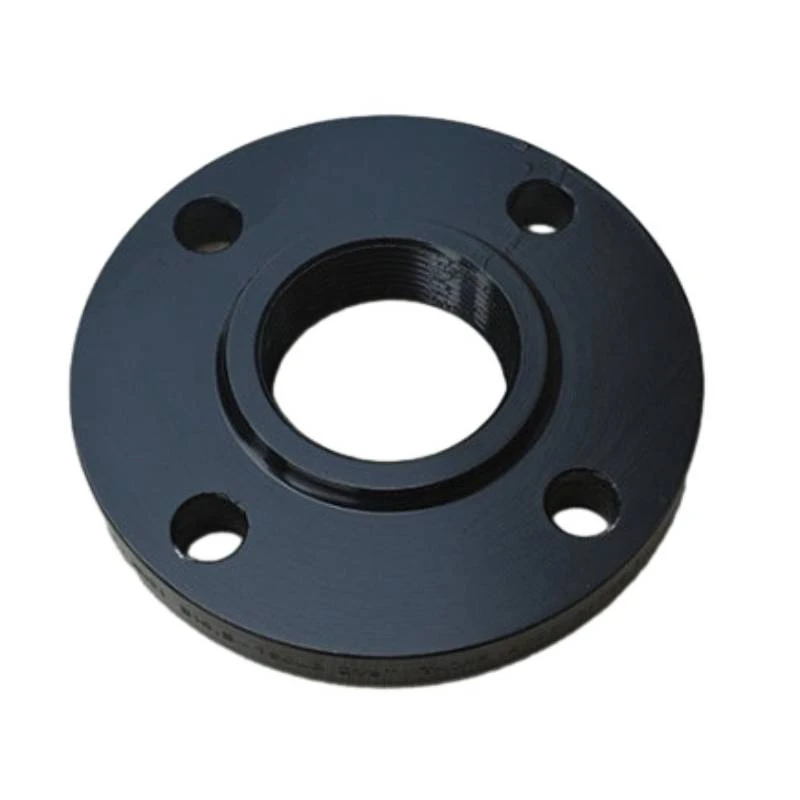
The 7018 electrode is specifically designed for creating welds that withstand significant stress and pressure, a necessity in industries such as oil and gas, shipbuilding, and structural steel applications. This makes the process a staple for projects that demand unequivocal strength and security. The industry regard for 7018 electrodes hinges on their detailed composition and intrinsic welding characteristics which ensure the integrity of larger metal structures where safety is paramount.
To appreciate its place in the industry, one must understand the composition of the 7018 electrode. It is a low hydrogen, potassium-based iron powder electrode, known for its arc stability, smooth weld bead appearance, and robust slag system. It’s a formula crafted for both AC and DC welding circuits. The low hydrogen emission is crucial as it reduces the risk of hydrogen-induced cracking, a common problem in high-strength materials.
This makes 7018 electrodes particularly valuable when welding low alloy steels.
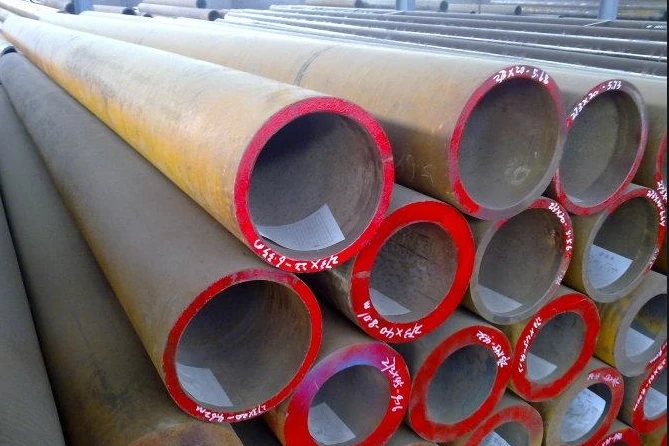
The welding process itself demands a certain level of expertise and experience to optimize the electrode's potential. A significant focus is placed on storage and handling of 7018 electrodes. Because of their low hydrogen properties, they are susceptible to moisture pick-up, necessitating storage in temperature-controlled environments or ovens to maintain their dryness. This aspect speaks directly to the professionalism required to handle and implement these electrodes effectively. Welders often dedicate time to preparing the workspace and materials, ensuring everything is in prime condition before any welding begins.
Another critical consideration when working with 7018 electrodes is the positional versatility they offer. Capable of performing in all positions—flat, horizontal, vertical, and overhead—these electrodes are highly adaptable, offering flexibility and reducing the need for repositioning workpieces during welding. The versatility speaks to the expertise required to operate under varying conditions, reiterating the importance of seasoned skills and practiced techniques.
7018 pipe welding
The expertise in 7018 pipe welding extends to mastering correct amperage settings, travel speeds, and maintaining consistent electrode angles—each step influencing the final weld quality. the nuanced control over these parameters ensures a strong, defect-free weld. Experienced welders know the importance of technique, with many tradesmen acquiring this elusive touch through years of practice and extensive training. This level of mastery contributes to its authority in the industry.
Moreover, instructors and seasoned professionals play a vital role in sharing knowledge within the welding community, reinforcing trustworthiness, and promoting safe practices across various industries. Regular updates and safety protocols are disseminated through workshops, conferences, and industry publications, aiding in the professional development of welders across the board.
7018 pipe welding’s authoritative standing in industrial sectors is cemented by its extensive utility and performance track record. It serves as a testament to human ingenuity in creating solutions capable of evolving with the ever-demanding requirements of modern construction and manufacturing. Thus, 7018 welding not only represents a technique but embodies an entire ecosystem of expertise, reliability, and technological advancement.
Lastly, the sustainability factor can be highlighted, as advances in electrode coatings and welding technologies are driving improvements in efficiency and reduction of waste, aligning with global shifts towards environmentally friendly industrial practices. This continued evolution ensures that 7018 welding will remain a cornerstone technique well into the future.
By fortifying infrastructure, advancing construction methodologies, and maintaining rigorous standards, 7018 pipe welding remains an invaluable skill and process recognized across numerous engineering and construction disciplines for its consistency, durability, and authoritative presence.