The Precision and Perseverance of Pressure Pipe Welding
Pressure pipe welding is an essential process in the construction and maintenance of critical infrastructure, such as water supply networks, oil and gas pipelines, and nuclear power plants. It involves the joining of pipes under high pressure conditions to ensure structural integrity and leak-proof seals. This specialized form of welding demands a unique blend of technical expertise, precision, and safety consciousness.
Welding pressure pipes is not a task for the uninitiated. It requires a deep understanding of material properties, welding techniques, and the ability to work under stringent safety protocols. The pipes, often made from materials like carbon steel, stainless steel, or alloy steel, must withstand extreme pressures and temperatures without failure. Therefore, the welds must be flawless, capable of withstanding immense stress and resistant to corrosion.
The process typically begins with thorough preparation. The pipe ends are cleaned and beveled to create a suitable joint profile. This step is crucial as any contamination can compromise the quality of the weld. Then, the welding procedure specification (WPS) is followed strictly, which outlines the exact parameters for the welding process, including the type of electrode, current, and travel speed.
The actual welding is a delicate dance between skill and science. It often involves the use of automated or semi-automated systems for increased precision and consistency It often involves the use of automated or semi-automated systems for increased precision and consistency
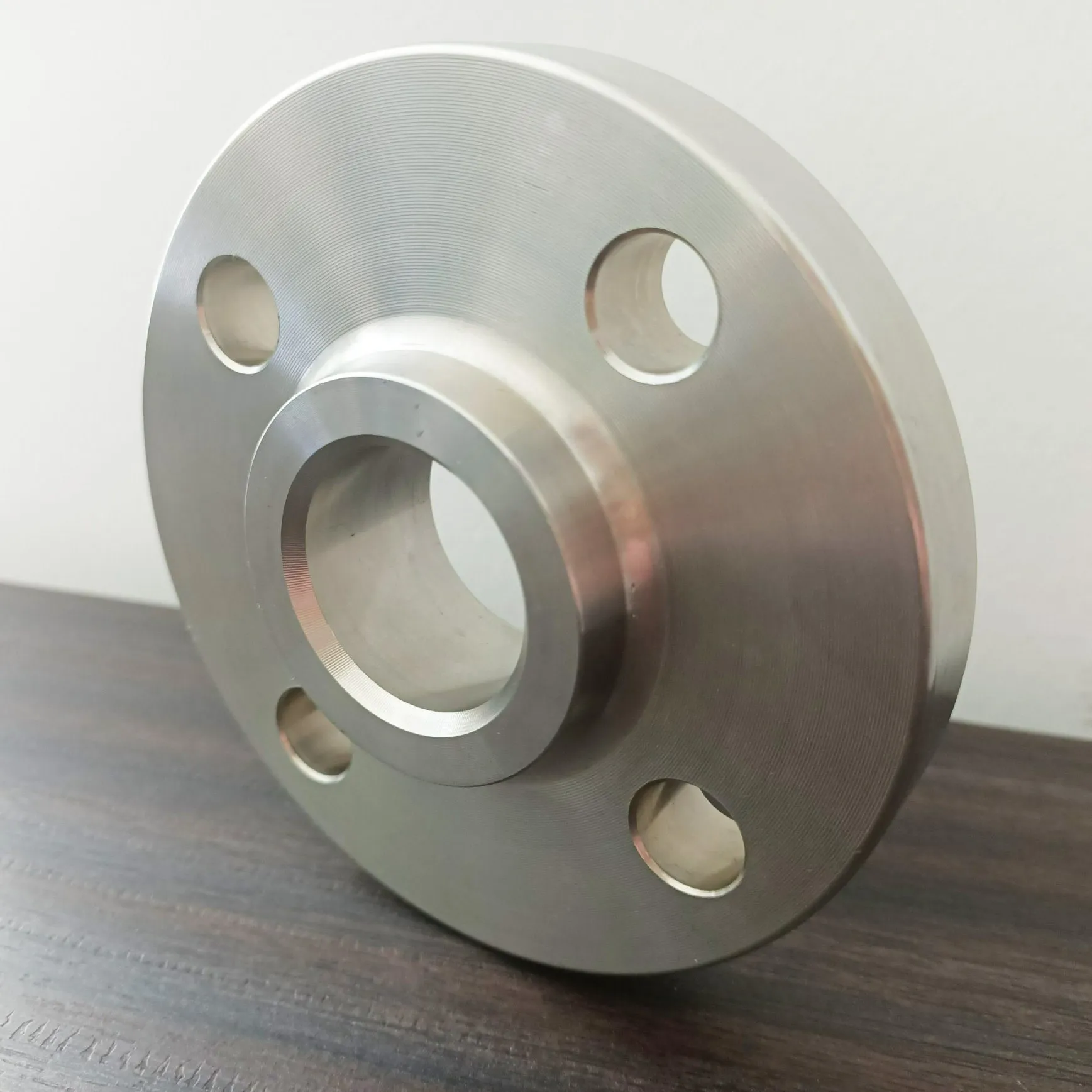
It often involves the use of automated or semi-automated systems for increased precision and consistency It often involves the use of automated or semi-automated systems for increased precision and consistency
pressure pipe welding. Techniques like Gas Tungsten Arc Welding (GTAW) or Gas Metal Arc Welding (GMAW) are commonly employed, depending on the pipe size, material, and pressure requirements.
Post-weld inspection is as critical as the welding itself. Non-destructive testing methods like X-ray, ultrasonic, or magnetic particle inspections are used to detect any defects that might compromise the pipe's structural integrity. These tests ensure that the weld meets industry standards and is safe for operation.
Pressure pipe welding is not just about connecting two pieces of metal; it is about building lifelines that transport essential resources and energy across vast distances. It is a testament to human ingenuity and our ability to engineer solutions to complex challenges. However, it also underscores the importance of safety and responsibility in the face of high stakes.
In conclusion, pressure pipe welding is a highly specialized field that demands a unique blend of technical prowess, meticulous attention to detail, and unwavering commitment to safety. It is a discipline where the smallest error could have significant consequences, making skilled welders the unsung heroes of our infrastructural backbone. Their work, often unseen, ensures that the pipes we rely on remain strong, secure, and reliable under immense pressure.