Different types of pipe flanges play a crucial role in a wide variety of industries, ensuring sealed and efficient connections within plumbing, automotive, aerospace, and manufacturing sectors. Understanding their specific functions, materials, and applications can pave the way for ensuring long-term efficiency and safety in any piping system.
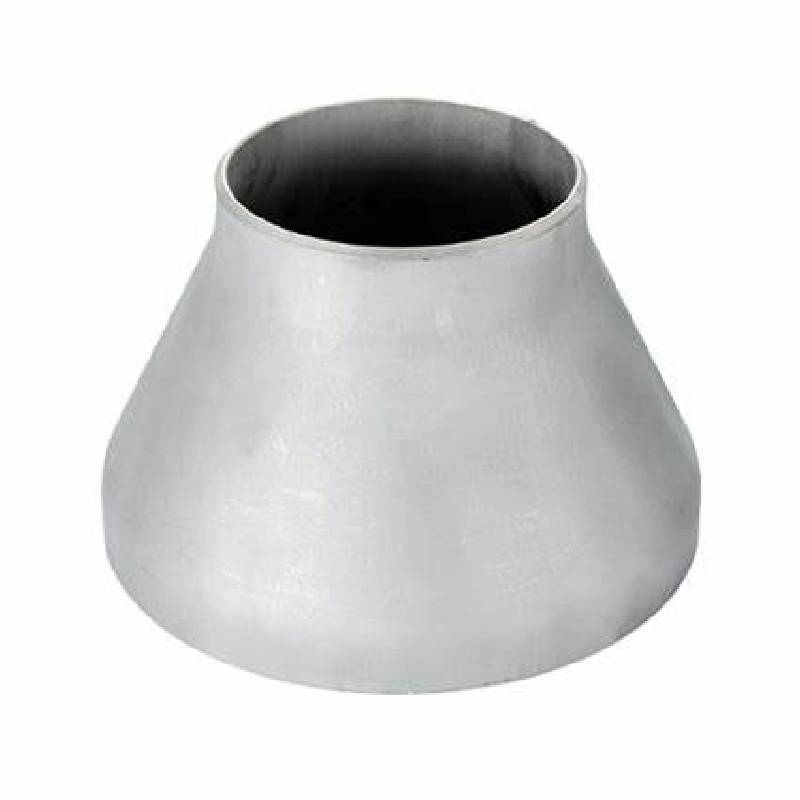
Pipe flanges are essential connectors that facilitate the assembly, disassembly, and maintenance of piping systems. These components provide easy access for cleaning, inspection, and modification of pipelines. The versatility of flanges—coming in various shapes, sizes, and materials—makes them suitable for diverse applications and environmental conditions.
The most common types of pipe flanges include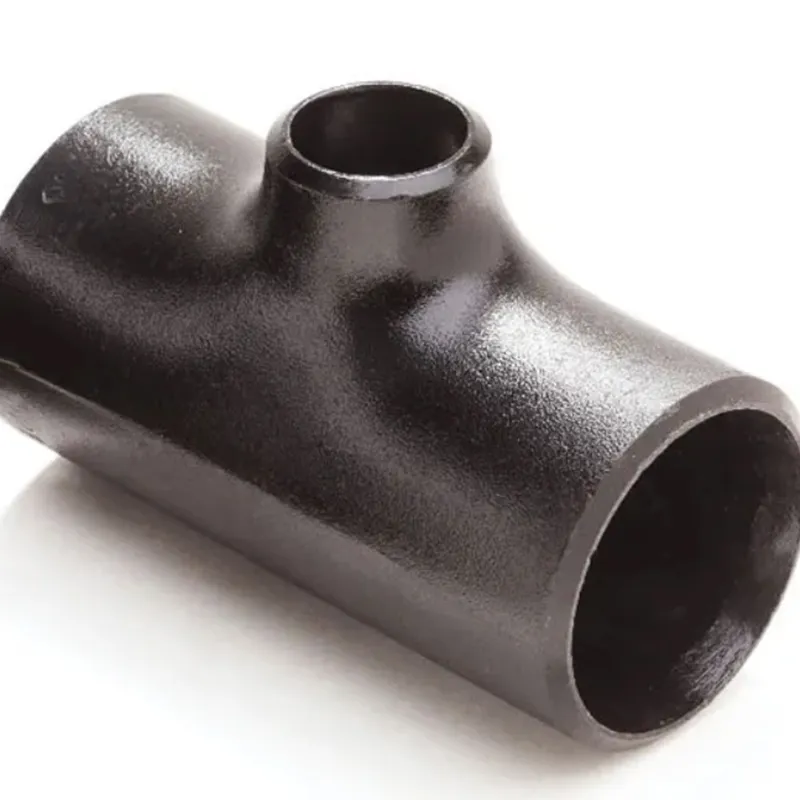
1. Weld Neck Flanges
Renowned for their ability to withstand extreme pressure and temperature, weld neck flanges are integral in systems where reliability is critical. Their protruding neck offers gradual transitions for stress distribution, minimizing the risk of structural failure. Used predominantly in high-pressure environments, their durability ensures longevity in demanding applications such as oil and gas refineries.
2. Slip-On Flanges
These are perfect for low-pressure applications where easy installation is a priority. As their name suggests, slip-on flanges slide over the pipe and are then welded in place. Although less robust than weld neck flanges, their cost-effectiveness and ease of assembly make them ideal for non-critical systems that do not encounter severe stresses.
3. Blind Flanges
Essential for sealing off pipe ends, blind flanges allow for easy access when inspecting or modifying a network. These flanges are frequently employed in systems that require periodic maintenance or expansions because they enable accessibility without the need to dismantle large sections of piping.
4. Socket Weld Flanges
Designed for small diameter, high-pressure applications, socket weld flanges provide excellent leakage prevention. The pipe is inserted into the flange, and a fillet weld is then applied, making this design an excellent choice in systems where leaking is an unacceptable risk, such as chemical processing plants.
different types of pipe flanges
5. Lap Joint Flanges
Featuring a two-part construction, lap joint flanges include a stub end which supports the flange over the pipe. This design allows for easy rotation and alignment, accommodating misalignments in systems where revising positioning is necessary. Their ease of replacement and alignment makes them suitable for systems requiring consistent inspection and alteration.
6. Threaded Flanges
These flanges are exceptionally convenient for assembly and disassembly without welding, making them a favorite in environments where heat application is undesirable. Common in low-pressure, non-volatile environments, their threaded design is adept for scenarios involving smaller diameters.
Selecting the right type of flange requires an understanding of the material it’s manufactured from and the intended application environment. Common materials include stainless steel, carbon steel, and alloy steel, each offering different benefits. For instance, stainless steel provides excellent corrosion resistance required in marine or chemical processes, while carbon steel offers robustness at a lower cost, suitable for high-temperature systems.
Moreover, the selection process must consider factors such as pressure ratings and temperature limitations denoted by classes (150, 300, etc.), as these specifications impact a flange's performance and compatibility with existing systems.
Professional expertise is indispensable when configuring a piping system. Engaging with experienced engineers and using high-quality, certified products ensures adherence to safety standards and optimal performance. Trust in authoritative sources and manufacturers can mitigate risks associated with poor quality products while maximizing operational efficiency.
Additional considerations such as gasket and bolt selection play a pivotal role in the functionality of pipe flanges. Ensuring compatibility with flange materials can prevent leakage and maintain the integrity of the junction under operational stresses.
In conclusion, the selection and application of different types of pipe flanges call for a balance of technical knowledge, material science, and judicious decision-making—especially in industries where reliability translates directly into safety and productivity. Comprehensive expertise paired with quality components fosters effective, durable, and efficient piping systems across all sectors.