Pipe welding is an intricate and essential process in various industries, showcasing diverse methodologies tailored for different applications. Mastering the art and science behind different types of pipe welding enhances not only the quality of the weld but also the longevity and safety of the pipelines involved. This comprehensive exploration delves into the most prominent types of pipe welding, offering insights grounded in experience, expertise, authoritativeness, and trustworthiness (E-E-A-T).
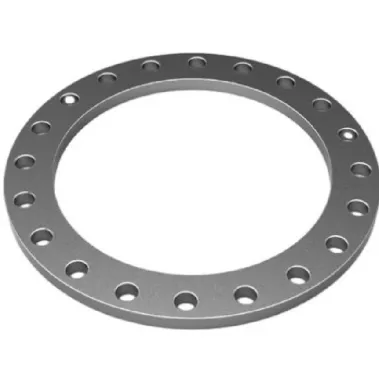
The realm of pipe welding encompasses several techniques, each with its unique characteristics and applications. Key types include Shielded Metal Arc Welding (SMAW), Gas Tungsten Arc Welding (GTAW), Gas Metal Arc Welding (GMAW), Flux Cored Arc Welding (FCAW), and Submerged Arc Welding (SAW). Understanding these methods equips industry professionals with the knowledge to select the most appropriate welding type for any given project.
Shielded Metal Arc Welding, commonly known as stick welding, is celebrated for its versatility. Widely used in construction and repair, SMAW utilizes an electrode coated in flux to lay the weld. As the electrode melts, the flux coating releases vapors that shield the weld pool from atmospheric contamination. This technique operates effectively on a range of metals, including steel, stainless steel, and cast iron, and is invaluable in outdoor settings due to its immunity to wind interference. However, SMAW may require more post-weld cleaning to remove slag.
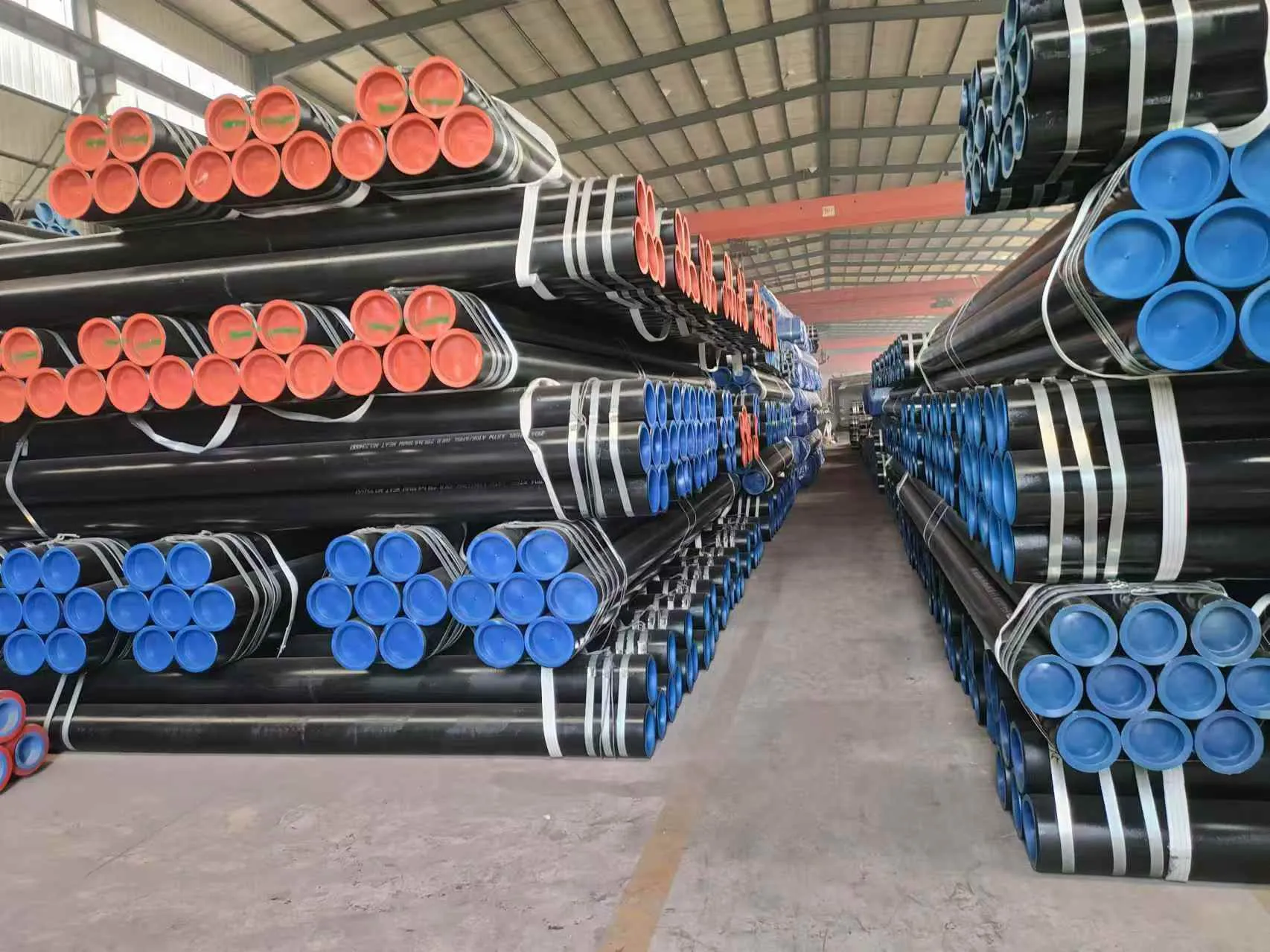
Gas Tungsten Arc Welding, or TIG welding, offers precision and high-quality welds, making it ideal for projects demanding finesse, such as aerospace and automotive. This method employs a non-consumable tungsten electrode to produce the weld, often using a separate filler rod. The inert gas, typically argon, protects the weld area, ensuring stability and preventing oxidation. TIG welding excels with thinner materials and non-ferrous metals like aluminum and magnesium, yet it requires skilled operators due to its complexity and slower speed.
Gas Metal Arc Welding, known as MIG welding, strikes a balance between proficiency and ease of use. It utilizes a continuous wire feed as an electrode and employs a shielding gas to protect against contamination. Popular in automotive and manufacturing, MIG welding is appreciated for its speed and efficiency on non-ferrous metals and carbon steel. Beginners often favor MIG welding due to its straightforward operation and cleaner results, though it’s less suitable for outdoor tasks without proper shielding gas adjustments.
different types of pipe welding
Flux Cored Arc Welding presents a twist to MIG, using a wire with a flux core that provides its shielding. Designed for thicker materials, FCAW can be employed in environments with drafts or gusts without a shielding gas, thus extending its utility outdoors. This method is particularly favored in heavy equipment repair and structural steelwork. The flux core wire not only works well in various positions but also tends to produce higher deposition rates, yet like SMAW, it may leave slag on the weld that needs cleaning.
Submerged Arc Welding is renowned for its efficiency in large-scale industrial applications. Unlike the aforementioned methods, SAW involves a continuously fed consumable electrode and a layer of flux applied over the welding area, which melts to form a protective barrier. Used prominently in pipeline construction and shipbuilding, SAW is cherished for its deep penetration, minimal spatter, and high deposition rates. Though limited to horizontal welding positions, its applicability on thick materials is unmatched, producing strong and stable welds at impressive speeds.
Transitioning from theory to practice, the choice of welding technique hinges on several factors material type and thickness, environment, speed requirements, and weld quality imperatives. Professionals seasoned in pipe welding recognize the significance of mastering multiple methods, allowing for adaptability and superior outcomes tailored to client specifications.
The foundation of expertise in pipe welding lies in rigorous training and certification. Programs accredited by organizations like the American Welding Society (AWS) and the American Society of Mechanical Engineers (ASME) ensure welders are equipped with both theoretical knowledge and practical proficiency. Such formal training is integral in fostering trust and authority, as certified welders are seen as reliable architects capable of traversing the diverse landscape of pipe welding demands.
In conclusion, a profound understanding of different types of pipe welding primes professionals to deliver superior results across numerous industrial sectors. By honing skills and embracing continuous learning, welders can not only fulfill immediate project demands but also propel their careers toward new heights, establishing themselves as esteemed experts in their field. With a steadfast commitment to quality, safety, and innovation, the world of pipe welding offers endless opportunities to explore and conquer.