Electric Motor Housing Design Considerations and Materials
The electric motor housing is a critical component in electric vehicles (EVs) and other applications that require reliable and efficient power transmission. It not only protects the motor from external elements but also plays a crucial role in heat dissipation, noise reduction, and overall system performance. In this article, we will discuss the design considerations and materials used in electric motor housings.
Design Considerations
1. Size and Shape The size and shape of the electric motor housing must be optimized to fit within the available space and meet the functional requirements of the application. This includes considering factors such as weight, balance, and accessibility for maintenance.
2. Thermal Management Electric motors generate heat during operation, which can lead to overheating if not properly managed. The housing must be designed with adequate cooling channels or fins to dissipate heat effectively. Additionally, the material used should have good thermal conductivity to ensure efficient heat transfer.
3. Noise Reduction Electric motors can produce significant noise, which can be detrimental to the overall performance and user experience of the device. The housing can be designed with sound-absorbing materials or features to reduce noise levels.
4. Durability and Strength The housing must be robust enough to withstand the rigors of the application without compromising its functionality. This includes considering factors such as impact resistance, corrosion resistance, and fatigue strength.
5. Cost The cost of the electric motor housing is an important consideration, especially in mass-produced applications Cost The cost of the electric motor housing is an important consideration, especially in mass-produced applications
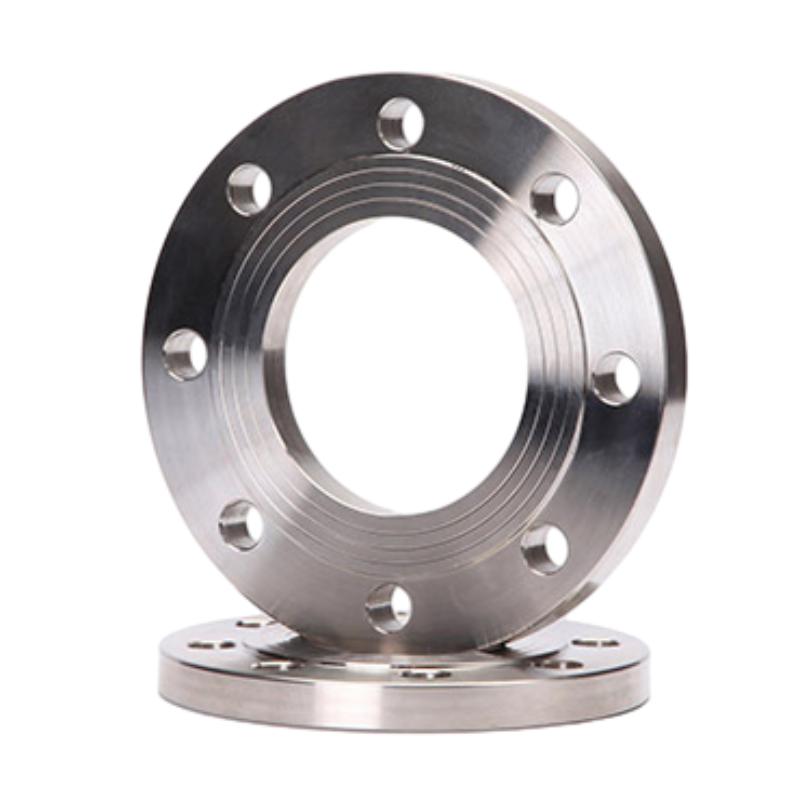
Cost The cost of the electric motor housing is an important consideration, especially in mass-produced applications Cost The cost of the electric motor housing is an important consideration, especially in mass-produced applications
electric motor housing. The material and manufacturing process chosen should be cost-effective while still meeting the performance requirements.
Materials Used in Electric Motor Housings
1. Aluminum Aluminum is a popular choice for electric motor housings due to its excellent thermal conductivity, light weight, and corrosion resistance. It is also relatively easy to machine and form into complex shapes.
2. Magnesium Magnesium is another lightweight metal that is commonly used in electric motor housings. It has a higher strength-to-weight ratio than aluminum and can provide better thermal management due to its higher thermal conductivity. However, it is more expensive and more difficult to machine than aluminum.
3. Plastic Plastic is a popular choice for electric motor housings due to its low cost, light weight, and ability to be molded into complex shapes. However, it may not offer the same level of durability and thermal management as metals.
4. Composites Composites, such as carbon fiber-reinforced polymers (CFRPs), are becoming increasingly popular in electric motor housings due to their high strength-to-weight ratio, excellent corrosion resistance, and ability to be tailored to specific performance requirements. However, they can be more expensive than traditional materials.
In conclusion, the design and material selection of electric motor housings are critical factors that affect the performance, reliability, and cost of the overall system. By considering the various design considerations and materials available, engineers can create efficient and cost-effective electric motor housings that meet the needs of a wide range of applications.