EN 10216-2 is a crucial specification for seamless steel tubes, primarily employed in applications where high-temperature service is needed. Understanding the dimensions of EN 10216-2 pipes is essential for engineers and designers in sectors such as power plants, automotive, oil and gas, and chemical industries, where precision engineering, safety, and integrity are non-negotiable.
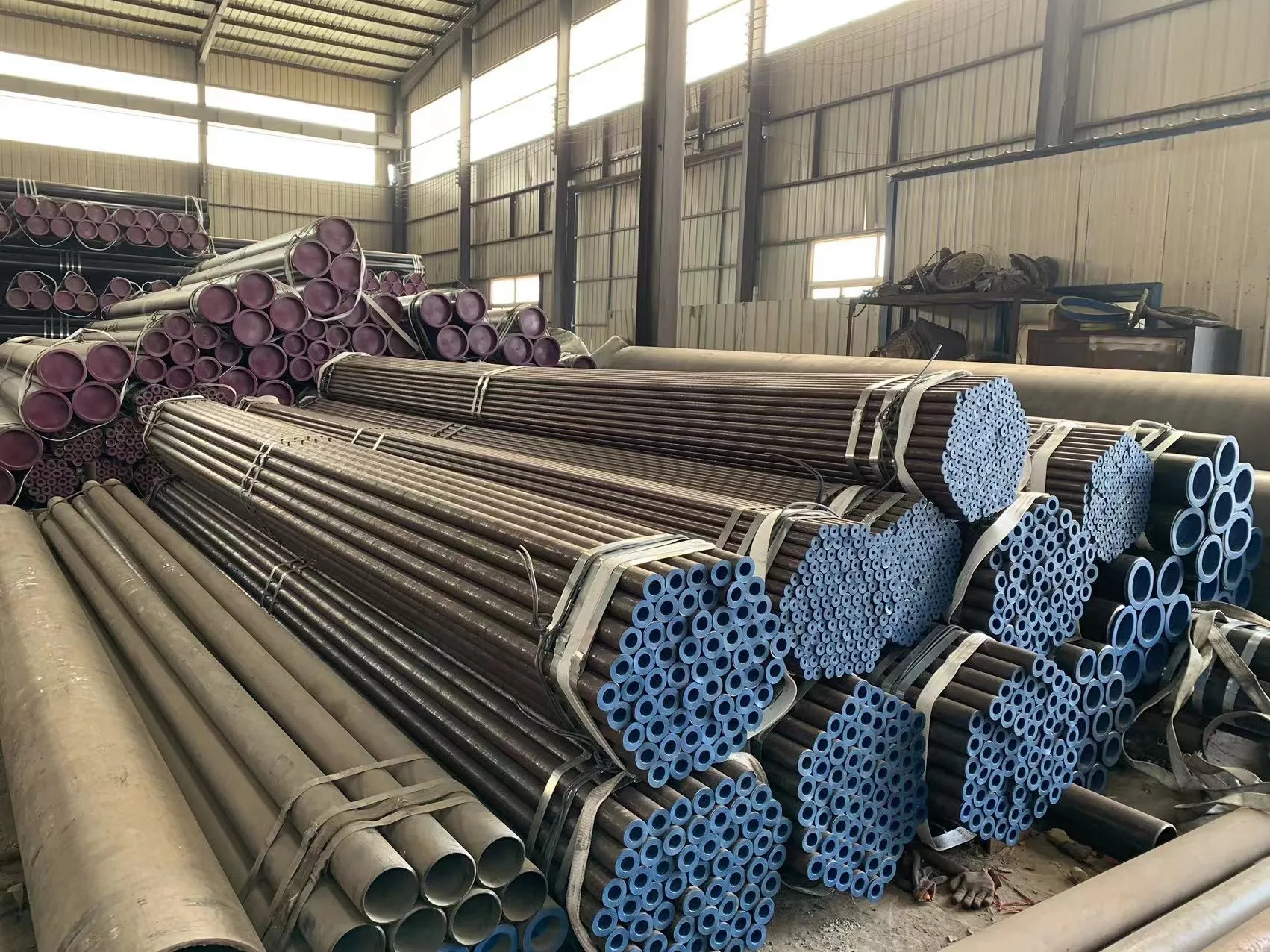
EN 10216-2 pipes are known for their specific chemical compositions and mechanical properties, which are specified for high-temperature uses. The production process involves a meticulous procedure ensuring each pipe meets the stringent European standards. The pipes are seamless, meaning they are created without a weld seam, making them ideal for high-pressure conditions.
Dimensions of EN 10216-2 pipes are diverse and depend greatly on their intended use. They range in outer diameter from small bore tubes starting at 10.2 mm to large bore tubes reaching up to 711 mm. Wall thickness also varies, typically from 1.2 mm to 60 mm, though custom dimensions can be achieved through special manufacturing processes. The variety in dimensions allows for considerable flexibility in design and application.

This dimension range is specified to cater to varied operational pressures and temperatures. Industries focusing on high-efficiency heat transfer, such as boilers or heat exchangers, often prefer pipes with a relatively thin wall to ensure optimal thermal conductivity. Conversely, systems managing substantial mechanical stresses, like those in heavy machinery, might necessitate a thicker wall for enhanced strength and durability.
Materials used in EN 10216-2 pipes are primarily non-alloy and alloy steel grades. Common grades include P235GH, P265GH, 16Mo3, and others, each offering unique properties for specific environments. For instance, P235GH is a popular choice due to its good weldability and bendability, combined with excellent heat resistance, making it suitable for medium-pressure applications. On the other hand, 16Mo3 contains molybdenum, increasing its resilience against corrosion and improving its tensile strength under high temperatures, which is critical for applications in harsh environments.
en 10216 2 pipe dimensions
Given the technical nature of these pipes, purchasing decisions should consider not only the dimensions but also the specific mechanical and chemical properties required for the application. Verification against EN 10216-2 standards is essential, and pipes should ideally be accompanied by a manufacturer's test certificate that confirms compliance with dimensional and material specifications.
The quality control in manufacturing EN 10216-2 pipes is rigorous. Each batch undergoes non-destructive testing (NDT), dimensional inspection, mechanical testing, and chemical analysis to ensure they can withstand the operational challenges. NDT methods such as ultrasonic testing are frequently employed to detect internal flaws, while dimension checks ensure consistency with specified tolerances.
Ultimately, leveraging the correct dimensions and materials for EN 10216-2 pipes contributes significantly to the efficiency, safety, and longevity of the projects they are used in. Companies supplying these pipes play a key role in guiding selection based on application requirements, offering expert insights derived from years of experience and technical expertise.
For project managers and engineers, an extensive understanding of the EN 10216-2 standard, and attentiveness to pipe dimensions and properties, is instrumental. It assures the seamless integration of these critical components into larger systems, fulfilling both functional and regulatory obligations. By choosing the right dimensions, backed by expert recommendations and stringent compliance, industries can achieve optimal performance and reliability in their high-temperature operations.