Fitting galvanized pipes is an essential task in various construction and plumbing projects, offering durability and strength where corrosion resistance is crucial. Whether you are an industry professional or a DIY enthusiast, understanding the nuances of galvanized pipe installation can save time, ensure safety, and improve longevity. This guide provides an in-depth look into the process, practical insights, and professional tips to achieve optimal results.
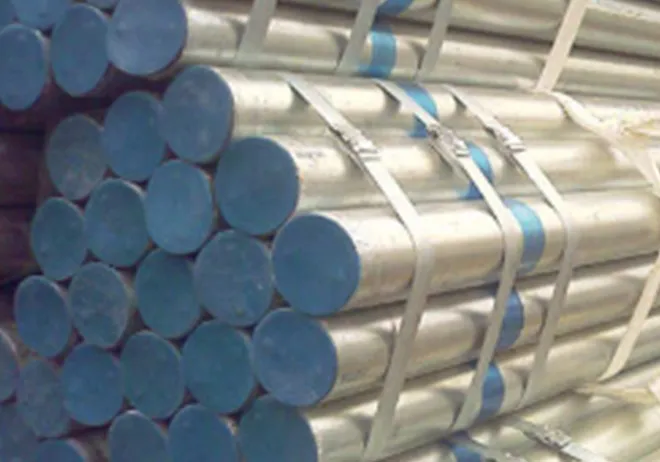
Galvanized pipes are steel pipes coated with a protective layer of zinc to prevent rust and corrosion, which are common in both residential and commercial infrastructures. Their fittings, such as elbows, tees, and couplings, are equally critical in maintaining the integrity and function of the piping system. The zinc coating acts as a barrier or sacrificial layer, affording the steel below enhanced durability in wet environments, making them ideal for water supply lines.
Choosing the Right Fittings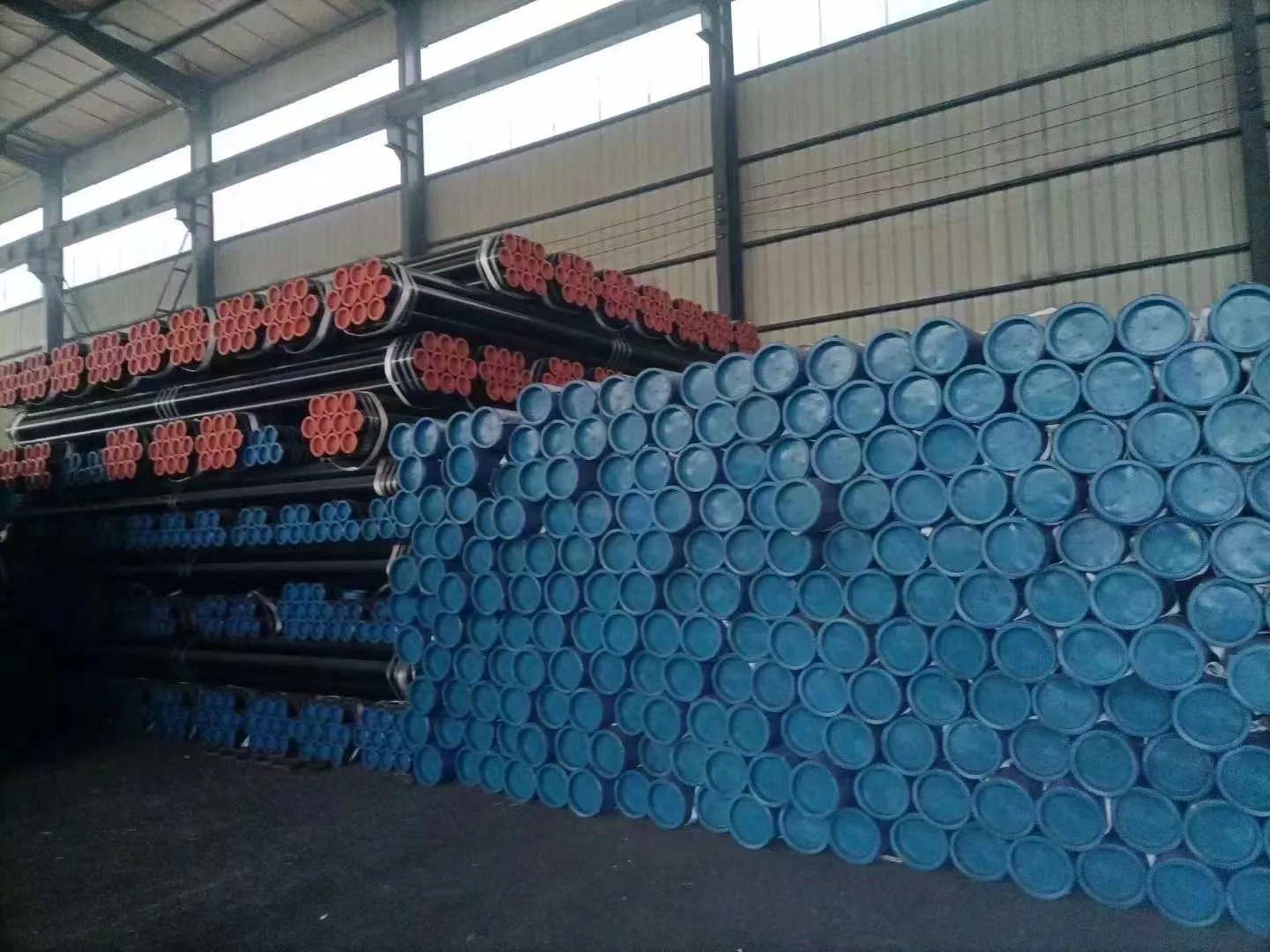
Selecting the appropriate fittings is the cornerstone of a secure galvanized piping system. Consider the pipe's specifications diameter, wall thickness, and intended use. For scenarios involving high pressure, thicker fittings are advisable. Be cautious of mismatched galvanizing; ensure uniformity between pipes and fittings to prevent galvanic corrosion.
Preparation and Tools
Before commencing the fitting process, gather all necessary tools pipe wrench, pipe cutter, reamer, and threading oil. Protective equipment, such as gloves and safety goggles, is essential to prevent injury. A clean workspace reduces the likelihood of contaminants interfering with the threading process.
Thread Cutting and Cleaning
Galvanized pipes require precise thread cutting, a critical phase that ensures leak-free joints. Utilize a die stock threader for uniform threading. Excess zinc may clog the threads, so cleaning the pipe's edges with a reamer and a brush post-threading is crucial. This step ensures a snug fit by removing any burrs or excess metal.
Fitting Assembly
fitting galvanized pipe
Apply a suitable pipe sealant or thread tape - usually PTFE tape - around the male threads to ensure airtight connections. Tighten the joints with a pipe wrench, but be careful to avoid over-tightening, which can compromise the pipe's integrity. Refer to manufacturer torque specifications to ensure accuracy.
Pressure Testing
After assembly, it's crucial to test the system's integrity. A pressure test will reveal any leaks or weak points in the fitting. Begin with a low-pressure test, gradually increasing to operational pressure. Consistent pressure and no visible drops indicate a successful installation.
Common Mistakes
One common error is failing to differentiate between galvanized pipes and regular iron pipes. Their appearances may be similar, but their compatibility is significant for corrosion prevention. Another is neglecting the integrity of the zinc coating during the threading process, which can lead to rapid deterioration if not appropriately addressed.
Maintenance and Longevity
Galvanized piping systems, though resistant to rust, require periodic inspections. Check for signs of corrosion, especially in areas where the coating may have been damaged. Regular maintenance involves checking all fittings and joints to ensure they remain tight and free from leaks.
Conclusion
The art of fitting galvanized pipes combines foundational knowledge with the precision of good craftsmanship. By following these guidelines, you'll enhance not only the effectiveness but also the lifespan of your piping systems. Remember, as straightforward as it may seem, the nuances and attention to detail in fitting galvanized pipes make the difference between a secure and secure system. By prioritizing quality materials and practices, you're investing in the reliability and safety of your infrastructure.