In the intricate world of mechanical and structural engineering, the flange emerges as an essential component bridging efficiency with safety. Ensuring mechanical stability and continuity, this seemingly simple piece of hardware plays a pivotal role in industries ranging from aerospace to plumbing. As someone who has spent years delving into the core of engineering solutions, I can confidently say that choosing the right flange is more than just about specifications; it's about comprehensive understanding and strategic integration into systems.
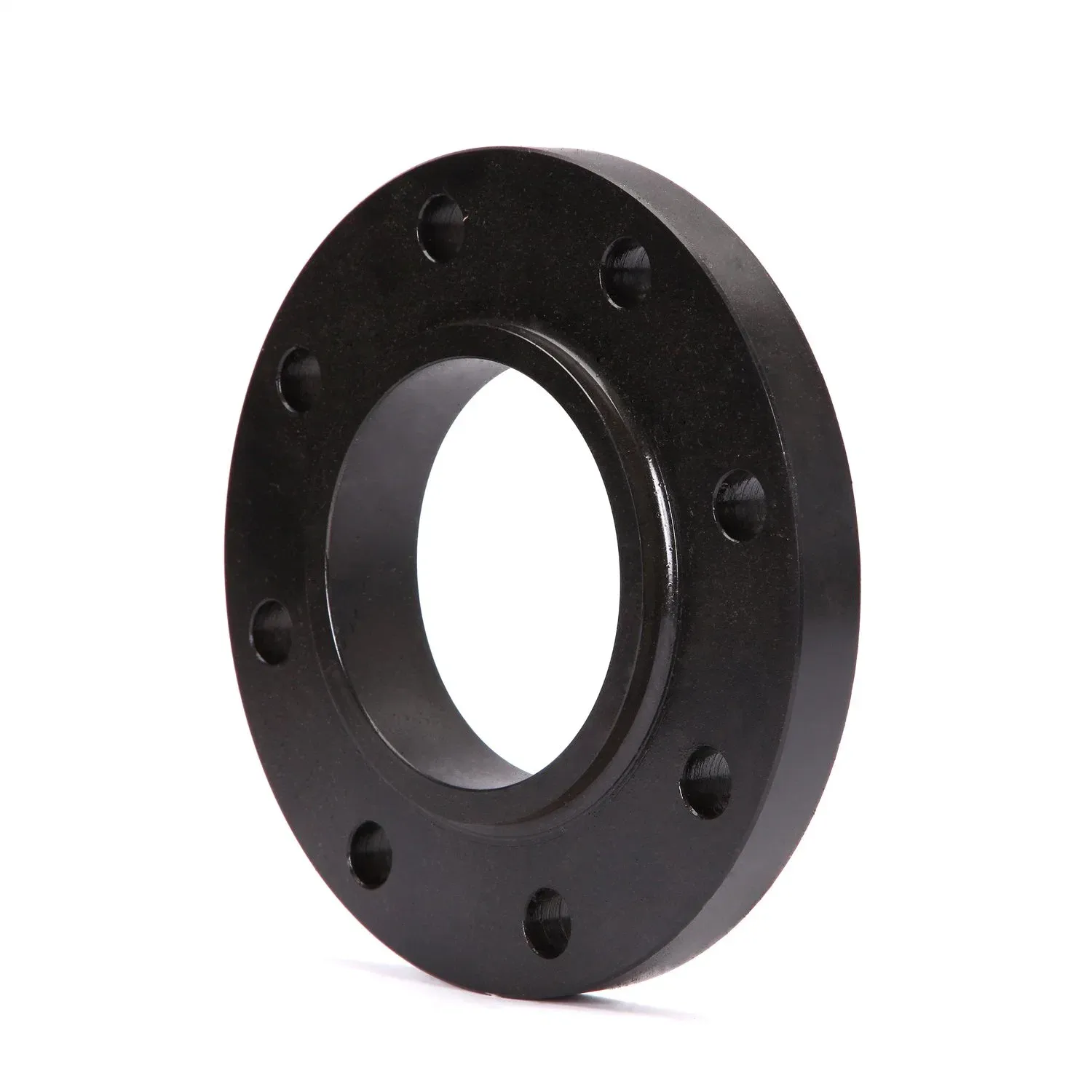
A flange, in essence, serves as a robust connector that links pipes, valves, pumps, and other equipment to form a coherent, operational system. It facilitates the assembly and disassembly of these systems, ensuring maintenance and inspections are not only possible but efficient. There are numerous types of flanges, including welding neck flanges, slip-on flanges, blind flanges, and socket weld flanges among others, each meticulously designed to cater to specific requirements and constraints.
Expertise in flange selection pivots on understanding the environmental conditions in which they will operate. Considerations include temperature fluctuations, pressure levels, and the chemical properties of the materials being transported. This is especially crucial in high-stake industries such as oil and gas, where the integrity of a flange can mean the difference between safe operations and catastrophic failures.
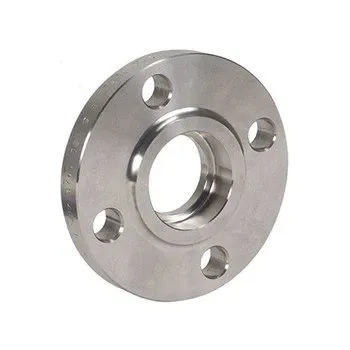
Furthermore, material selection cannot be underestimated. Flanges are typically constructed from stainless steel, carbon steel, aluminum, or exotic alloys. The choice of material impacts the flange's corrosion resistance, strength, thermal properties, and, ultimately, its longevity. For instance, stainless steel flanges are renowned for their corrosion resistance and are popular in industries dealing with harsh chemical environments.
flange
The importance of regulatory compliance and standards also comes into play, making it imperative for engineers to adhere to international standards such as ANSI, ASME, and DIN. These standards ensure that flanges are manufactured to consistent quality and safety benchmarks, enhancing trustworthiness and reliability in their application.
Installation precision is another critical factor. The deployment of flanges must be performed with meticulous attention to detail to mitigate risks of leaks and misalignments that could compromise system integrity. Skilled technicians employ torque wrenches to follow precise torque sequences, ensuring bolts are tightened to the exact specifications required for optimal performance.
Experience has taught me the invaluable lesson that preventive maintenance can drastically extend the lifespan of any system incorporating flanges. Regular checks for signs of wear and tear, corrosion, and bolt loosening can prevent costly downtime and shield against more severe repercussions. Implementing a proactive maintenance schedule is a hallmark of operational excellence.
In conclusion, the integration of flanges in engineering systems represents a convergence of design, material science, and practical application. A deep understanding of their functions, supported by a robust framework of industry standards and maintained through diligent care, positions organizations to leverage these components to their fullest potential. The reliability and effectiveness of a flange are testaments to the expertise and trustworthiness of those who select and implement them. For industries navigating the complexities of modern engineering challenges, the flange, although small in physical stature, looms large in significance.