Understanding Flanged Expansion Joints A Key Component in Modern Pipeline Systems
Flanged expansion joints, an integral part of various industrial piping systems, play a crucial role in managing mechanical stress and absorbing expansion and contraction. These versatile devices, often found in high-pressure and high-temperature applications, are designed to provide a flexible connection between pipe sections, ensuring the integrity and longevity of the overall system.
An expansion joint, at its core, is a flexible element that compensates for linear or angular movement due to thermal changes or mechanical stress. The term 'flanged' refers to the specific type of connection used, characterized by two flat surfaces with bolt holes, allowing the joint to be securely fastened to the adjacent pipes or equipment.
The flanged design offers several advantages. Firstly, it enables easy installation and maintenance, as the joint can be disconnected and reconnected without requiring additional welding or cutting. Secondly, the flanges provide a strong, leak-tight seal, making them suitable for high-pressure applications. Lastly, the use of standard flange dimensions allows for compatibility with a wide range of pipeline systems.
Flanged expansion joints consist of several components, including bellows, connectors, and restraint components. The bellows, typically made from corrosion-resistant metals, are the primary flexible element that absorbs the majority of the expansion or contraction. The connectors, or flanges, connect the bellows to the pipe and transmit the forces generated by the system The connectors, or flanges, connect the bellows to the pipe and transmit the forces generated by the system
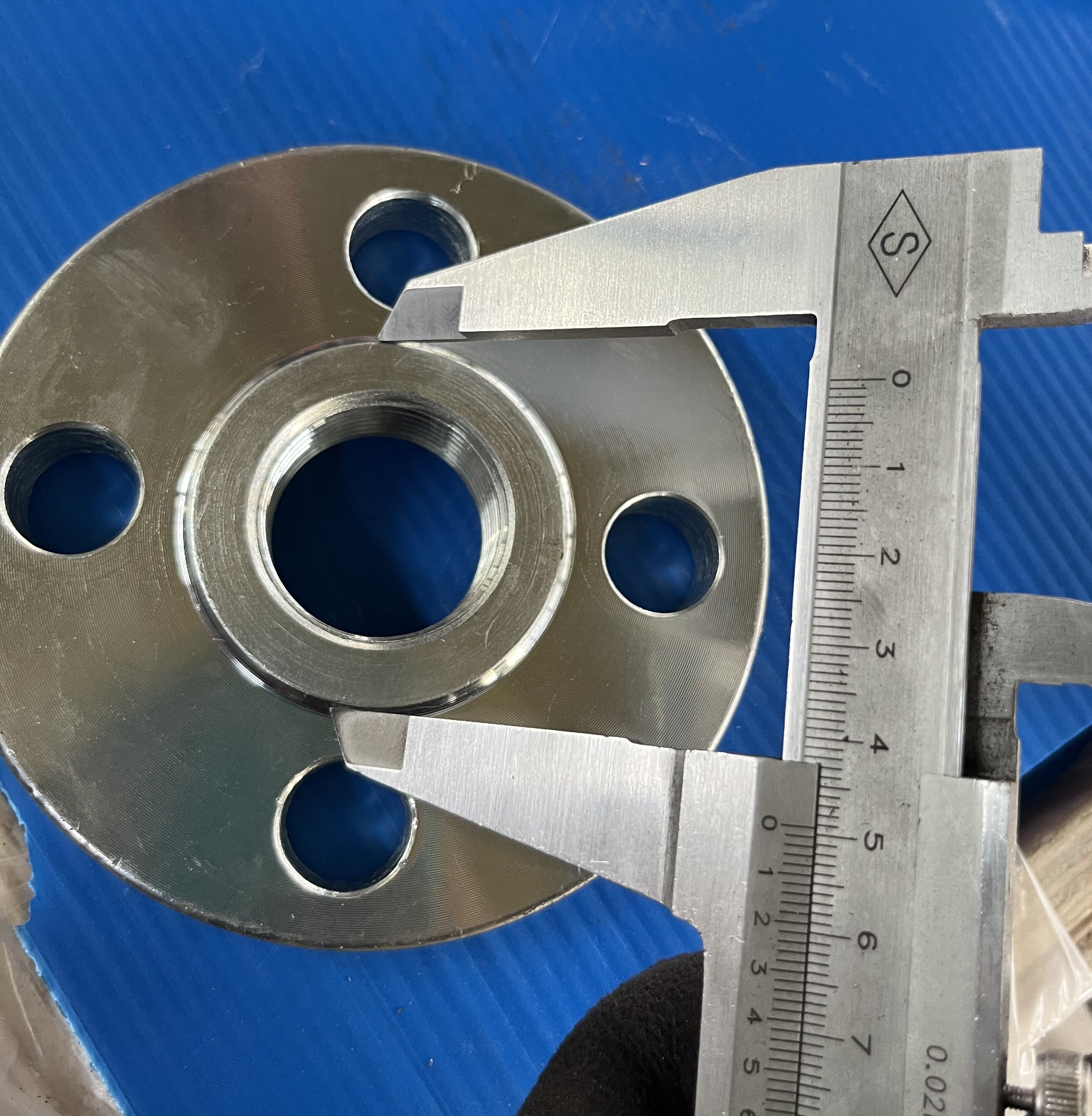
The connectors, or flanges, connect the bellows to the pipe and transmit the forces generated by the system The connectors, or flanges, connect the bellows to the pipe and transmit the forces generated by the system
flanged expansion joint. The restraint components, such as tie rods or U-bolts, prevent excessive movement and ensure the joint's stability.
In addition to their standard applications, flanged expansion joints also find usage in complex situations where there is a need for angular, lateral, or axial movement. They are commonly employed in power plants, chemical processing facilities, petrochemical plants, and even in the HVAC industry for large ductwork systems.
However, proper selection and sizing of flanged expansion joints are critical to their efficient operation. Factors such as operating temperature, pressure, fluid properties, and expected movement must all be considered to determine the appropriate design and material.
In conclusion, flanged expansion joints are indispensable tools in modern pipeline engineering, mitigating the stresses induced by thermal changes and mechanical forces. Their adaptability, strength, and ease of installation make them a preferred choice for engineers seeking to ensure safe and efficient flow in a variety of industrial settings. As technology advances, so too will the design and functionality of these essential components, further enhancing their role in maintaining the robustness and resilience of our industrial infrastructure.