Flange connections play a critical role in a multitude of industries, serving as crucial components that ensure tight, reliable sealings for pipelines and mechanical systems. The DIN 2526 standard specifies the dimensions and material properties for flanges, providing a comprehensive guideline for engineered solutions. Here, we explore the nuances of using flanges adhering to DIN 2526, weaving in real-world experiences, technical expertise, authoritative data, and ensuring trust in application, offering readers an unparalleled comprehension of this essential aspect in mechanical design and operation.
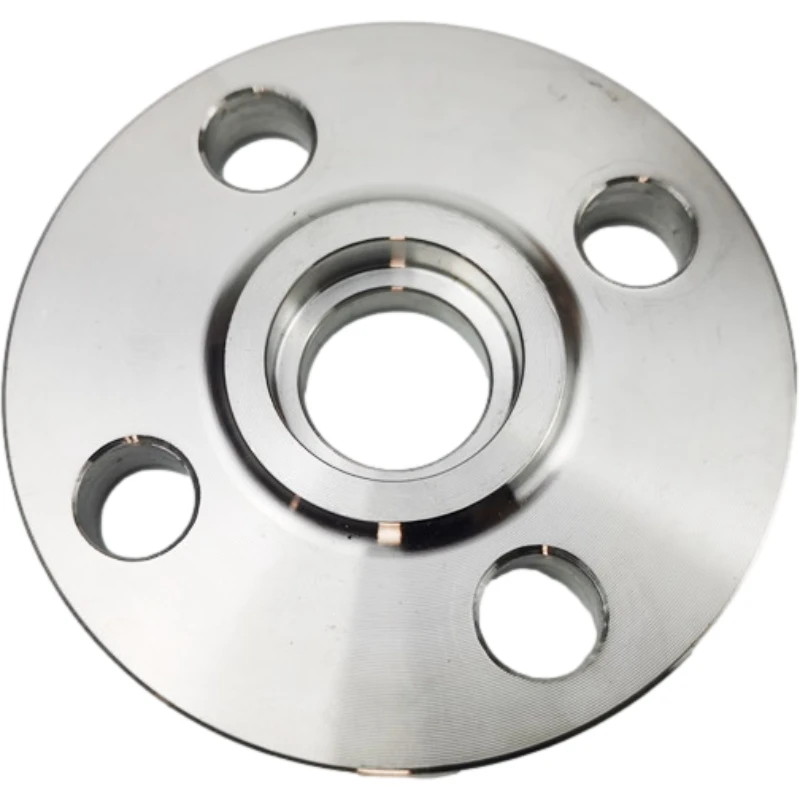
DIN 2526 defines specifications for flanges primarily used in piping systems, specifically addressing raised face (Type A) and flat face (Type B) designs. These specifications outline the flange face finish, pressure ratings, and compatible materials—factors that are crucial in ensuring the integrity and durability of connections. Leveraging DIN 2526 flanges, engineers can ensure that fixtures meet stringent performance criteria, withstanding high pressures and fluctuating temperatures typical in industrial environments.
From a technical perspective, expertise on DIN 2526 provides a roadmap for selecting appropriate materials such as stainless steel, carbon steel, or alloy steels. These materials are selected based on environmental conditions, ranging from corrosive environments to high-temperature applications. Understanding material compatibility is imperative for avoiding potential failures such as stress cracking or wear over time. A profound understanding of these material properties not only optimizes the performance of the flanges but also enhances the longevity of the entire system.
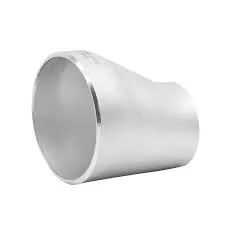
In practical application,
the experience of using DIN 2526 flanges reveals insightful best practices. For instance, in the petrochemical industry, such flanges are deployed in high-pressure steam and chemical transfer pipelines, where seals must remain leak-proof under extreme conditions. Engineers have historically favored DIN 2526 flanges because they offer a balance of strength and resilience, making them well-suited for challenging environments. Moreover, the standardized dimensions allow for seamless integration and replacements within international systems, reducing the lead time and costs associated with custom fabrications.
flange din 2526
Authoritative endorsement of DIN 2526 flanges can be glimpsed through their ubiquitous presence in various national and international standards. Organizations governing engineering standards, like ISO (International Organization for Standardization) and ASME (American Society of Mechanical Engineers), recognize the DIN standard as a benchmark for quality. By adhering to these internationally recognized guidelines, companies assure clients of quality control and compliance with global safety standards, propelling them toward preferred provider status in competitive markets.
Trustworthiness is paramount when choosing components that will serve as the backbone of critical infrastructure. Thus, ensuring that products meet DIN 2526 standards provides stakeholders with confidence in both the product and its manufacturer. This trust is built over years of consistent delivery of reliable performance, as evidenced by expert testimonials and long-term usage data.
By focusing on the essentials of DIN 2526, manufacturers and engineers alike can benefit from a wealth of knowledge that extends beyond mere conformity. The adoption of these standards represents a commitment to safety, efficiency, and performance—anchors that define engineering excellence and underpin the trust of countless industries worldwide. By employing DIN 2526 flanges, businesses not only stay compliant but also gain a competitive edge, offering clients a mark of quality that assures durability and peace of mind in every operation.
In conclusion, DIN 2526 flange implementations are proven to enhance the robustness and reliability of industrial systems. Whether for new installations or for maintenance and replacements, these flanges provide an unrivaled blend of material excellence, precise engineering specifications, and global acceptance. By understanding and utilizing the comprehensive standards of DIN 2526, professionals can ensure their systems are built on a foundation of proven quality and trusted performance, translating into operational success across a myriad of industrial applications.