Navigating the world of industrial components can often seem like an intricate dance of precision and understanding—particularly when discussing niche yet significant components like flange rollers. These critical components are a staple in various industrial sectors, facilitating smooth operations and efficient mechanical actions. Below, we'll delve into the essential aspects of flange rollers through the lens of real-world applications, backed by professional insight and an authoritative overview that reinforces their critical functionality and necessity.
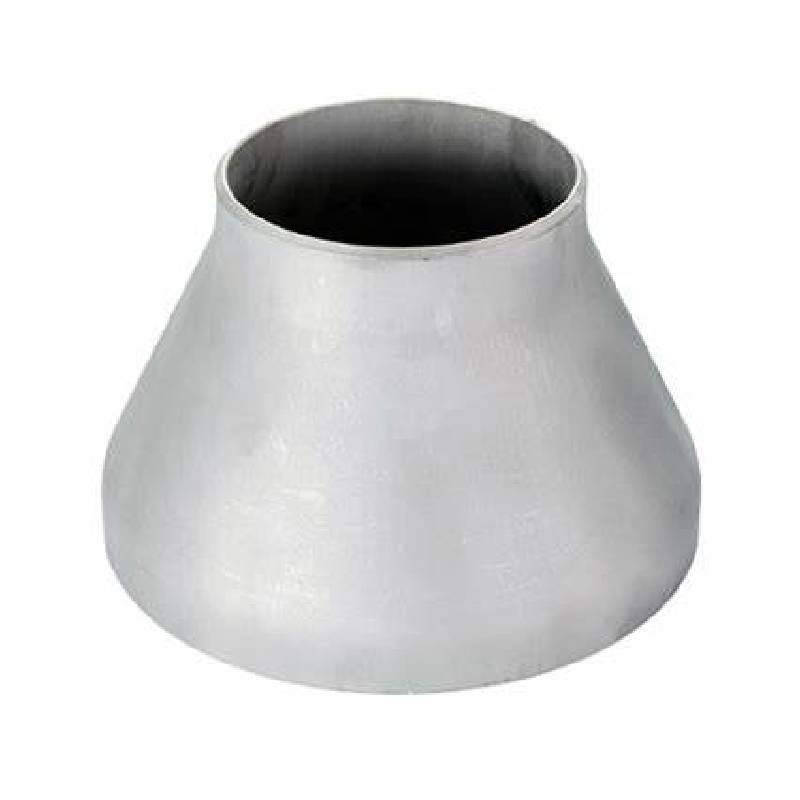
Flange rollers are a specialized variety of roller device typically employed in conjunction with track systems. They are characterized by a flange, which acts as a guide to prevent the wheel from traversing out of its designated track. This specific feature not only enhances the efficiency of the system but also fortifies the safety parameters across various industries, including manufacturing, logistics, and heavy machinery.
Experience derived from multiple industries illustrates that flange rollers play a pivotal role in enhancing operational precision. Consider a high-stakes environment, such as an automotive manufacturing plant, where assembly lines rely on the uninterrupted movement of materials. A flange roller, precisely engineered to withstand substantial loads while maintaining frictionless movement across tracks, becomes indispensable. Industry professionals recognize that investing in high-quality flange rollers mitigates downtime and maintenance costs, contributing significantly to productivity and cost efficiency.
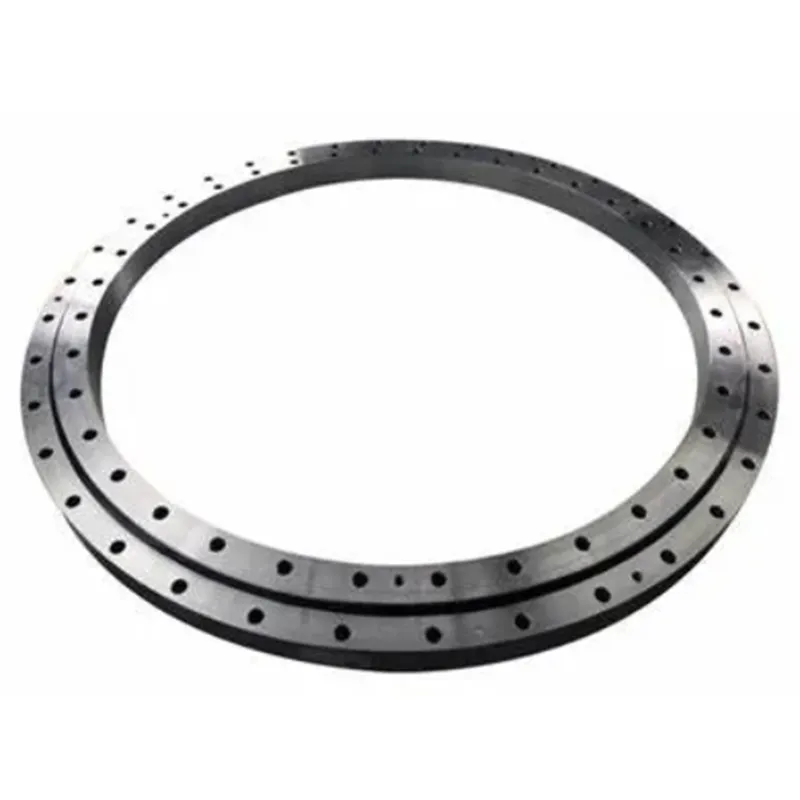
In terms of expertise, selecting the right flange roller requires an in-depth understanding of material science and engineering. Top-tier flange rollers are typically manufactured from robust materials such as hardened steel or specially formulated polymers, each chosen based on application-specific requirements such as load capacity, environmental conditions, and speed of operation. Engineers meticulously design these rollers to endure extreme conditions, such as abrasive environments, temperature fluctuations, and heavy-duty loads, ensuring longevity and consistent performance.
flange roller
Authoritativeness in the context of flange rollers is largely determined by adherence to stringent industry standards and testing protocols. Reputable manufacturers subject their products to rigorous tests that simulate real-world conditions to ascertain durability and reliability. Compliance with international standards—such as ISO certifications—serves as a hallmark of quality and safety, providing end-users with the assurance that they are investing in components that will not only meet but often exceed operational demands.
Trustworthiness is perhaps the most critical component when evaluating flange rollers for industrial use. Trust is built through consistent performance, positive testimonials from industry peers, and a reputation for reliability. Many businesses share case studies and success stories that highlight the dependability of their chosen flange rollers. For example, a logistics company may report a marked improvement in conveyor system efficiency after switching to flange rollers with enhanced load-bearing capabilities, reinforced by positive feedback from their maintenance team due to reduced servicing frequency.
Beyond technical specifications and performance metrics, the choice of flange rollers often reflects a company's commitment to sustainability. Eco-conscious businesses favor flange rollers produced using environmentally friendly processes and recyclable materials, thereby reducing carbon footprint while maintaining industrial efficiency.
In conclusion, flange rollers might initially appear to be a minor component within a grand industrial framework, yet their role is anything but insignificant. The confluence of real-world usage, professional input, and adherence to global standards underpins the trust and reliance placed on these components. As industrial demands evolve, so too do the engineering and materials science criteria for flange rollers, paving the way for continued innovation and elevated performance standards. Companies looking to gain a competitive edge understand the importance of integrating high-quality flange rollers into their product lines, ensuring not only operational efficacy but also aligning with broader goals of sustainability and industry leadership.