Flange types play a critical role in the assembly and functionality of piping systems across various industries, offering both structural and performance benefits. Each flange type is uniquely designed to meet specific requirements, and understanding these can enhance decision-making in procurement, installation, and maintenance. Below, we've demystified different flange types, focusing on their real-world applications, material compatibility, installation, and performance nuances.
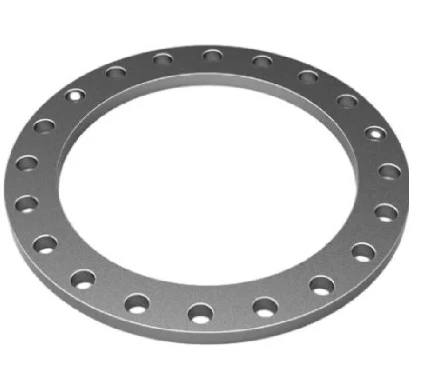
Slip-On Flanges are widely appreciated for their ease of use and cost-effectiveness. Their simplicity in design, allowing them to slide over pipes, makes them a favorite for low-pressure settings and applications requiring quick installations. Ideal for water treatment plants and low-pressure air systems, slip-on flanges require fillet welding at the hub of the pipe and the flange, ensuring a secure fit. Despite their ease of installation, ensuring proper alignment is crucial; improper installation can lead to leaks and potential system failures.
Weld Neck Flanges are the go-to choice for high-pressure applications, providing superior structural support and stress distribution.
This flange type is easily identified by its protruding neck, which butt-welds to the pipe. This design not only offers an excellent seal, minimizing chances of leaks, but also reduces turbulence and erosion inside the pipe. Oil and gas industries heavily rely on weld neck flanges for their pipelines due to their ability to withstand extreme temperatures and pressures over prolonged periods.
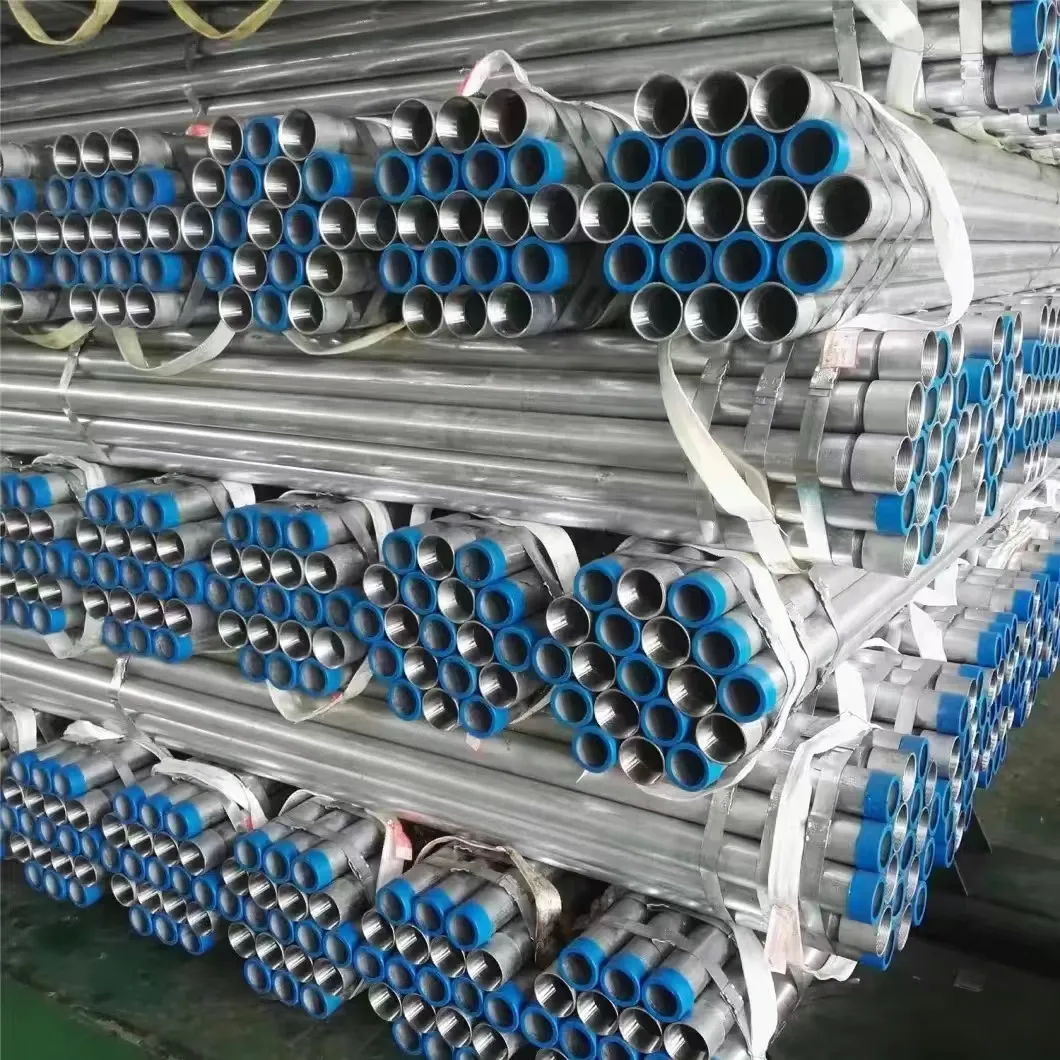
Blind Flanges serve as end caps in piping systems, effectively sealing systems during maintenance or repair. They are instrumental in preventing flow within pipe sections, making them essential during system inspections and integrity tests. Industries where regular maintenance checks are paramount, like chemical manufacturing, benefit greatly from blind flanges' capability to isolate piping sections without dismantling extensive infrastructure.
Socket Weld Flanges are engineered for high-pressure, small-diameter applications. The flange possesses a socket in which the pipe is inserted, and then fillet welded around the hub. This creates a strong, leak-proof connection. Industries dealing with toxic or expensive chemicals, where leaks cannot be afforded, value socket weld flanges for their reliability in maintaining a sealed system. However, the downside of this flange is the potential for stress corrosion, especially when used with stainless steel pipes, necessitating meticulous material selection and application planning.
flange types
Lap Joint Flanges are designed for applications where frequent dismantling is required for inspection or cleaning purposes. While they feature a loose flange, which is not directly welded to the pipe and thereby allows for rotational freedom, they rely on the backing flange to provide a seal. This setup, while suitable for low-pressure applications, requires caution as misalignment during installation can compromise the seal's effectiveness. Petrochemical refineries and food processing plants benefit from their versatility and ease of assembly and disassembly.
Threaded Flanges, though not as commonly used today due to advancements in welding technology, remain relevant in scenarios where welding could pose a risk, such as in explosive or flammable environments. Threaded flanges don't require welding, making them ideal for small, high-pressure systems where heat from welding could result in system vulnerabilities. Their maintenance simplicity often outweighs their limitations in handling vibration compared to other, welded counterparts.
Each flange type has its ideal use case, and the choice hinges on factors like pressure ratings, installation environment, and operational conditions. An in-depth understanding of these variables can significantly boost system efficiency, cost-effectiveness, and longevity.
For businesses looking to apply the right flange types to their piping systems, it’s essential to consult with vendor experts, evaluate long-term performance data, and consider future system modifications or expansions. Correct flange selection not only enhances system integrity but also safeguards against premature failures and operational hiccups, ensuring seamless productivity across operations.