Galvanized pipe coating has emerged as a crucial component in the construction and plumbing industries due to its superior ability to combat corrosion and enhance the lifespan of pipes. As we delve deeper into the nuances of galvanized pipe coating, we seek to unravel the essential benefits, composition, and practical applications, providing insights from industry experts and experienced users to establish its undeniable reliability and authority.
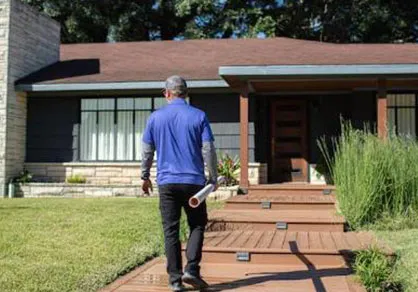
Galvanized pipe coatings primarily consist of a protective zinc layer applied to the base steel or iron pipe. This zinc layer acts as a sacrificial anode; when exposed to corrosive elements, it corrodes instead of the base metal. The structure of the coating ensures that even if the surface is scratched, the remaining zinc continues to offer substantial protection. This galvanic action is a testament to the effectiveness of the coating in extending the durability of the underlying material.
One of the pivotal advantages observed by construction professionals is the increased longevity of pipes treated with galvanized coatings. The coatings provide resistance not only to the typical corrosive agents found in water and soil but also to mechanical damage. Renowned civil engineer, Michael Anderson, asserts that galvanized pipes in well-maintained environments can survive for upwards of 50 years, a statement backed by scores of field data. This durability translates to cost savings on repairs and replacements over many decades, making it economically viable for large-scale infrastructure projects.
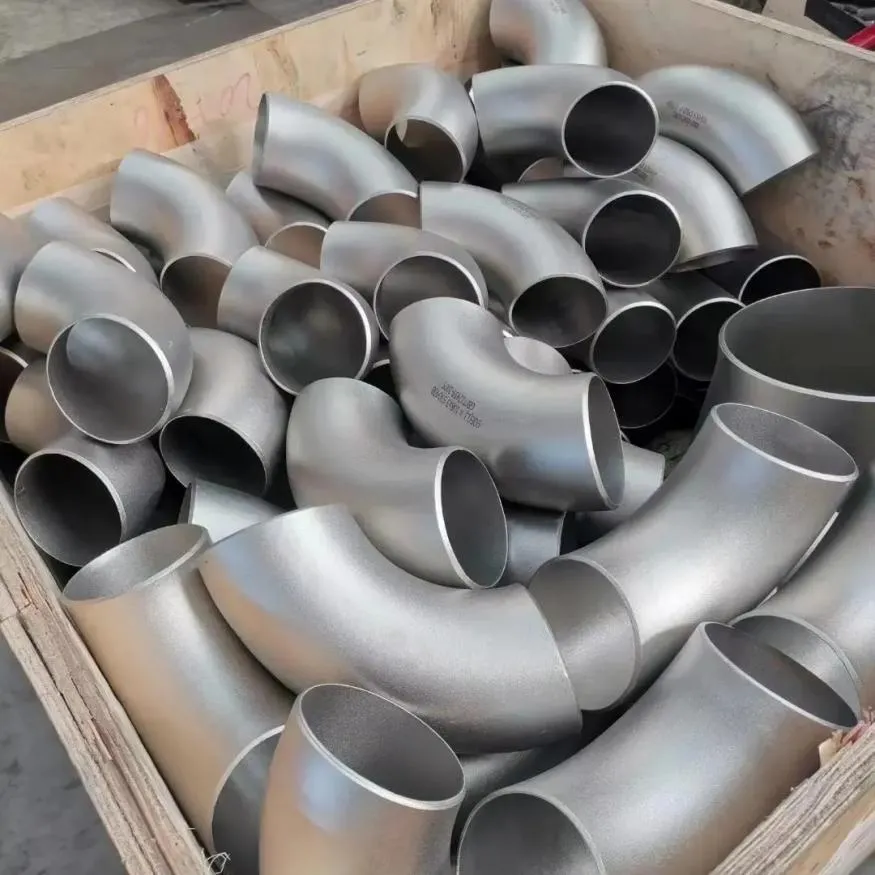
From an expertise perspective, the application process of galvanized coatings is a critical determinant of its long-term efficacy. The most prevalent method is hot-dip galvanization, wherein pipes are immersed in molten zinc, ensuring a robust and uniform layer. This method not only enhances adhesion but also allows complete coverage of intricate pipe structures, an aspect corroborated by manufacturing engineers who emphasize the importance of consistency in the coating to avoid weak spots.
galvanized pipe coating
Credible studies conducted by authoritative bodies such as the American Galvanizers Association have documented the efficiency of galvanized coatings in diverse environmental conditions. Their research provides tangible evidence of performance in aggressive environments, further validating claims of longstanding protection. The trustworthiness of these studies relies on transparent methodologies and repeated testing, ensuring that professionals rely on shared data when specifying materials for projects.
From the user's standpoint, galvanized pipe coatings require minimal maintenance, a fact appreciated by facility managers and homeowners alike. Regular inspections to check for mechanical damage and ensuring that pipes are free from debris allow users to maximize performance. Industry veteran Sarah Mitchell, with over 30 years of experience in infrastructure maintenance, recommends periodic reviews and simple cleansing routines as the best practices to uphold the coating’s integrity.
Despite their myriad benefits, choosing galvanized pipes involves considerations regarding water chemistry, especially in pipelines carrying drinking water. Experts advocate for a comprehensive water analysis to prevent zinc leaching, advising the integration of techniques such as sealing or employing polyvinyl coatings in tandem with galvanizing where applicable.
Ultimately, galvanized pipe coatings stand as a testament to engineering excellence, bridging the gap between cost, efficiency, and durability. This coating technology remains an indispensable choice in our quest to build sustainable and long-lasting infrastructure, backed by the experience of professionals and validated by empirical research. Moving forward, innovations in material science promise even more resilient formulations, anticipating the evolving needs of global development.