Understanding Welding Hose Pipes An Essential Component in Welding Processes
Welding hose pipes, often referred to as welding torch hoses or welding gas hoses, play a pivotal role in the welding industry. They are specifically designed to withstand the high temperatures and pressures associated with welding processes, ensuring safe and efficient transmission of gases and fluids.
A welding hose pipe is essentially a flexible conduit that connects the welding equipment to the source of the welding gas or coolant. It is made from high-quality materials like synthetic rubber, nylon, or a combination of both, providing resistance against heat, flames, and chemical exposure. The robust construction of these hoses ensures durability and longevity even under extreme conditions.
The primary function of a welding hose is to transport shielding gases to the welding area. Shielding gases, such as argon, carbon dioxide, or helium, protect the weld from atmospheric contamination, resulting in cleaner and stronger welds. For instance, in MIG (Metal Inert Gas) and TIG (Tungsten Inert Gas) welding, the hose carries the inert gas to the welding torch, while in plasma cutting, it carries the compressed air or gas to the cutting torch.
In addition to gas delivery, welding hoses are also used to carry water or coolant in some welding processes. This coolant helps to dissipate heat, preventing overheating of the welding electrode or torch, thus extending their lifespan and improving welding efficiency This coolant helps to dissipate heat, preventing overheating of the welding electrode or torch, thus extending their lifespan and improving welding efficiency
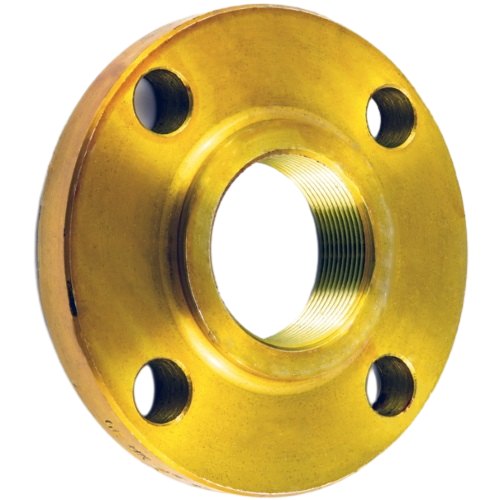
This coolant helps to dissipate heat, preventing overheating of the welding electrode or torch, thus extending their lifespan and improving welding efficiency This coolant helps to dissipate heat, preventing overheating of the welding electrode or torch, thus extending their lifespan and improving welding efficiency
welding hose pipe.
The selection of a welding hose depends on various factors such as the type of welding process, the gas being used, the working pressure, and the environment. Different types of hoses are available for different applications, with some designed for high-pressure use, others for low-pressure, and some specifically for abrasive materials.
When it comes to safety, regular inspection and maintenance of welding hoses are crucial. Cracks, leaks, or signs of excessive wear should be promptly addressed to prevent accidents. It's recommended to replace hoses after a certain period or when they show signs of degradation, as compromised hoses can lead to gas leaks, fire hazards, or even explosions.
In conclusion, welding hose pipes are indispensable components in the welding process, serving as lifelines for the transfer of gases and fluids. Their reliability and resilience make them a critical factor in ensuring the quality, safety, and productivity of welding operations. Therefore, understanding their function, selecting the right one, and maintaining them properly is paramount in the world of welding.