Hot dip galvanized pipes have emerged as indispensable components in numerous industrial applications, offering unparalleled durability and protective attributes that cater to various environments. In-depth insight into these pipes reveals their unique manufacturing process, superior longevity, and diverse application spectrum, ensuring they remain a quintessential choice for professionals seeking reliable material solutions.
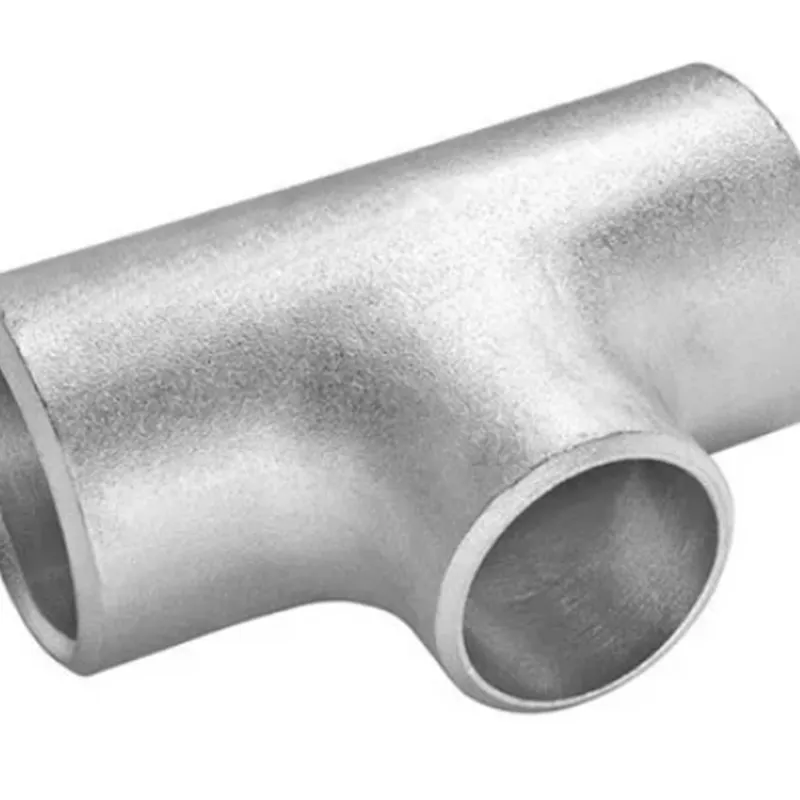
Crafted through the process of immersing steel pipes in molten zinc, hot dip galvanized pipes gain a robust, corrosion-resistant coating that shields the underlying metal from environmental and chemical adversities. This galvanization process offers several advantages over other types of protective coatings, such as paint or electroplating, by forming a metallurgical bond between zinc and steel, thereby enhancing the structural integrity and lifespan of the pipes.
The longevity of hot dip galvanized pipes is particularly noteworthy. The typical service life extends beyond 50 years, making it a cost-effective alternative in the long term compared to other piping materials. The zinc coating corrodes preferentially, which means it sacrifices itself to preserve the core steel, maintaining the structural soundness even in harsh conditions like marine environments, chemical exposure, and varying temperature ranges.
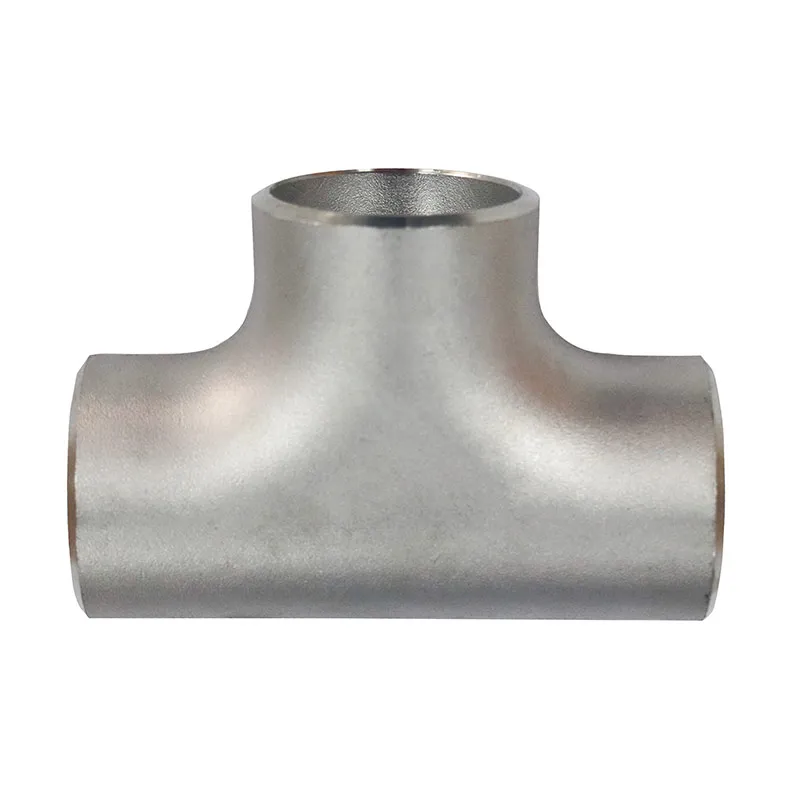
One of the most compelling aspects of these pipes is their versatility in applications. Hot dip galvanized pipes are extensively utilized in the construction industry, not only for structural support but also for conduit and HVAC systems due to their reliable mechanical properties. In agriculture and waterworks, their ability to withstand soil and water-induced corrosion makes them an ideal choice for irrigation and drainage systems. Furthermore, these pipes serve critical roles in the automotive and telecommunication sectors, where their durability and conductive properties are highly valued.
hot dip galvanized pipe
Abundant real-world experiences corroborate the efficacy of hot dip galvanized pipes. Industry experts have observed that these pipes often outperform expectations, especially in infrastructural projects subjected to rigorous testing conditions. For instance, bridge constructors frequently deploy hot dip galvanized pipes for their handrails and safety barriers, astounded by the minimal maintenance required even after decades of exposure to the elements.
The trustworthiness of hot dip galvanized pipes is affirmed by the adherence to international standards such as ASTM A123/A123M, ensuring each pipe is manufactured with consistent and reliable quality. This authoritative endorsement from recognized bodies reassures consumers of its unmatched performance and safety credentials.
In terms of expertise, the production of hot dip galvanized pipes involves sophisticated techniques, requiring skilled professionals to manage the galvanization process effectively. The intricacy involved in ensuring uniform coating thickness, maintaining appropriate temperatures, and achieving the right cooling rates reflects a high level of technical proficiency and commitment to quality.
Choosing hot dip galvanized pipes means investing in a product where real-world experience, technical expertise, authoritative backing, and trust assurance converge to provide a solution that stands the test of time. This makes them not only a preferred choice among engineers and project managers but also a key contributor to the longevity and sustainability of infrastructural developments globally.