The Challenges of Working with Slurry Pumps in Extreme Conditions
In the realm of industrial machinery, slurry pumps occupy a unique niche, often operating under the worst possible working conditions. These robust machines are designed to handle abrasive and corrosive slurries, which can range from mineral ores to wastewater, presenting a litany of challenges that push their engineering limits.
Slurry pumps are predominantly used in industries such as mining, construction, and wastewater treatment, where they are tasked with moving a mixture of solid particles and liquids. The 'worst working conditions' these pumps face are not just about the harsh environment; they encompass extreme temperatures, heavy loads, continuous operation, and exposure to corrosive or abrasive materials.
The first challenge is the abrasive nature of the slurry itself. The solid particles within the slurry can wear down the pump's internal components at an alarming rate, necessitating frequent maintenance and replacement. This constant erosion can significantly reduce the efficiency and lifespan of the pump if not properly addressed.
Corrosion is another major adversary. Depending on the type of slurry being handled, the may be exposed to acidic or alkaline substances that can corrode metal parts. Special materials like high chrome iron, rubber, or ceramic are often used to combat this issue, but even these have their limits.
Temperature extremes also test the resilience of slurry pumps. In hot environments, seals and lubricants can degrade faster, while in cold conditions, the viscosity of the fluid can increase, hindering flow In hot environments, seals and lubricants can degrade faster, while in cold conditions, the viscosity of the fluid can increase, hindering flow
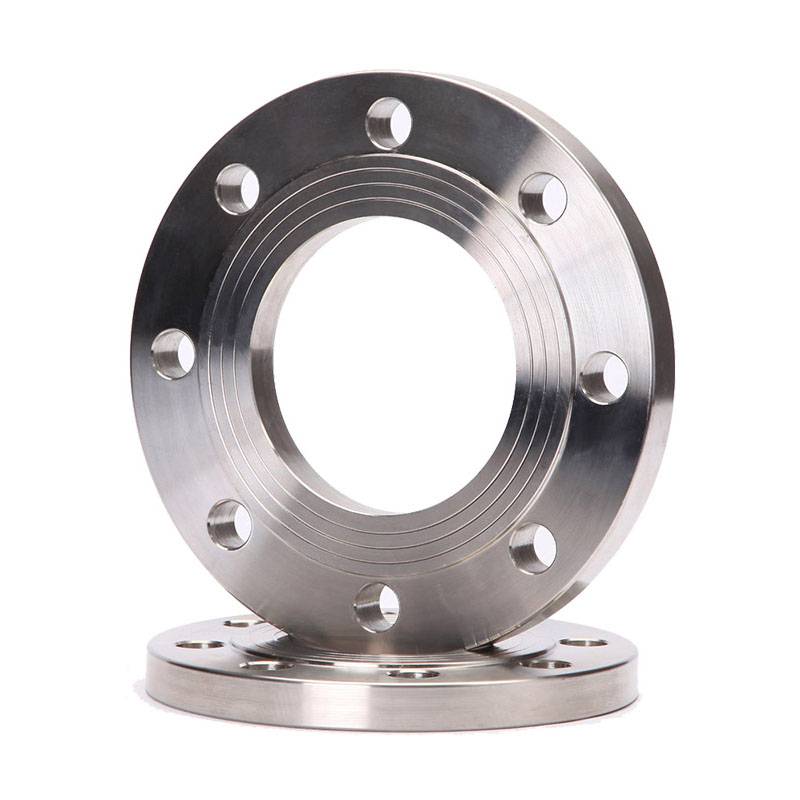
In hot environments, seals and lubricants can degrade faster, while in cold conditions, the viscosity of the fluid can increase, hindering flow In hot environments, seals and lubricants can degrade faster, while in cold conditions, the viscosity of the fluid can increase, hindering flow
worst working conditions slurry pump. Ensuring the pump operates within its optimal temperature range is crucial to prevent premature failure.
Continuous operation is a common requirement for slurry pumps, especially in 24/7 operations like mining. This non-stop workload can lead to overheating and fatigue, necessitating robust cooling systems and regular maintenance intervals.
Lastly, the remote locations of many slurry pump installations add an operational difficulty. Access for maintenance and repair can be limited, making it essential to design pumps that can operate with minimal intervention and withstand harsh environmental conditions.
Despite these adversities, slurry pumps remain indispensable due to their ability to handle materials that other pumps cannot. Technological advancements in materials science, design engineering, and monitoring systems are continually improving their performance and durability, ensuring they can withstand the worst working conditions.
In conclusion, the world of slurry pumps is a testament to the resilience and innovation of engineering. While they operate under some of the most challenging conditions, they continue to evolve, adapting to the demands of industries that rely on them. It's a reminder that even in the harshest environments, human ingenuity prevails, pushing the boundaries of what machines can endure.