Pipe Welding Joint Types An Overview
Welding is a crucial process in the construction and maintenance of pipelines, which are used to transport fluids such as water, oil, gas, and chemicals. The type of joint used in pipe welding can significantly impact the integrity and longevity of the pipeline. In this article, we will discuss the various types of pipe welding joints and their applications.
1. Butt Welding This is the most common type of pipe welding joint and involves joining two pipes together by melting and fusing their ends. The ends of the pipes are prepared by beveling them at a specific angle and cleaning them to remove any contaminants. The pipes are then aligned and clamped together, and a welding torch is used to melt and fuse the metal together. Butt welds are typically used in high-pressure applications and where the pipes are of equal diameter.
2. Lap Welding Lap welding involves overlapping the ends of two pipes and welding them together. This type of joint is commonly used in low-pressure applications and where the pipes have different diameters. The ends of the pipes are beveled, and the overlap is measured and marked. The pipes are then clamped together, and a welding torch is used to melt and fuse the metal together.
3. Tee Welding Tee welding is used to join a pipe to another pipe or fitting at a right angle. The tee joint is created by welding a separate piece of pipe or fitting to the end of the existing pipe The tee joint is created by welding a separate piece of pipe or fitting to the end of the existing pipe
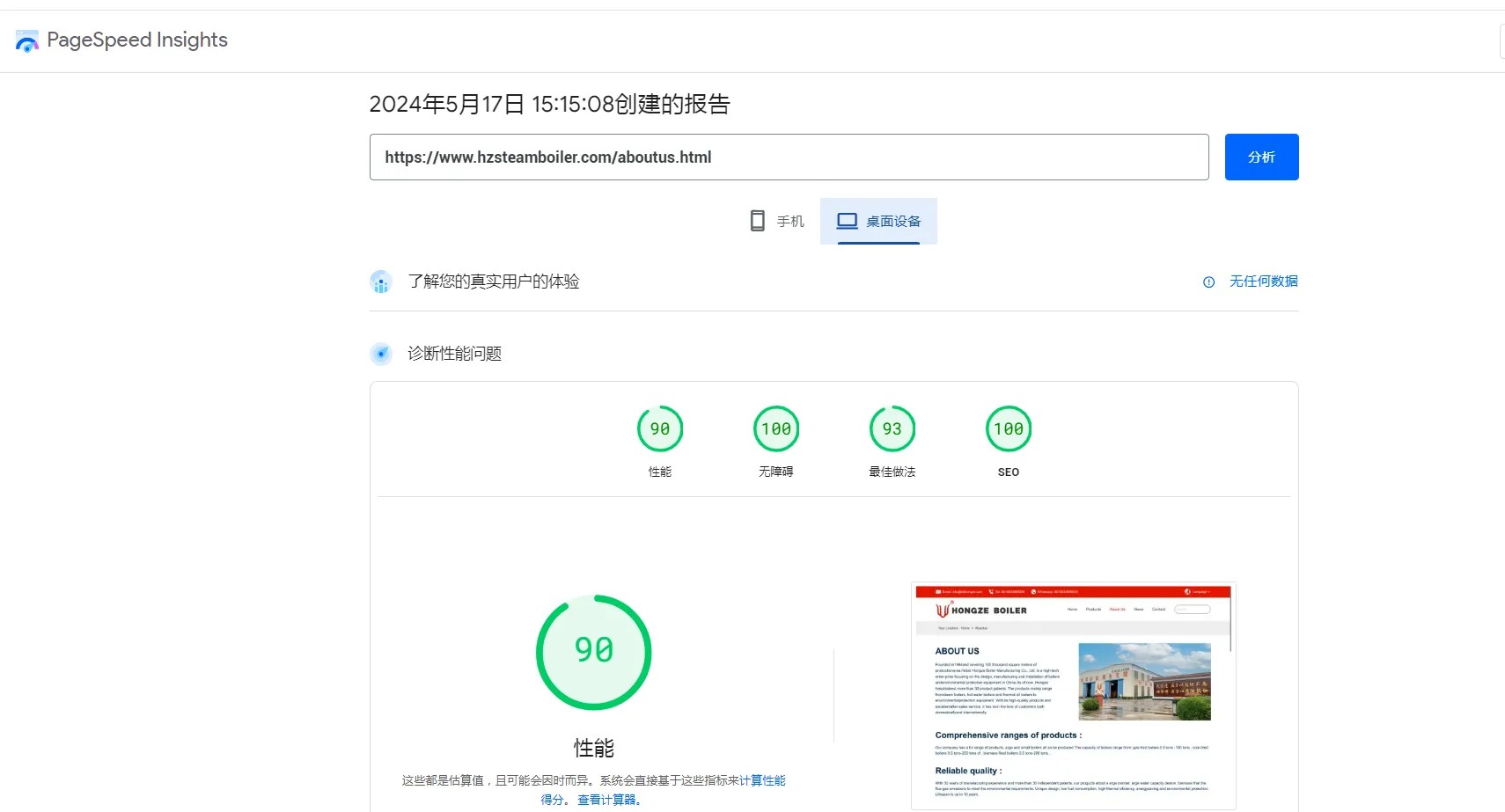
The tee joint is created by welding a separate piece of pipe or fitting to the end of the existing pipe The tee joint is created by welding a separate piece of pipe or fitting to the end of the existing pipe
pipe welding joint types. The ends of the pipes are beveled, and the tee joint is welded in place using the appropriate welding technique. Tee welds are commonly used in plumbing systems and drainage networks.
4. Corner Welding Corner welding is used to join two pipes at a 90-degree angle. This type of joint is created by welding a bracket or fitting to the end of each pipe, and then welding the brackets or fittings together. Corner welds are commonly used in structural applications and where space constraints require a compact joint.
5. Insert Welding Insert welding involves inserting a pre-made fitting into the end of a pipe and welding it in place. This type of joint is commonly used in high-pressure applications and where the pipes have different diameters. The insert is designed to withstand the pressure and provide a leak-tight seal.
In conclusion, there are several types of pipe welding joints available, each with its own unique advantages and applications. The choice of joint type depends on factors such as the pressure requirements, diameter of the pipes, and the space constraints. It is essential to select the appropriate joint type to ensure the integrity and longevity of the pipeline.