The Definitive Guide to Plain Flanges Your Go-To Resource for Industrial Excellence
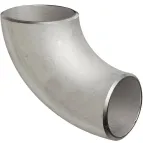
Plain flanges, an indispensable component in the vast realm of industrial applications, often go unnoticed despite their critical role in ensuring system integrity and functionality. They are the silent workhorses of piping systems across industries, from petrochemical to food processing. Understanding their application, functionality, and nuances is vital for any industry professional seeking to maintain and optimize operational efficiency.
A plain flange, at its core, is a type of flange without any raised face or additional sealing surface. This characteristic differentiates it from other flange types,
like the raised face or ring-type joint flanges. Designed primarily for low-pressure environments, plain flanges provide a flat sealing surface, which makes them suitable for gasketed joints. Their simplicity belies their utility in various non-critical applications, making them an economical choice in industries where cost-efficiency is a priority.
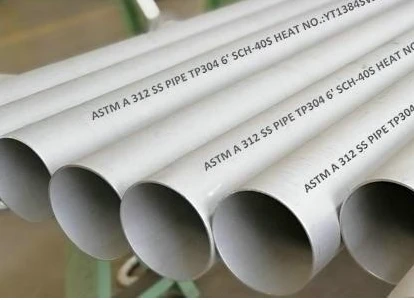
Experience suggests that the choice of a plain flange is heavily influenced by the specific requirements of the project. Considerations such as material compatibility, pressure rating, and environmental conditions are paramount. Carbon steel, stainless steel, and alloy steel are common materials used for manufacturing plain flanges, each offering distinct advantages concerning resistance to corrosion, tensile strength, and temperature tolerance.
In practice, the proper installation of plain flanges is crucial. They require precision in alignment with the mating flange to ensure an even distribution of pressure across the sealing surface. A misaligned connection could lead to uneven gasket compression, resulting in leaks and compromised system integrity. Industry experts advise regular maintenance checks, focusing on the integrity of the bolts and the condition of the gasket material to preempt any operational failures.
plain flange
Industry veterans often underscore the importance of choosing the right gasket for a plain flange. The gasket material should mirror the operational conditions, considering factors like temperature fluctuations and chemical exposure. Options range from non-asbestos materials to advanced PTFE gaskets, each offering varying degrees of resistance to degradation.
The versatility of plain flanges extends beyond their basic configuration. They can be augmented with coatings or surface finishes to enhance their performance in particularly corrosive environments. Specialized coatings, such as epoxy or phenolic, offer an additional layer of protection, mitigating the impact of aggressive chemicals and extending the service life of the flange.
Trust in plain flanges is not unfounded. Their widespread acceptance is a testament to their reliability and efficiency in non-critical applications. Authority in this domain demands a comprehensive understanding of the regulatory standards governing their use. Compliance with standards such as ANSI, ASME, and ASTM not only ensures quality but also instills confidence in the end-users that these components meet stringent industry requirements.
In summary, plain flanges are a cornerstone in industrial piping solutions, offering simplicity, cost-effectiveness, and reliable performance in suitable environments. Professionals working with these components need to draw on both theoretical knowledge and practical experience to maximize their benefits. By understanding the subtleties of material selection, installation practices, and maintenance requirements, industry professionals can uphold the highest standards of operational excellence. As is often the case with industrial components, their worth is not measured merely by their complexity, but by their ability to perform consistently and effectively under designated conditions.