Sanitary pipe welding is an essential process in industries where hygiene and cleanliness are paramount, such as food and beverage processing, pharmaceuticals, and biotechnology. This specialized form of welding ensures that pipes used in these sectors meet stringent sanitary standards to prevent contamination and maintain product purity.
Sanitary pipe welding, often referred to as orbital TIG (Tungsten Inert Gas) welding, utilizes a non-consumable tungsten electrode under an inert gas shield to create a clean, precise weld. The key aspect of this welding method is its ability to produce a smooth, mirror-like finish on the pipe's interior, eliminating any crevices or rough surfaces where bacteria could potentially accumulate.
The process begins with meticulous preparation. Pipes are cleaned thoroughly, often with specialized detergents, to remove any oil, dust, or other contaminants. Then, the pipes are polished to achieve the required surface finish, which typically ranges from 240 to 320 grit. The welding joint is designed to be seamless, with no grooves or beads that could harbor microorganisms The welding joint is designed to be seamless, with no grooves or beads that could harbor microorganisms
sanitary pipe welding.
During the welding operation, the inert gas, usually argon, is used to protect the weld area from atmospheric contamination
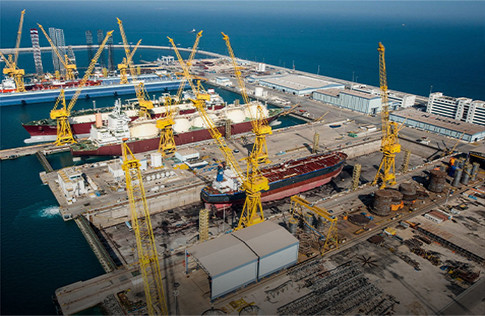
. The welder, using a computer-controlled welding machine, ensures consistent heat input and bead profile, minimizing distortion and ensuring a consistent, high-quality weld. The weld is then visually inspected and often X-rayed or tested with non-destructive testing methods to guarantee its integrity.
Sanitary pipe welding also involves strict adherence to industry-specific codes and standards, such as ASME BPE (American Society of Mechanical Engineers Bioprocessing Equipment) and 3A standards. These guidelines dictate everything from material selection to the specific welding procedures to ensure the highest level of sanitation.
In conclusion, sanitary pipe welding is not just about joining materials; it's a critical step in maintaining the safety and quality of products in hygiene-sensitive industries. It requires a high level of skill, precision, and attention to detail from both the welders and engineers involved. Continuous advancements in technology and welding techniques further enhance the efficiency and reliability of this process, ensuring that it remains a cornerstone of clean, safe manufacturing processes.