The Art and Science of Seamless and Welded Pipes
In the vast landscape of industrial manufacturing, seamless and welded pipes stand as testaments to human ingenuity and engineering prowess. These two types of pipes, while serving similar functions, embody distinct characteristics that make them uniquely suited for specific applications.
Seamless pipes, as their name suggests, are manufactured without any seams or joints. This is achieved through a process called rotary piercing, where a solid billet is pierced and then extruded into the desired pipe size. The absence of seams ensures that these pipes can withstand higher pressures and are less prone to leakage, making them ideal for applications such as oil and gas pipelines, high-pressure steam systems, and precision instruments where strength and integrity are paramount.
On the other hand, welded pipes are created by joining individual pieces of metal through welding. This method allows for greater flexibility in terms of diameter and wall thickness, enabling manufacturers to tailor pipes to specific needs. While they may not possess the same inherent strength as seamless pipes, advances in welding technology have significantly reduced the risk of failure at the joints. Welded pipes are commonly used in construction, automotive exhaust systems, and water supply lines where their adaptability is advantageous.
The choice between seamless and welded pipes often depends on the intended use, cost considerations, and safety requirements
The choice between seamless and welded pipes often depends on the intended use, cost considerations, and safety requirements
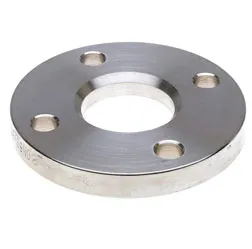
The choice between seamless and welded pipes often depends on the intended use, cost considerations, and safety requirements
The choice between seamless and welded pipes often depends on the intended use, cost considerations, and safety requirements
seamless and welded pipe. For instance, seamless pipes might be preferred for critical applications due to their superior strength and durability. However, welded pipes could be more economical for projects where weight is a concern or when large diameters are needed.
In both cases, quality control is essential to ensure that each pipe meets rigorous standards before it leaves the factory floor. Non-destructive testing methods such as ultrasonic testing and radiographic inspection are employed to detect any flaws that could compromise the pipe's performance.
As our world continues to evolve, so too does the demand for reliable piping solutions. Seamless and welded pipes represent two sides of this coin, each offering its own set of benefits that contribute to the ever-expanding tapestry of modern industry. By understanding their differences and strengths, engineers can select the most appropriate pipe for the job at hand, ensuring that their projects run smoothly and efficiently.