Understanding seamless pipe sizes is crucial for industries that rely on precision and durability. Seamless pipes, known for their strength and resilience, are used extensively across various sectors including oil and gas, construction, and manufacturing. The absence of welded seams ensures maximum pressure capacity, making them ideal for high-stakes applications.
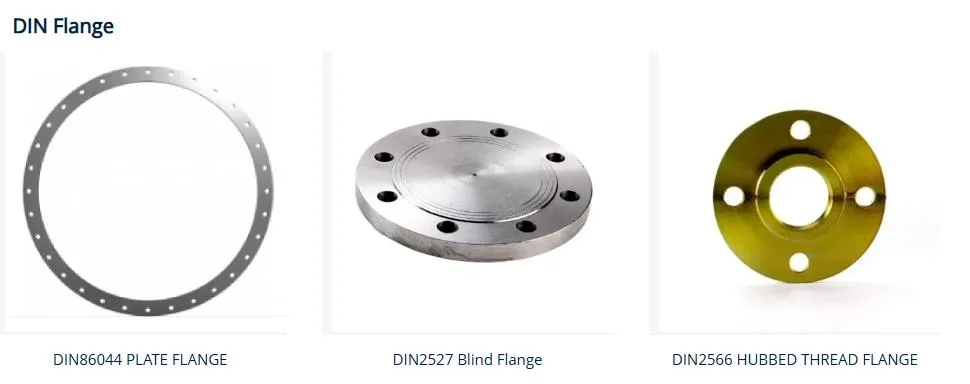
Seamless pipe sizes are classified according to specific standards, such as the ANSI/ASME B36.10 and B36.19 specifications, which define the nominal pipe size (NPS) and wall thickness, noted as schedule numbers. This classification ensures that the pipes meet rigorous industry requirements for safety and performance. For example, common nominal sizes range from 1/8 inch to 24 inches, catering to a wide spectrum of applications from small-scale machinery to large industrial systems.
In practical experience, selecting the right seamless pipe size entails considering the operational environment and the particular demands of the application. For instance, in high-temperature settings, a thicker wall (with a high schedule number like Sch 80 or Sch 160) might be necessary to withstand thermal expansion and pressure. In contrast, lower schedules (like Sch 10) suffice for less demanding conditions, offering cost efficiency without compromising integrity.
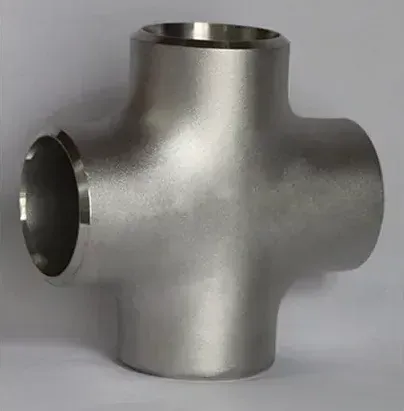
Expertise in the field underscores the importance of understanding the relationship between size, material composition, and application needs. For example, carbon steel seamless pipes are favored in environments where strength and resistance to wear and tear are paramount. Meanwhile, stainless steel variants are chosen for their superior resistance to corrosion and are often used in chemically aggressive or hygienic applications.
seamless pipe sizes
An authoritative perspective involves being informed about technological advances in seamless pipe manufacturing, such as the use of advanced thermal techniques and automation, which enhance precision in creating uniform dimensions and consistent quality across batches.
This ensures that seamless pipes not only meet but exceed stringent international standards.
Trustworthiness in providing seamless pipe solutions comes from reliably sourcing materials that trace back to reputable mills and adhering to global benchmarks for quality assurance. With traceability comes confidence; clients can trust that each pipe will perform as expected over its operational lifetime, reducing the risk of failure even in the most demanding situations.
Furthermore, emerging innovations in seamless pipe production, such as eco-friendly processes and smart technologies for real-time monitoring, are shaping the future of this industry, promising even greater efficiency and environmental responsibility. Companies investing in these innovations solidify their role as leaders in the field, influencing best practices and setting new standards.
In conclusion, a comprehensive understanding of seamless pipe sizes involves not merely knowing the dimensions but appreciating the intricacies of their application, the materials from which they are crafted, and the standards they must meet. Industries rely on seamless pipes not only for their robustness but also for their ability to conform to complex specifications that prevent downtime and optimize performance. As technology continues to evolve, so too does the potential for seamless pipes to deliver unparalleled results across diverse industrial applications.