In the realm of industrial manufacturing and engineering, seamless steel tubes hold a pivotal role due to their broad applications, including construction, automotive, and energy sectors. One crucial aspect that manufacturers and consumers meticulously consider is the size of these steel tubes, which directly impacts their performance, regulation adherence, and cost-effectiveness.
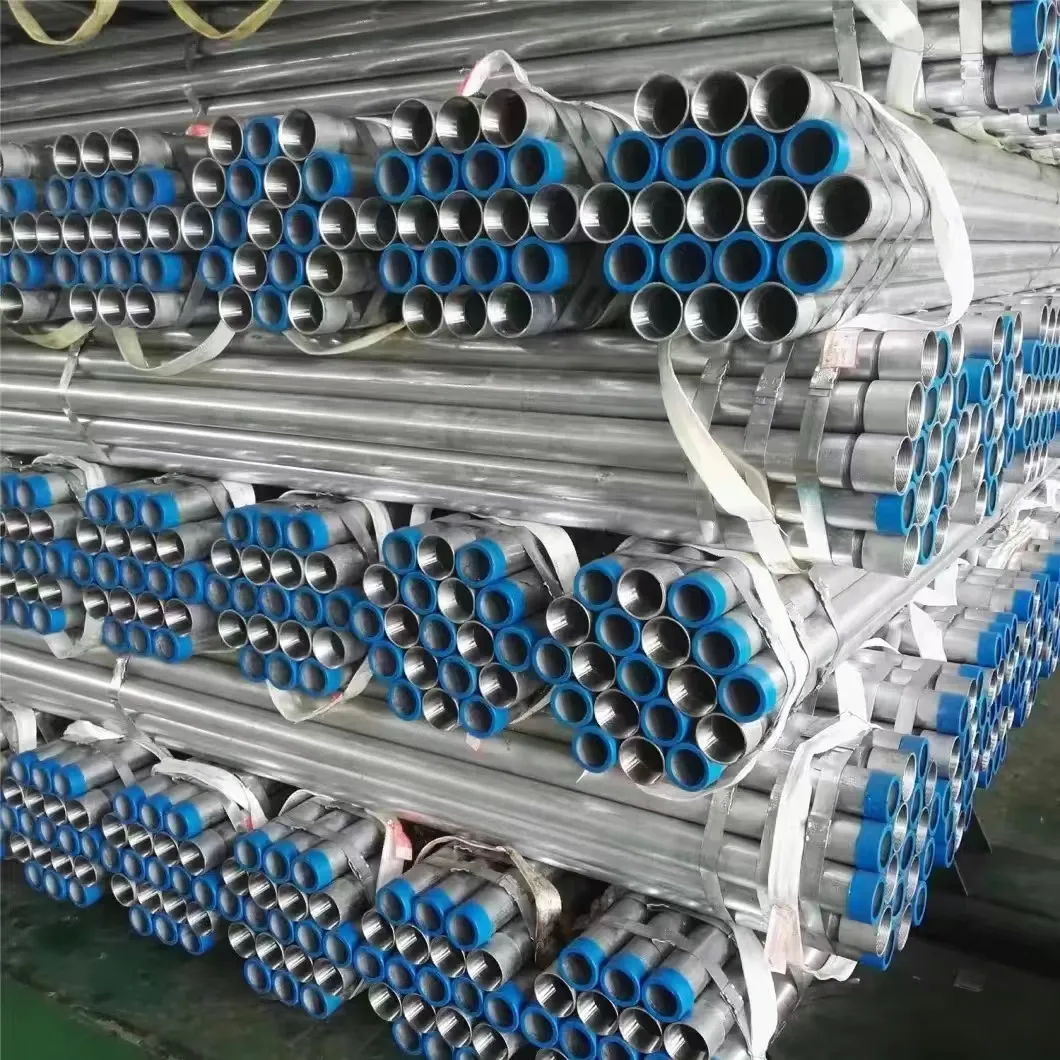
Seamless steel tubes, distinguished from welded tubes by their manufacturing process wherein a solid billet is pierced to create the tube, offer superior strength and resilience, making them ideal for high-pressure environments. However, understanding the optimal tube size for specific applications necessitates an exploration into fundamental and nuanced details regarding dimension, application, and industry standards.
To ensure optimal performance and safety,
one must select the appropriate seamless steel tube size. Typically, tube dimensions are classified by outside diameter (OD), wall thickness, and length. For example, in the automotive industry, smaller diameter tubes with thinner walls are often used for fuel lines and cooling systems, while larger diameter tubes with thicker walls may be employed in exhaust systems. The American Society for Testing and Materials (ASTM) provides global standards that aid in determining the correct specifications for seamless steel tubes, ensuring they meet both industry and safety requirements.
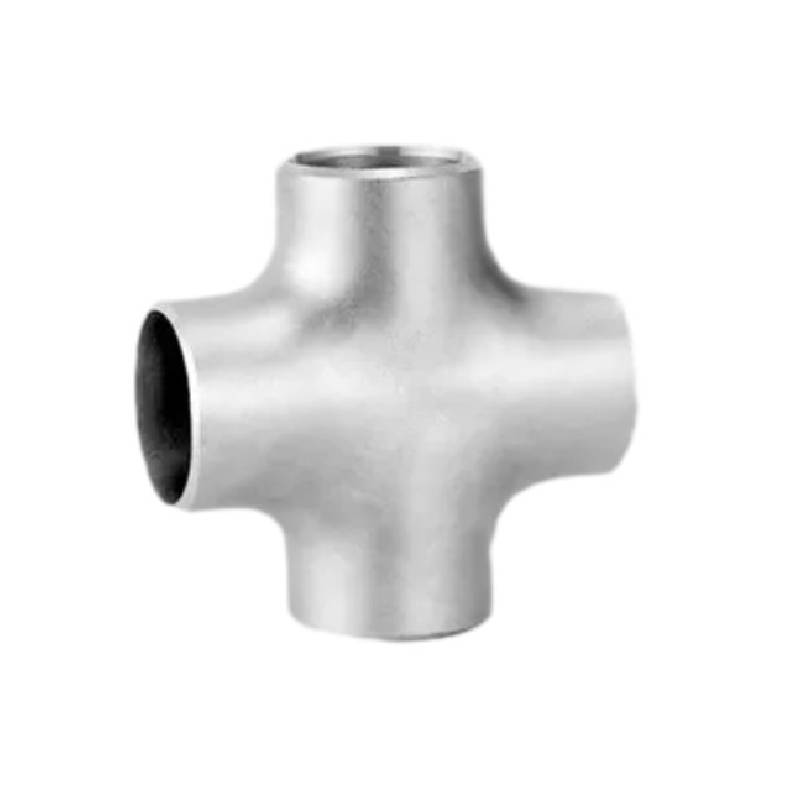
When selecting the right size of seamless steel tubes, it is essential to understand the pressure and flow requirements of the application. For high-pressure applications, such as in oil and gas industries, thicker walls and larger diameters are commonly preferred to withstand internal pressure and reduce risk of failure. Conversely, when weight is a significant concern, such as in aerospace applications, thinner walls might be desirable, provided the material's strength can guarantee structural integrity.
seamless steel tube sizes
Regulatory standards, such as ASTM or International Organization for Standardization (ISO) specifications, provide comprehensive guidelines on dimensions and tolerances for seamless steel tubes. These standards ensure consistency in quality and compatibility across different projects and geographic locations. By strictly adhering to these standards, manufacturers and consumers can mitigate risks associated with poor product performance and safety failures.
Advancements in manufacturing technologies have also influenced the availability of seamless steel tube sizes. Innovations such as cold drawing and precision rolling allow for a greater array of size options. These techniques not only diversify size choices but also enhance the material properties, such as increased tensile strength and improved surface finish, adhering to stringent industry demands.
These comprehensive considerations underscore the importance of seamless steel tube size in any engineering project. Prioritizing the correct dimension involves balancing application requirements, regulatory standards, and technological advancements. Professionals leveraging vast experience and technical expertise ensure the selection process is both informed and efficient, maximizing performance and sustaining trust with clients and stakeholders.
Understanding and selecting the accurate seamless steel tube size is an intricate process that intertwines technical expertise, regulatory knowledge, and practical application comprehension. By navigating these considerations effectively, engineers and manufacturers can bolster the reliability, efficiency, and safety of their projects, fulfilling the intricate demands of modern industrial applications.