The Art and Significance of Split Casing in Engineering Design
In the realm of engineering, the concept of split casing holds a unique position, particularly in the design of pumps, compressors, and other mechanical equipment. This technique, often employed to enhance efficiency and facilitate maintenance, is a testament to the intricate balance between functionality and practicality.
Split casing refers to a design feature where the housing or casing of a machine is divided into two or more parts, typically along a horizontal or vertical plane. This allows for easy access to the internal components without the need for extensive disassembly, thereby reducing downtime and maintenance costs. It's a design strategy that has been embraced by engineers globally due to its inherent benefits.
The idea behind split casing is rooted in the principle of modularity. By dividing the casing, manufacturers can create sections that can be individually manufactured, tested, and transported. This not only simplifies the manufacturing process but also enables the replacement of damaged parts without disturbing the entire system. In large-scale industrial applications, this can translate into significant time and cost savings.
In pumps, for instance, split casing designs enable the removal of impellers or other rotating elements without requiring the complete removal of the pump from the pipeline. This is particularly advantageous in situations where the pump is installed in a restricted or hard-to-reach area. Similarly, in compressors, split casings allow for easier cleaning, inspection, and repair of internal parts, enhancing overall operational reliability Similarly, in compressors, split casings allow for easier cleaning, inspection, and repair of internal parts, enhancing overall operational reliability
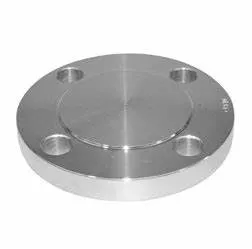
Similarly, in compressors, split casings allow for easier cleaning, inspection, and repair of internal parts, enhancing overall operational reliability Similarly, in compressors, split casings allow for easier cleaning, inspection, and repair of internal parts, enhancing overall operational reliability
split casing.
However, the implementation of split casing is not without its challenges. The design must ensure that the split does not compromise the structural integrity of the casing or introduce unnecessary stress points. Engineers need to meticulously calculate the load paths and potential stress concentrations to prevent leaks or failure under pressure.
Moreover, the precision required in the manufacturing and assembly of split casings is paramount. Even the slightest misalignment can affect the performance and lifespan of the machinery. Therefore, advanced manufacturing techniques and strict quality control processes are integral to the success of split casing design.
In conclusion, split casing is more than just a design choice; it's a strategic engineering solution that optimizes functionality, maintainability, and efficiency. Its adoption reflects the continuous quest for betterment in the industry, balancing the need for robustness with the desire for ease of use. As technology advances, we can expect even more innovative applications of split casing in the future, further pushing the boundaries of engineering design.